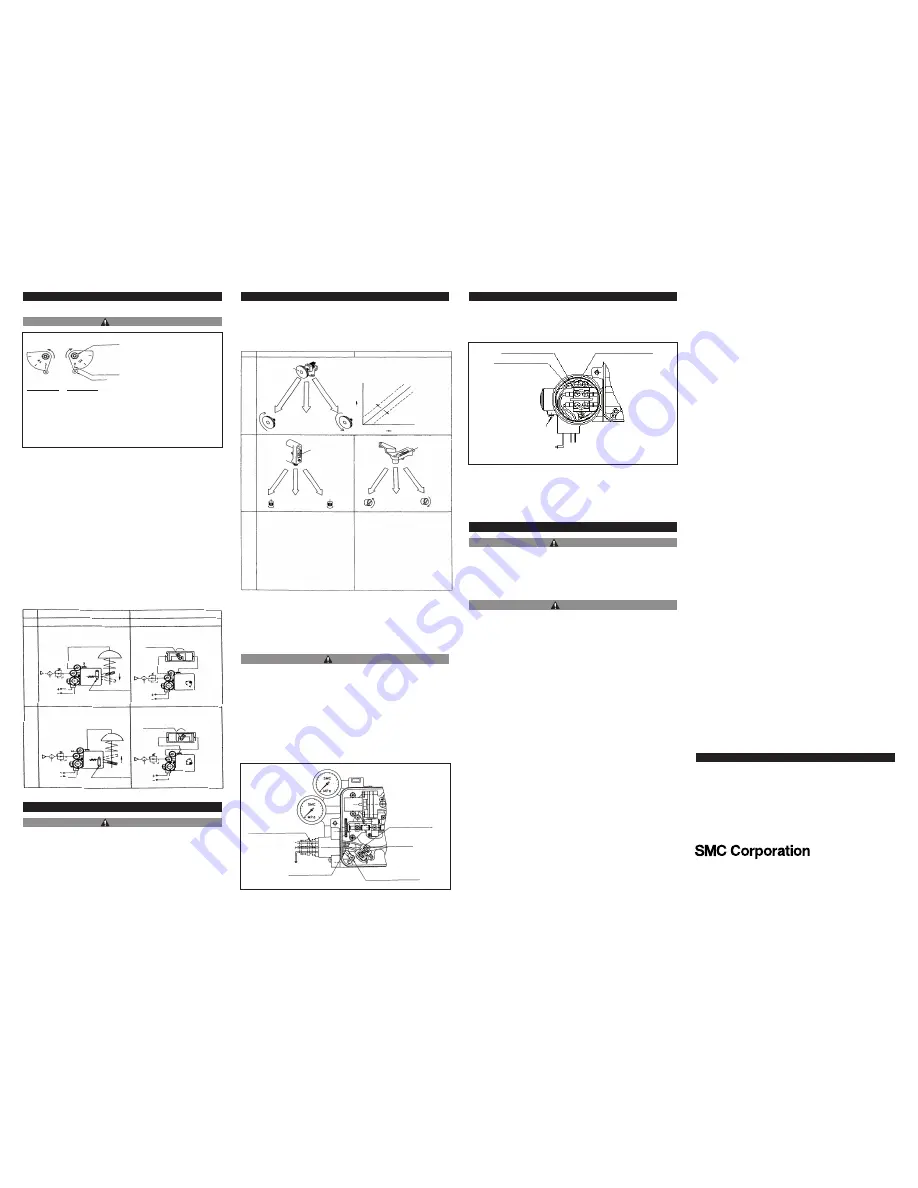
4 Mounting (Continued)
4.2.3 Cam attaching procedure
CAUTION
IP80-TFI03GB-B
Table 2
5 Adjustment
CAUTION
Check the following prior to start the adjustment.
(1) Check that the pipeline is correctly connected with the pressure
supply port and OUT1 and OUT2 ports.
(2) Check that the actuator and positioner are sturdily connected.
(3) Check that the span adjusting lever of internal feed back (Type
IP8000) is attached to the correct (normal or reverse) position.
(Refer to Tables 2.)
5 Adjustment (Continued)
(4) Check for locking of the auto/manual changeover screw of pilot valve
(fully tightened in the clockwise direction).
(5) Check for correct use of the cam face (normal or reverse) in Type
IP8100 and that the flange nut is firmly locked. (Refer to Table 2.)
