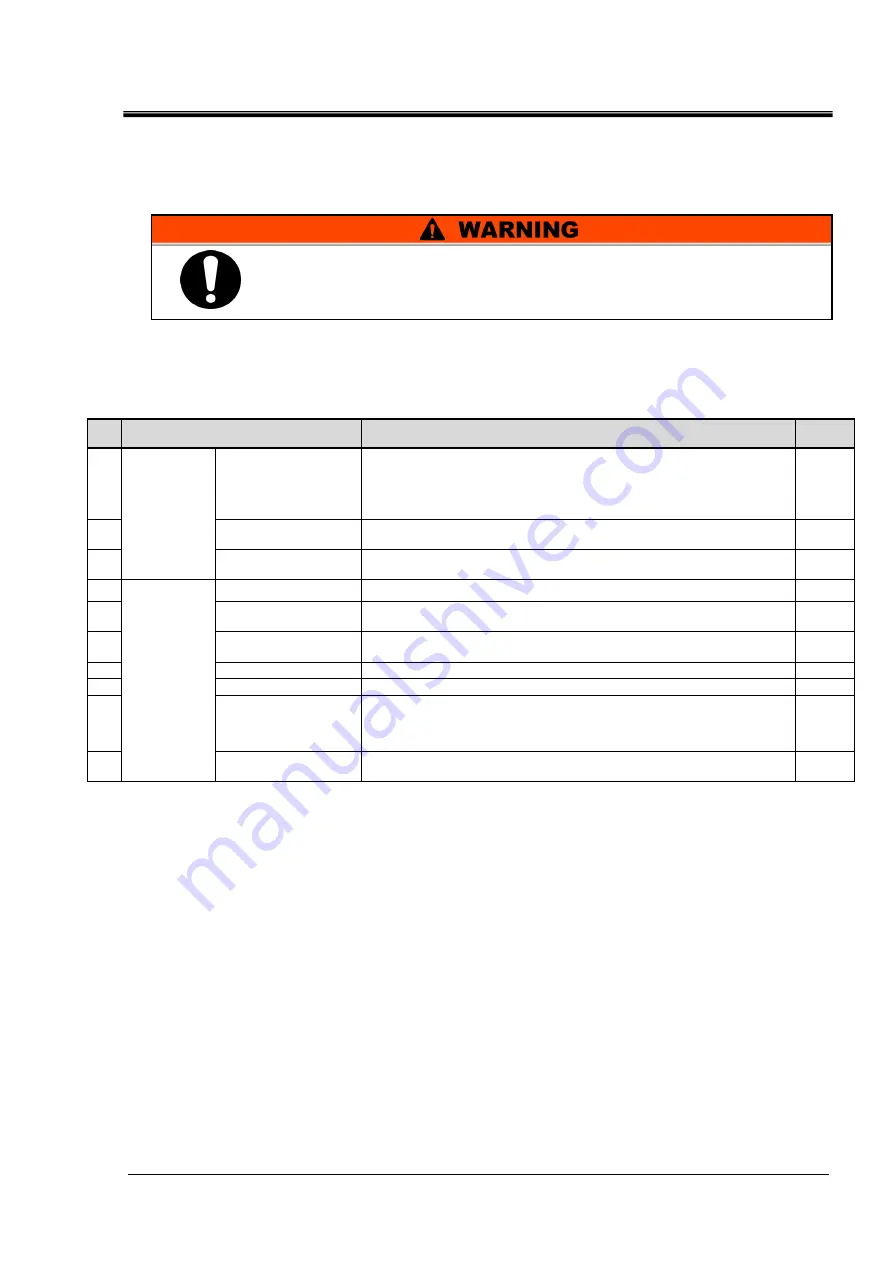
HRX-OM-X084
Chapter 5 Display and Setting of Various Functions
HRR Series
5.1 List of Functions
5-1
Chapter 5 Display and Setting of
Various Functions
5.1 List of Functions
The product can have the displays and settings shown in Table 5-1.
Table 5-1
List of functions
Read and understand this manual carefully before changing the
settings.
No.
Outline
Reference
page
1
Main menu
Displays the current temperature and set temperature of circulating fluid.
Change circulating fluid setting temperature.Set the pump output (option T1 only).
By pressing the [
▲
] [
▼
] key, circulating fluid return temperature,
circulating fluid discharge pressure, circulating fluid flow rate(except option Z, Z1),
pump output setting (option T1 only), electric conductivity (option DM only) are displayed.
5.4.2
2
Alarm display menu
When an alarm occurs, the alarm number is displayed.
Only the currently occurring alarms are displayed.
5.4.3
3
Maintenance notification menu
Notification function of maintenance time. When pump, fan, refrigerator,
dustproof filter, DI filter is replaced, it is displayed.
5.4.4
4
Monitor Menu
Displays the temperature of the freezing circuit, pressure and ambient temperature.
5.5.2
5
Standard setting menu
Set various setting values such as key lock, alarm buzzer sound,
offset temperature, electric conductivity set value (in option DM).
5.5.3
6
Alarm setting menu
It sets the validity / invalidity of various alarms, switches WRN (operation continuation) /
FLT (operation stop), and changes the alarm set value.
5.5.4
7
Communication setting menu
Set contact input / output and serial communication.
5.5.5
8
Reset menu
Initialize the setting data and reset the maintenance time.
5.5.6
9
Information monitor menu
The model and program version of this product are displayed.
Displays the operation cumulative time, pump operation cumulative time,
cumulative freezer operation cumulative time, fan operation cumulative time,
dust filter use time, and DI filter usage time for this product.
5.5.7
10
Alarm history menu
The alarm number that occurred in the past and the operation total time when
an alarm occurred are displayed. (Up to 150 records will be recorded.)
5.5.8
Item
Basic setting mode
Advanced setting
mode
Summary of Contents for HRR010-A-10 Series
Page 14: ...HRX OM X084 Chapter 1 Safety Instructions 1 8 Material Safety Data Sheet MSDS HRR Series 1 8...
Page 46: ...HRX OM X084 Chapter 3 Transport and Setting Up 3 5 Fill of circulating fluid HRR Series 3 24...
Page 120: ...HRX OM X084 Chapter 6 Option 6 5 Option Z HRR Series 6 6...
Page 165: ......