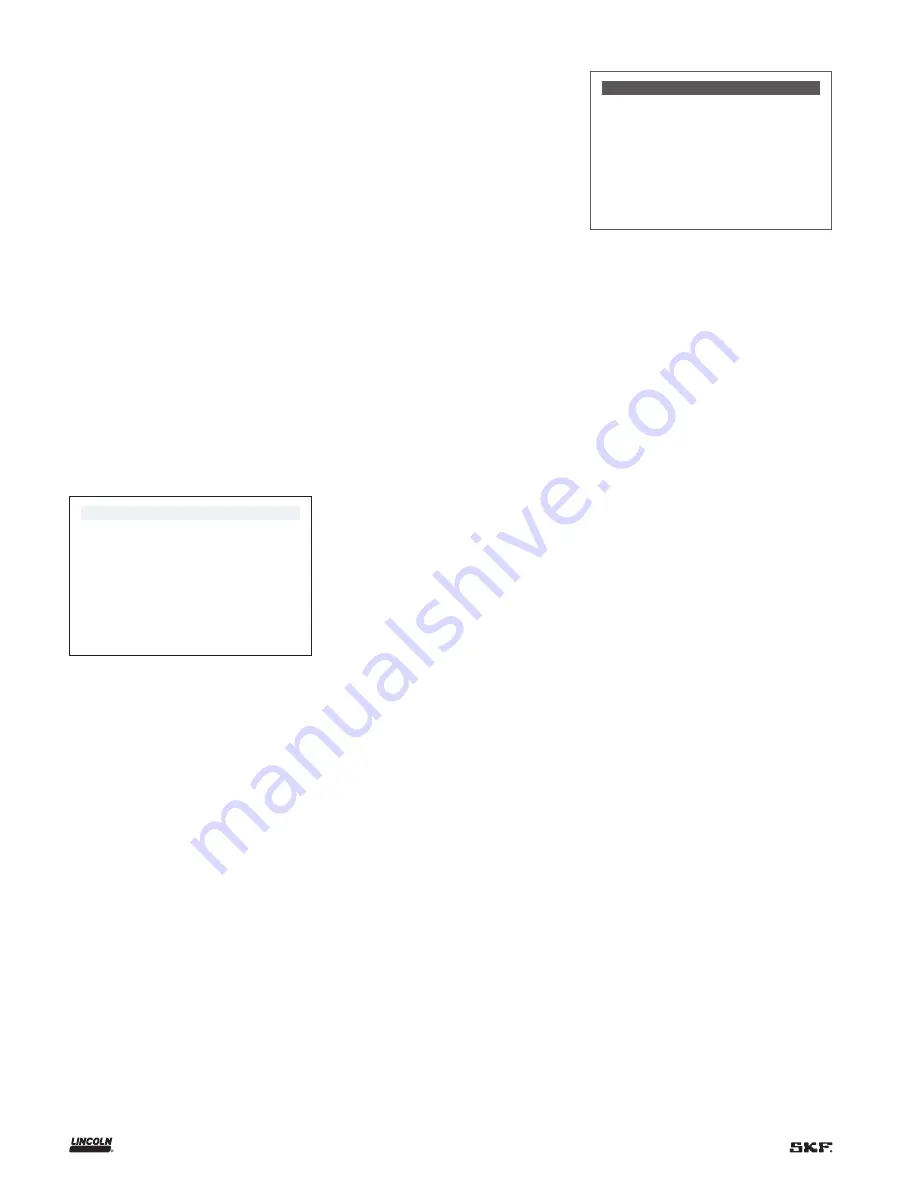
Assembly
instructions
Assemble unit as shown in diagrams.
Read and understand all warnings and
directions in component manuals.
1
Remove cover nut from top of pump. Lift air
motor cover from pump.
2
Remove four screws holding cover-bottom
to pump outlet body.
3
Hold pump with pump outlet body resting
securely on inner surface of cover-
bottom. Insert end of pump tube
through hole in drum cover. Line up
holes in drum cover, cover-bottom and
pump outlet body.
4
Replace four screws and tighten securely.
5
Push insert through follower with small cone
of wiper body facing up. Place insert
retainer over insert and align holes on
insert and insert retainer. Secure
assembly with four self-tapping screws.
6
Remove drum top and insert follower into
drum against surface of lubricant.
7
Guide end of pump tube into follower insert.
8
Lower pump tube into lubricant drum until
drum cover rests on top bead drum.
9
Assemble lubricant hose to pump outlet
body. Connections must be leak proof.
10
Place cover over air motor and position over
cover-bottom.
11
Replace cover nut on pump stud to hold air
motor cover securely in place.
12
Assemble nipple and adapter through hole in
side of air motor cover and into air
motor. Connection must be leak proof.
13
Connect air coupler to an air hose of
sufficient length so lubrigun can be used
to cover entire lubrication area.
Typical system
hookup
1
Determine drum or pail system for
requirement.
2
Obtain air line filter/regulator/lubricator to
use with inlet air supply.
3
Clean supply lines, hoses, reducers,
connectors and accessories of matter
that could damage pump or system
components. Clean/flush pump with
mineral spirits or solvents if necessary.
4
Assemble cleaned pump and supply line
together with any required accessory.
5
Mount assembled pump to drum or pail.
6
Connect material output line/hose to pump.
Connect air regulator to pump.
7
Make sure all connections are securely
tightened.
NOTE
Pump was tested in lightweight oil and was
left in to prevent corrosion.
Flush pump before connecting to system
to prevent possible contamination of grease
being pumped.
WARNING
Do not exceed 90 psi (
6 bar
) air pressure to
pump when using whip hoses.
Accessory item whip hoses for dispensing
valve are rated at 4 500 psi (
310 bar
).
Failure to comply may result in serious
injury or damage to equipment.
4