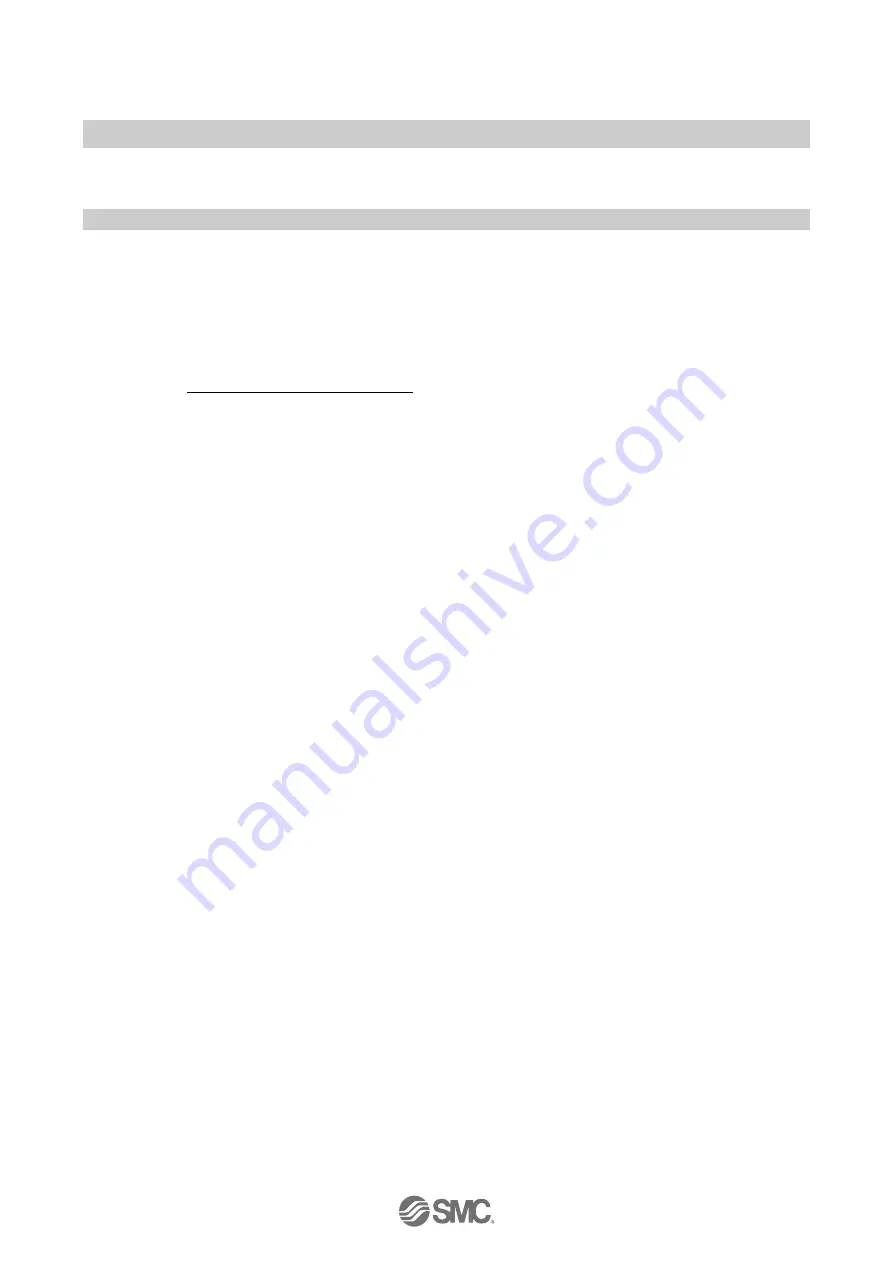
-5-
No.D-
※
S-OMJ0004-E
Cylinders or actuators include cylinders, air grippers, rotary actuators, and electrical actuators/cylinders.
Design/Selection
1. Confirm the specifications.
If the product is used with excess load applied or beyond the specification range, this may cause the product to break
or malfunction. We do not guarantee against any damage if the product is used outside of the specification range.
2. Pay attention to the length of time that a switch is ON at an intermediate stroke position.
When an auto switch is placed at an intermediate position of the stroke and a load is driven at the time the piston
passes, the auto switch will operate, but the operating time will be short if the speed is too fast. As a result, the load
may not operate completely. The maximum detectable piston speed is:
V[mm/s] =
Auto switch operating range [mm]
×1000
Time load applied [ms]
3. Take precautions when multiple cylinders/ actuators are used close together.
When multiple auto switch cylinders/actuators are used in close proximity, magnetic field interference may cause the
auto switches to malfunction. Maintain a minimum cylinder separation of 40 mm. (When the allowable interval is
specified for each cylinder series, use the indicated value.)
The auto switches may malfunction due to the interference from the magnetic fields.
Use of a magnetic screen plate (MU-S025) or commercially available magnetic screen tape can reduce the interference
of magnetic force.
4. Ensure sufficient clearance for maintenance activities.
When designing an application, be certain to allow sufficient clearance for maintenance.
5. Do not mount the cylinder or actuator with the auto switch on a footing.
If work personnel gets on or
puts the work personnel’s foot on the footing accidentally, an excessive load is applied to
the cylinder or actuator, causing the cylinder or actuator to break.
6. Design the circuit so that any back-flow current does not flow in if a short-circuit trouble occurs or forced
operation is performed to check the operation.
If a back-flow current occurs, this may cause the switch to malfunction or break.
7. When multiple auto switches are required.
“n” indicates the number of auto switches which can be physically mounted on the cylinders/actuators. Detection
intervals depends on the auto switch mounting structure and set position, therefore some required interval and set
positions may not be available.
8. Limitations on detectable position
There are positions or surfaces (bottom surface of the foot bracket, etc.) where the auto switch cannot be mounted due
to the physical interference depending on the cylinder or actuator mounting status or mounting bracket. Select an
appropriate auto switch setting position where the auto switch does not interfere with the cylinder or actuator mounting
bracket (trunnion or reinforcing ring) after checking it sufficiently.
9. Keep wiring as short as possible.
Be sure to use a wire length of 100 m or less.
When the wire length is long, we recommend the ferrite core is attached to the both ends of the cable to prevent excess
noise. A contact protection box is not necessary for solid state switches due to the nature of this product construction.
10. Do not use a load that generates surge voltage.
If driving a load such as a relay that generates a surge voltage, use a built-in surge absorbing element type device.
11. Pay attention to the internal voltage drop of the auto switch.
Generally, the internal voltage drop of the solid state auto switch is larger than that of the reed auto switch. When the
auto switches (“n” pcs.) are connected in series, the voltage drop is multiplied by “n”. In this case, the auto switches
operate correctly, but the loads may not operate. Additionally, note that the 12 VDC relay does not apply to the auto
switch.