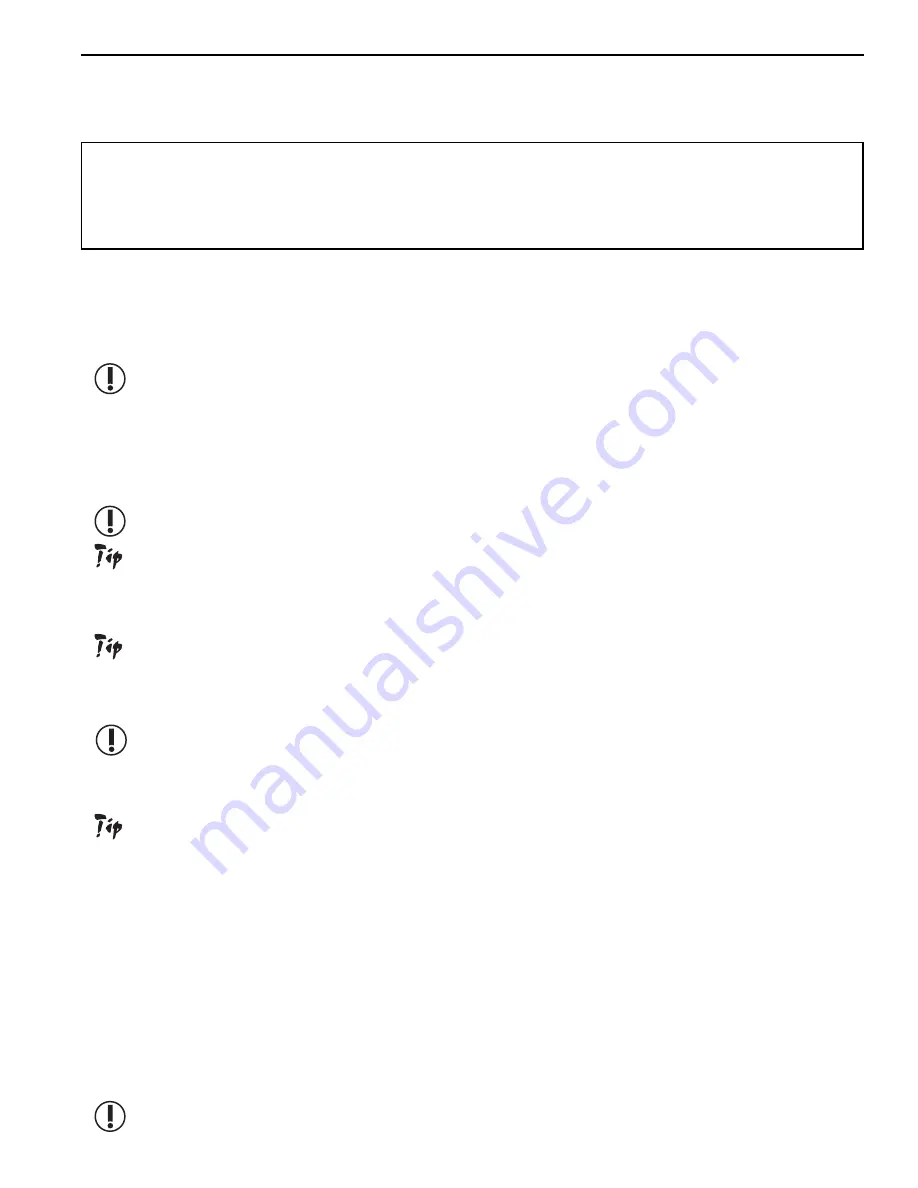
Universal Pump Service Manual
11
11
11
11
11
Pump Reassembly
Tools
• Universal XR Series pump (disassembled)
• Pliers
•
Dual-ball rotameter,
valve,
• Phillips head screwdriver
• Needle nose pliers
magnehelic gauge connected
• Small fl at-head screwdriver
• Thin wooden stick
with tubing in line and in order
• Small Allen wrench
(popsicle stick)
Reassembling and Replacing the Stack
1. Insert the yoke/diaphragm into the pump housing. Ensure that the opening in the yoke is properly placed to
allow the motor to be installed (Figure 7) and that the oval-shaped O-rings are still in place at the air passages
(Figure 2, #12).
2. Gently push the motor with the soldered wires facing outward into the pump housing until it is bo omed.
Ensure the motor is centered in the yoke/diaphragm before pushing it in (Figure 7).
3. Set the top valve plate assembly on top of the pump housing ensuring that the diaphragm fi ts into the recessed
area in the valve plate. This will help keep the diaphragm centered.
4. Gently press the yoke/diaphragm parallel against the motor counterweight (Figure 7). Once the yoke/diaphragm
has aligned itself with the face of the motor counterweight, press down on the valve plate, replace the short screw
in the top screw hole fi rst, and then replace remaining 4 screws. Tighten the screws in an alternating fashion.
Ensure that the short screw is placed in the top screw hole (Figure 2, #13).
The yoke/diaphragm assembly must be perfectly parallel to the motor counterweight. If it is not, it can cause the motor
to bind (Figure 7).
5. Replace the bo om valve plate assembly. Ensure that the components are aligned properly.
Ensure that the diaphragm is fi " ed into the recessed area in the valve plate.
.
6. Replace the short screw in the top screw hole fi rst, and then replace the remaining four screws on the bo om valve
plate. Tighten in an alternating fashion.
Ensure that the short screw is placed in the top screw hole (Figure 2, #13).
7. Reassemble the top half stack (two pulsation dampener assemblies and regulator assembly). Ensure that
components are aligned properly (Figure 2).
Do not assemble components O-ring to O-ring.
8. Using a small Allen wrench, tighten the set screw on each side of the pump housing (Figure 8, #14). Turn on
the pump to ensure that the motor runs properly. If it does not, loosen the set screw on each side of the pump
housing and use pliers to carefully back the motor out slightly. Also check that the valve plates are installed
properly. Retest the motor. If it still does not run, ensure the set screws are loosened and remove it. Turn on the
pump and slowly reinsert the running motor until it stops. This will help to determine where the motor is binding.
9. Align the two long screws (Figure 2, #11) in the top half stack with screw holes on top of the bo om half stack.
10. Tighten screws.
11. Using needle nose pliers, grip the cable connector on the new keypad interface ribbon and insert it into the plug
on the board.
Not applicable to 44XR model.
12. From inside the case, insert the top of the keypad through the slot at the bo om of the front case (Figure 3).
Not
applicable to 44XR model.
13. Reseat the control board, reinsert screws (one screw in 44XR model) into the back of the control board, and tighten
(Figure 4).
Ensure that a washer is underneath each screw head before tightening them.