(6) Check that the wires are connected correctly with the (+), (-) and
grounding terminals.
*¹ When the span adjusting screw is turned clock-wise with a slothead(-)
screwdriver, the span increases. When it is turned counter-clockwise, the
span decreases.
*² When the span adjusting screw is turned clock-wise with a slothead(-)
screwdriver, the span decreases. When it is turned counter-clockwise, the
span increases.
CAUTION
(1) For this positioner, span and zero point adjustment of each actuator is
necessary. Adjustment shall be done based on each actuator size.
(2) Keep in mind that span and zero point adjustment interfere in each
other.
(3) Characteristics changes due to change of mounting position, ambient
temperature and supply pressure.
(4) If it takes along time until the operation after initial adjustment, check
and adjust this product.
(5) Sensitive adjustment is effective for only double acting actuator.
(6) Manual change function is effective for single acting actuator which is
controlled by using OUT1.
5.1 Electrical wiring
(without terminal box)
5 Adjustment (Continued)
Connect the (+) and (-) output terminal of positioner with the (+) and (-)
input terminal of positioner respectively. The input port of the electrical
connection is equiped with a cable connector G 1/2 female.
5.2 Electrical wiring
(with terminal box)
(1) Connect the (+) and (-) output terminals from the regulator with the (+)
and (-) input terminals, respectively, of the positioner terminal box. The
port diameter at the conduction wire drawing port is the size of G1/2
parallel screw for piping and the depth is for a 16.5mm female screw.
(2) Two drawing ports, marked as Part A and Part B in Fig.14, are provided.
Use either one as fitted. (Part B is used in the figure).
6 Limitations of Use
WARNING
(1) After installation, repair and disassembly, connect compressed air and
perform a proper function test and leak test. If bleed noise is louder than
the initial state, or operation is abnormal, stop operation and check if
installation is correct or not.
CAUTION
(1) Check if supply air is clean or not. Inspect compressed air cleaning
system periodically so that dust, oil and humidity, which can cause
malfunction and failure of the unit, do not enter the equipment
(2) If handled improperly, compressed air can be dangerous. Maintenance
and replacement of unit parts should only be performed by trained and
experienced personnel for instrumentation equipment , as well as
following the product specifications.
(3) Check the positioner once a year. When an excessively worn
diaphragm, O-ring or other packing of any unit that has been damaged
is found, replace with new ones. Treatment at an early stage is
especially important if the positioner is used in a place of severe
environment, such as costal areas.
(4) Before removing the positioner for maintenance, or replacing unit parts
after installation, ensure the supply pressure is shut off and all residual
air pressure is released from the piping.
(5) When the fixed orifice is clogged with carbon particles or other material,
remove the pilot valve Auto/Manual change over screw (built in fixed
aperture) and clean it by inserting a 0.3mm diameter wire into the
aperture.
(6) When you disassemble the pilot valve, coat the O-ring of the sliding
section with grease. (Use the TORAY SILICONE SH45 grease.)
(7) Check for air leaks from the compressed air piping. Air leaks could lower
the performance characteristics of the positioner. Air is normally
discharged form a bleed port, but this is necessary air consumption
based on the construction of the positioner, and is not an abnormality if
the air consumption is within the specified range.
(1) Use the DA face of the cam to turn the
actuator main shaft clockwise (viewed from
the positioner front cover side) at the time of
input signal increase. Use the RA face to
turn it counter-clockwise (reverse actuation).
Correctly attach the cam to the flange part of
feed back shaft.
(2) Attach the cam in the procedure of
loosening the hexagonal nut with flange first,
setting the using actuatorto the starting
position and then setting the cam reference
line and the bearing contact point of span
adjusting arm unit to the matching position.
(3) Do not apply the supply pressure when attaching the cam as otherwise it is very
dangerous.
(4) When the positioner is shipped out of our plant, the cam is tentatively tightened to the
shaft. Be sure to firmly lock the cam to the lock nut [tightening torque 2.0 ~ 2.5 Nm.
Counter-
clockwise
(Reverse actuation)
Clockwise
Cam reference
Bearing
(Normal actuation)
Hex. nut with flange
Fig.9 Example of cam attaching
Single action
Re
v
erse actuation
Nor
mal actuation
Double action
IP8000 (Lever type)
IP8100 (Rotary type)
Actuation: The stem moves in the arrow
direction when the input current increases.
