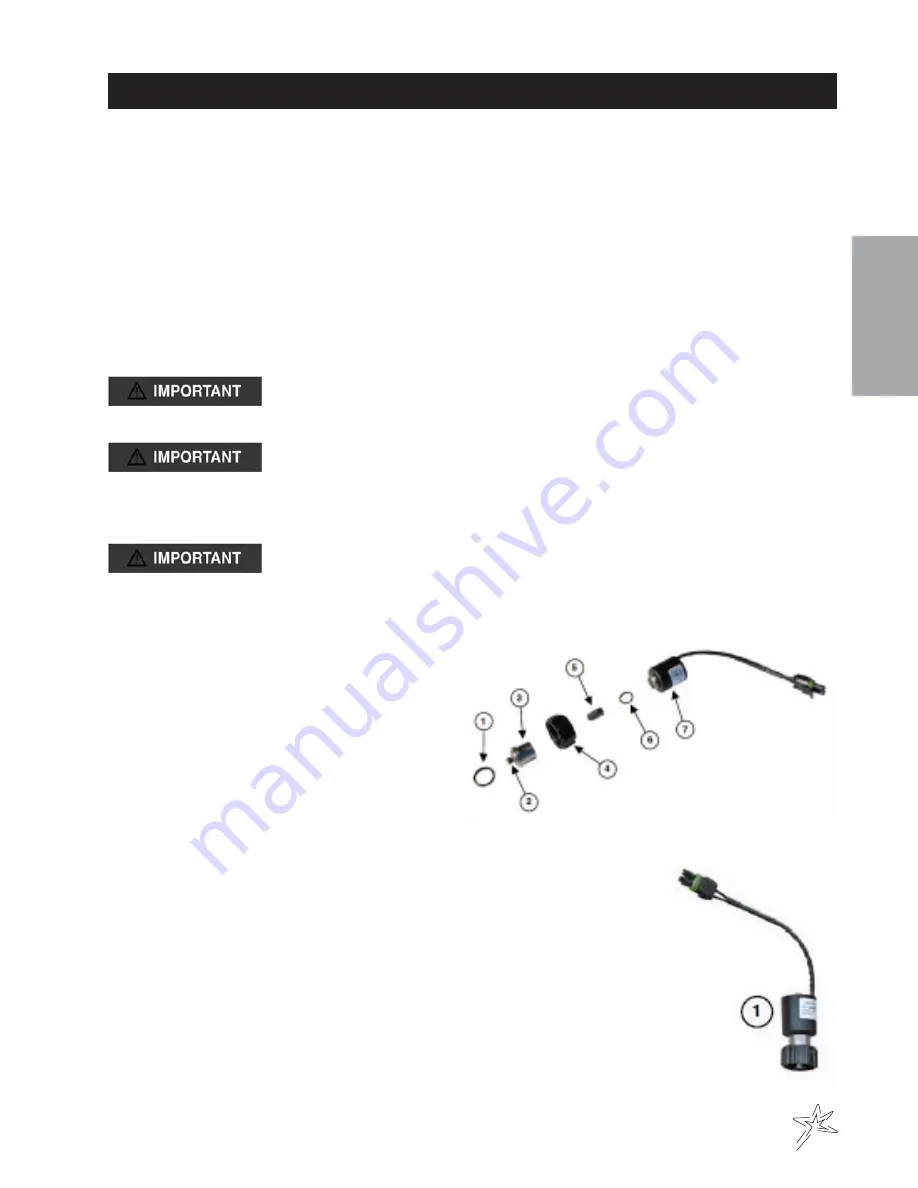
25
Operation
PARTS MANUALS AVAILABLE ONLINE AT smithco.com
TROUBLE SHOOTING NOZZLE VALVES
Plugged nozzle valves can be classified in two categories:
Plunger blockage.
Plunger stuck.
Plunger blockage results when larger debris catches between the orifice and plunger seal. This is the smallest
flow passage within the nozzle valve.
Stuck plungers result when smaller debris collects around the barrel of the plunger and binds the plunger in
place.
Symptoms of a blocked or stuck plunger are:
Constant spray.
Dripping when nozzle is shut off.
Pinched or split o-rings will also cause nozzles to drip.
Operating a plugged nozzle valve for extended periods may result in nozzle valve coil
failure. Clean plugged nozzle valves immediately.
If plugged nozzles are a frequent problem in a particular boom section, inspect the
machines boom filter screens for plugged or damaged screens. An 80 mesh screen
is recommended to prevent nozzles from plugging. Check the mesh size of the
strainers and replace if they are too coarse.
Nozzle valve component identification.
1.
O-ring
30-168-18P
2.
O-ring
30-168-20P
3.
Valve Body
30-168-26P
4.
Flynut
30-168-25P
5.
Plunger
30-168-17P
6.
O-ring
30-168-19P
7.
Coil
30-168-21P
The nozzle valve assembly (30-168-05P) screws into the nozzle bodies replacing
the standard diaphragm check valve.
1.
Complete Nozzle Valve Assembly
30-168-05P
Summary of Contents for Spray Star 3185
Page 30: ...28 Nozzle Charts ...
Page 33: ...31 NOTES ...