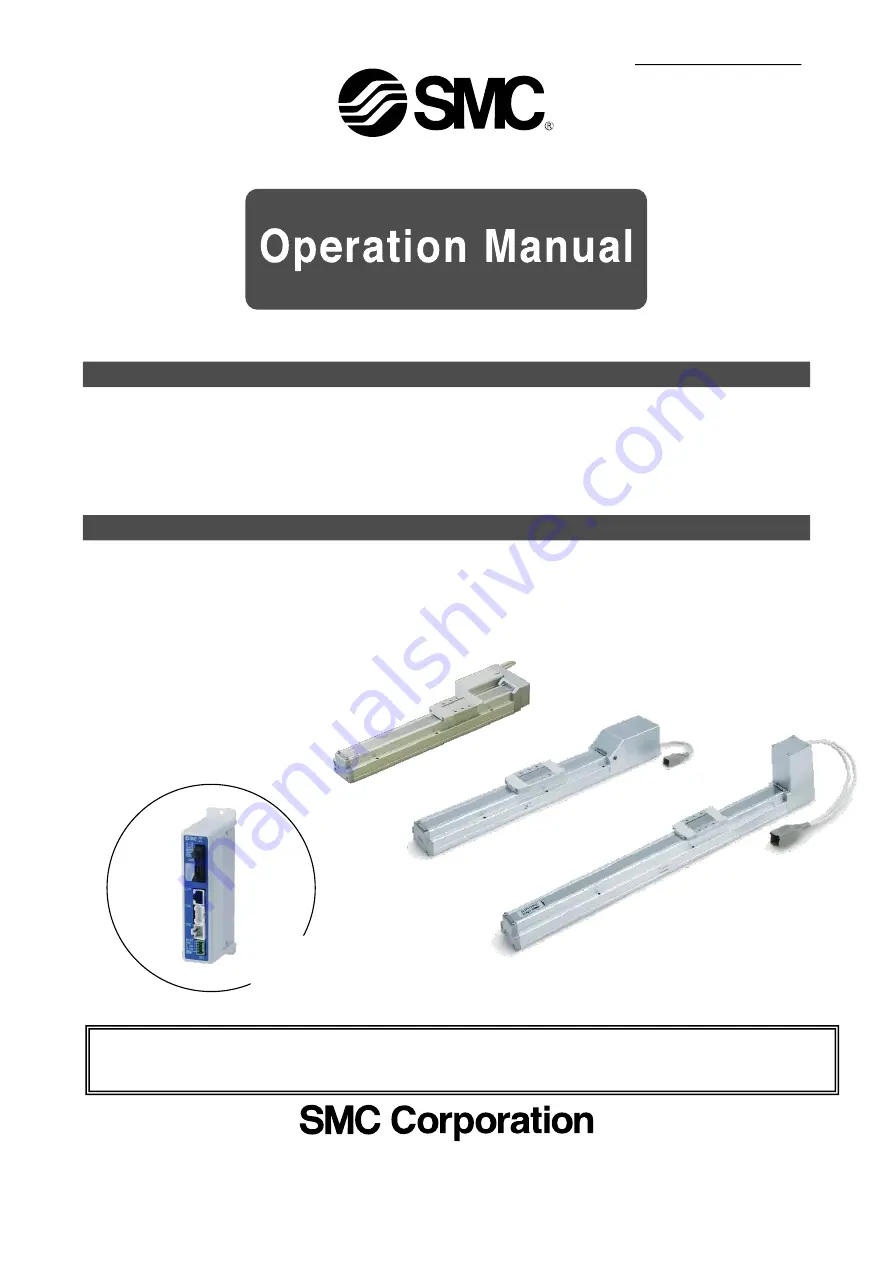
PRODUCT NAME
Electric Actuator
/
Slider Type
《
Step motor
/
Servo motor
》
MODEL / Series
LEF Series
Applicable models: LEFS, LEFB
Doc. no. LEF-OM00213
This manual describes the actuators operation in combination with the LEC*6
series controllers.
Refer to the manual relevant to the controller being used for full
operating instructions.
<Controller>
LEC Series
2021-05-20 10:32
DW913599