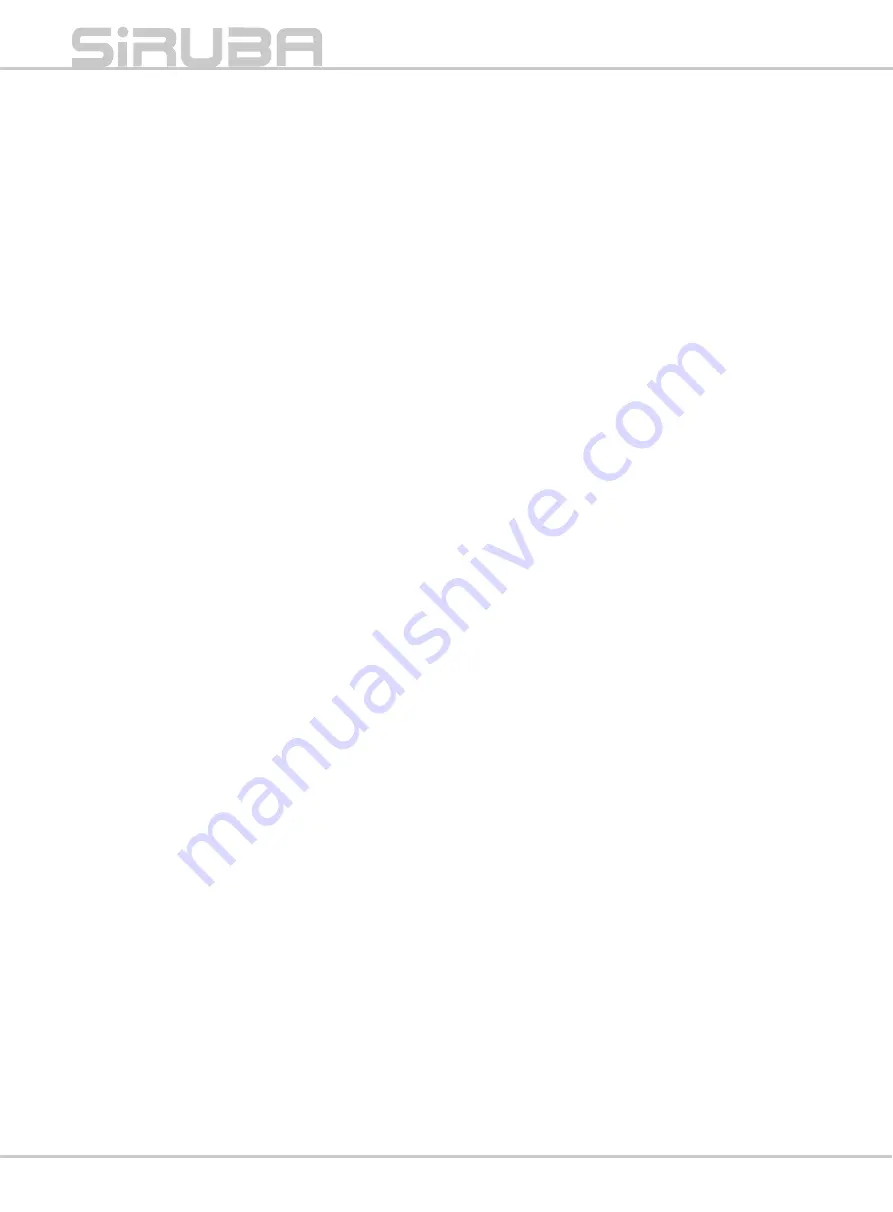
8.
中斷機器電源
當不使用機器時、維修前、以及更換配件
時。
9.
避免誤啟動
不要以手指置於啟動開關上之後,搬運一個
已插入電源的工具。確定在插電之前,電源
開關是關閉的。
10.
檢查損害零件
在進一步使用器具之前,應該小心檢查並
確認損傷的零件或是穿戴保護器具來確認
零件會正確運轉並且呈現應有功能。
11.
警告
除了在這本使用說明手冊中建議的功能之
外,任何附件或是配件的使用,都可能會
導致個人傷害的危險。
12.
由合格人員來修理器具
所以修理工作應由合格的人員使用原始個
別零件來作修理。
連接電源的特別警示
!
1.
只可與有
"CE"
認證的按壓啟動裝置連接這
台機器。
2.
遵守此使用說明手冊來安裝控制裝置。
3.
在操作過程中,永遠保持機器適當的接地。
4.
在調整、更換零件、或是維修保養之前,必
須確定將插頭由插座拔出,以預防任何機器
意料之外的啟動而造成危害。
8. Disconnect machine
When not in use, before servicing and
when changing accessories.
9. Avoid unintentional starting
Do not carry a plug-in tool with a finger on
the switch. Ensure the power switch is off
when plugging in.
10. Check damaged parts
Before further use of the tool, a guard or
other part that is damaged should be
carefully checked to determine that it will
operate properly and perform its intended
function.
11. Warning
The use of any accessory or attachment,
other than those recommended in this
instruction manual, may present a risk of
personal injury.
12. Have your tool repaired by a
qualified person
Repairs should only be carried out by
qualified persons using original spare
parts.
SPECIAL WARNING FOR ELECTRIC
CONNECTION!
1. Incorporate this machine only with "CE"
certificate hold-to-run control device.
2. Follow the instruction manual device to
install control device.
3. Always earth machine appropriately
during operation.
4. Before adjustment, parts change or
servicing must be sure to pull out the plug
from socket to prevent the hazard of
unintentionally start of machine.
P2
Summary of Contents for HF008A
Page 1: ...HF008A INSTRUCTIONS BOOK PARTS LIST...
Page 2: ......
Page 26: ...P22...
Page 27: ...P23...
Page 28: ...P24...
Page 29: ...P25...
Page 30: ...P26...
Page 31: ...P27...
Page 32: ...P28...
Page 33: ...P29...
Page 34: ...P30...
Page 35: ...P31...
Page 36: ...P32...
Page 37: ...P33...
Page 38: ...P34...
Page 39: ...P35...
Page 40: ...P36...
Page 41: ...P37...
Page 42: ...P38...
Page 43: ...P39...
Page 44: ...P40...
Page 45: ...P41...
Page 46: ...P42...
Page 47: ...P43...
Page 48: ...P44...
Page 49: ...P45...
Page 50: ...P46...
Page 51: ...P47...
Page 52: ...P48...
Page 53: ...P49...
Page 54: ...P50...
Page 55: ...P51...
Page 56: ...P52...
Page 57: ...P53...
Page 58: ...HF008A HWL P54...
Page 59: ...HF008A HWL P55...
Page 60: ...HF008A FBQ P56...
Page 61: ...HF008A FBQ P57...
Page 62: ...HF008A FBQ P58...
Page 63: ...HF008A FBQ P59...
Page 64: ...HF008A FBQ P60...
Page 65: ...P61...
Page 66: ...P62...
Page 67: ...P63...