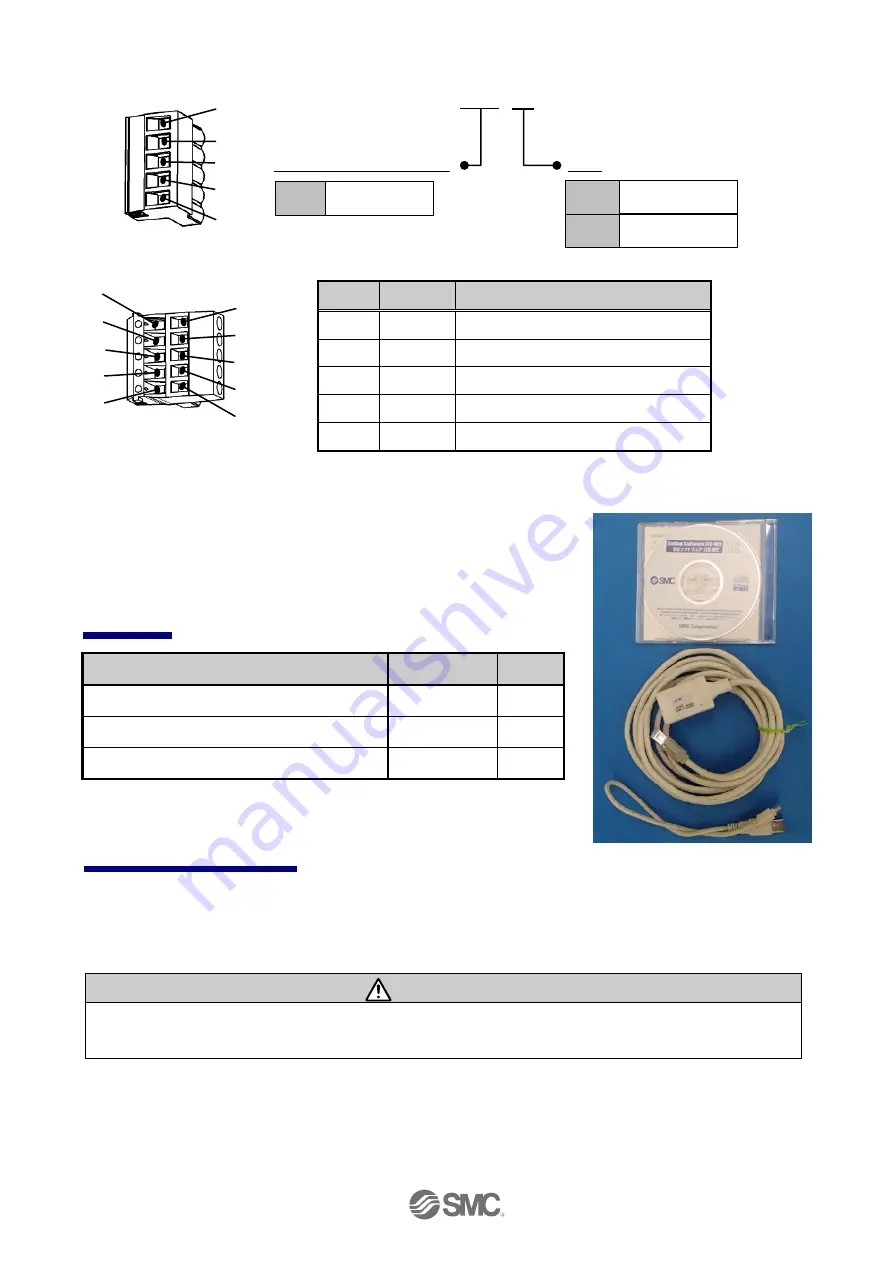
- 12 -
(5) Communication plug connector
LEC- CMJ- □
Correspondence network Type
Straight type
T-Branched type
(6) Controller setting kit
LEC- W2
Contents
*1) Can be ordered separately.
Hardware requirements
PC/AT compatible machine installed with Windows®XP and Windows®7 Windows®8.1 and equipped with
USB1.1 or USB2.0 ports.
Windows
Ⓡ
and Windows®XP, Windows®7, Windows®8.1 are registered trademarks of Microsoft Corporation.
Caution
The controller setting software must use the latest version.
Upgrade software be able to download on SMC website. http://www.smcworld.com/
No.
Name
Function
1
DA
CC-Link communication line A
2
DB
CC-Link communication line B
3
DG
CC-Link ground line
4
SLD
CC-Link shield
5
FG
Frame ground
Description
Product No.
*1
)
Quantity
(1) Controller setting software (CD-ROM)
LEC-W 2-S
1
(2) Communication cable (3m)
LEC-W 2-C
1
(3) USB cable (0.3m)
LEC-W 2-U
1
(1)
(2)
(3)
5
4
3
2
1
5
4
3
2
1
5
4
3
2
1
CC-Link
MJ
T-Branched
type
T
Straight type
S