Actuation: The actuator main shaft turns
clockwise when the input signal increases.
Actuation: The stem moves in the arrow
direction when the input current increases.
(Reverse actuation using the normal
actuation drive unit).
Actuation: The actuator main shaft turns
counter-clockwise when the input signal
increases.
OUT 1
Span adjusting lever
normal position
IN
SUP
IN
IN
IN
OUT 1
Main shaft
Double action
actuator
The cam
should be
set to DA
surface.
Double action
actuator
Main shaft
The cam
should be
set to RA
surface.
OUT 2
OUT 1
OUT 2
OUT 2
Span adjusting lever
normal position
SUP
OUT 2: Plug
OUT 1: Plug
Span adjustment
Zero point adjustment
Type IP8000
Zero adjusting knob
Move
clockwise
Move counter-
clockwise
When the zero adjusting knob is turned clockwise,
the starting point increases. When it is turned
counter-clockwise, the starting point decreases.
Strok
e
Input current
Decrease of starting points
Increase of
starting points
Counter-
clockwise
turn
Adjusting producre
(1) Set the input current to 0% (4mADC in the
standard specification) and turn the zero adjusting
knob by hand to set it to the actuator starting point.
(2) Then set the input current to 100% (20mADC in
the standard specification) and check the actuator
stroke. At this point depending on the span is too
large or too small, loosen the lock screw and
adjust the span as shown in the illustration above.
(3) Set the input current to 0% and conduct the zero
point adjudtment, as done in Step (1) again.
(4) Repeat the above operations until the
predetermined stroke of the actuator is obtained to
the input current.
(1) Set the input current to 0% (4mADC in the
standard specification) and turn the zero adjusting
knob by hand to set it to the actuator starting point.
(2) Then set the input current to 100% (20mADC in
the standard specification) and check the actuator
stroke. At this point depending on the span is too
large or too small, loosen the lock screw and
adjust the span as shown in the illustration above.
(3) Set the input current to 0% and conduct the zero
point adjudtment, as done in Step (1) again.
(4) Repeat the above operations until the
predetermined stroke of the actuator is obtained to
the input current.
Too small star
ting point
Star
ting point OK
Too large star
ting point
to span adjustment
Span adjusting
screw
Lock screw
Span adjusting
screw
Move clockwise
Move counter-clockwise
Too large span
Spam OK
Too small span
Too large span
Spam OK
Too small span
Move counter-clockwise
Move clockwise
Type IP8100
*¹
*²
Cable connector
G1/2 female
Input current
Mini-terminal unit
Twisted wire fixing screw
M4 screw for internal
grounding terminal connection
Terminal lug
(Use twisted wire of 2.63 to 6.64mm²)
Grounding
(Use twisted wire of
0.5 to 1.5mm²)
OUT2
Fig.14 Positioner with terminal box
2-M4 screw input terminal
M4 screw for internal
grounding terminal connection
Grounding
Input current
Part B
Part A
- +
M4 screw for external
grounding terminal connection
Terminal lug
(Use twisted wire of
2.63 to 6.64mm
2)
7 Contact
URL http://www.smcworld.com (Global) http://www.smceu.com (Europe)
Specifications are subject to change without prior notice from the manufacturer.
The descriptions of products in this document may be used by other companies.
© SMC Corporation All Rights Reserved.
AUSTRIA
(43) 2262 62280
NETHERLANDS
(31) 20 531 8888
BELGIUM
(32) 3 355 1464
NORWAY
(47) 67 12 90 20
CZECH REP.
(420) 541 424 611
POLAND
(48) 22 211 9600
DENMARK
(45) 7025 2900
PORTUGAL
(351) 21 471 1880
FINLAND
(358) 207 513513
SLOVAKIA
(421) 2 444 56725
FRANCE
(33) 1 6476 1000
SLOVENIA
(386) 73 885 412
GERMANY
(49) 6103 4020
SPAIN
(34) 945 184 100
GREECE
(30) 210 271 7265
SWEDEN
(46) 8 603 1200
HUNGARY
(36) 23 511 390
SWITZERLAND
(41) 52 396 3131
IRELAND
(353) 1 403 9000
UNITED KINGDOM
(44) 1908 563888
ITALY
(39) 02 92711