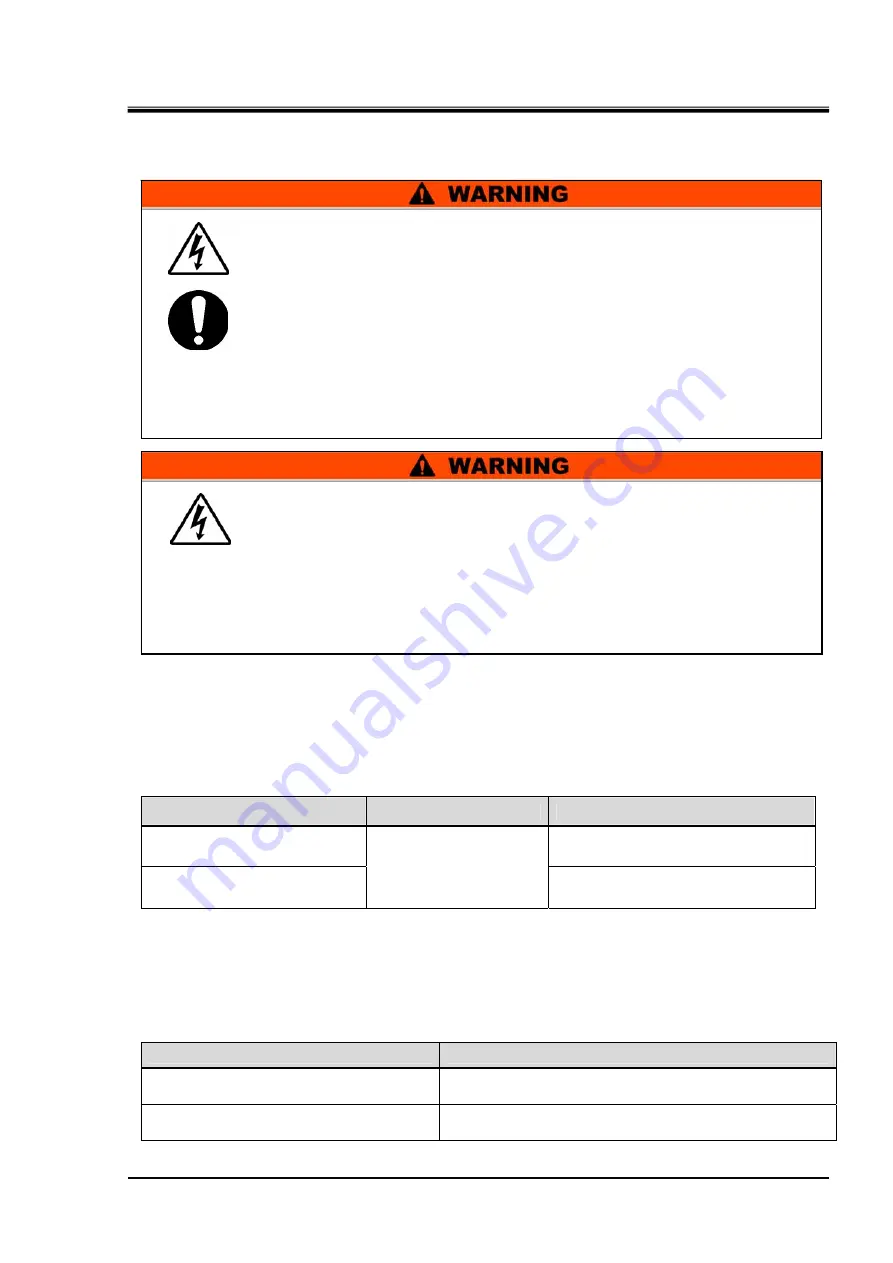
HEC-OM-O018-A
Chapter 3 Transporting and Installation
3.3 Wiring
3-5
3.3 Wiring
3.3.1
Power Sourse Specification
Confirm that the power supply at your workplace
has sufficient capacity and
a voltage within that specified. It is recommended to install ground-fault
circuit interrupter. Rated leakage current:30mA or less.
Table 3-2 Electrical specifications of power supply
Model Number
Voltage
Rated Current
INR-244-733/-745
3.5A(at 100VAC)~1.5A (at 240VAC)
INR-244-734/-736/-746/
-747/-748/-749
Single Phase
100VAC~/-10%
(Over Voltage Category
I or II)
5.5A(at 100VAC)~2.5A (at 240VAC)
3.3.2
Power Supply Cable and Connector
The power cable and connecter are to be prepared under your responsibility,
referring to the following table.
Power supply Cable
Table 3-3 Power Supply Cable and Connector
Cable and Connector
Types (for your system)
Cable
3 wires, thicker than 14AWG, includes ground.
Power Supply Connector
IEC60320 C-13 equivalent
10A cable mount female connector
z
Only qualified personal are allowed to install wiring.
z
Be sure to turn OFF the power prior to wiring to assure safety.
Do not do any wiring when the system is energized.
z
The system wiring requires not only a through connection with the
designated cable but also securing to prevent loose connection.
Poor connection and securing may cause electric shock, heat spots,
fire, or communication errors.
z
Be sure to supply the power to this product according to the
specification.
z
Always establish a connection to a ground for safety.
z
Be sure that no ground connection is made to a water pipe, gas pipe
and lighting rod.
z
Be sure to provide protective ground. IEC protection
class of the product is class I. Be sure to provide protective
ground (ground resistance of 100
Ω
or less). Grounding can be
provided via the PE line of the power supply cable. For details
of the power supply cable, refer to page 3-5, Power Supply
Cable and Connector
z
Do not use the same ground being used by equipment
that generates strong electrical magnetic noise or high
frequencies