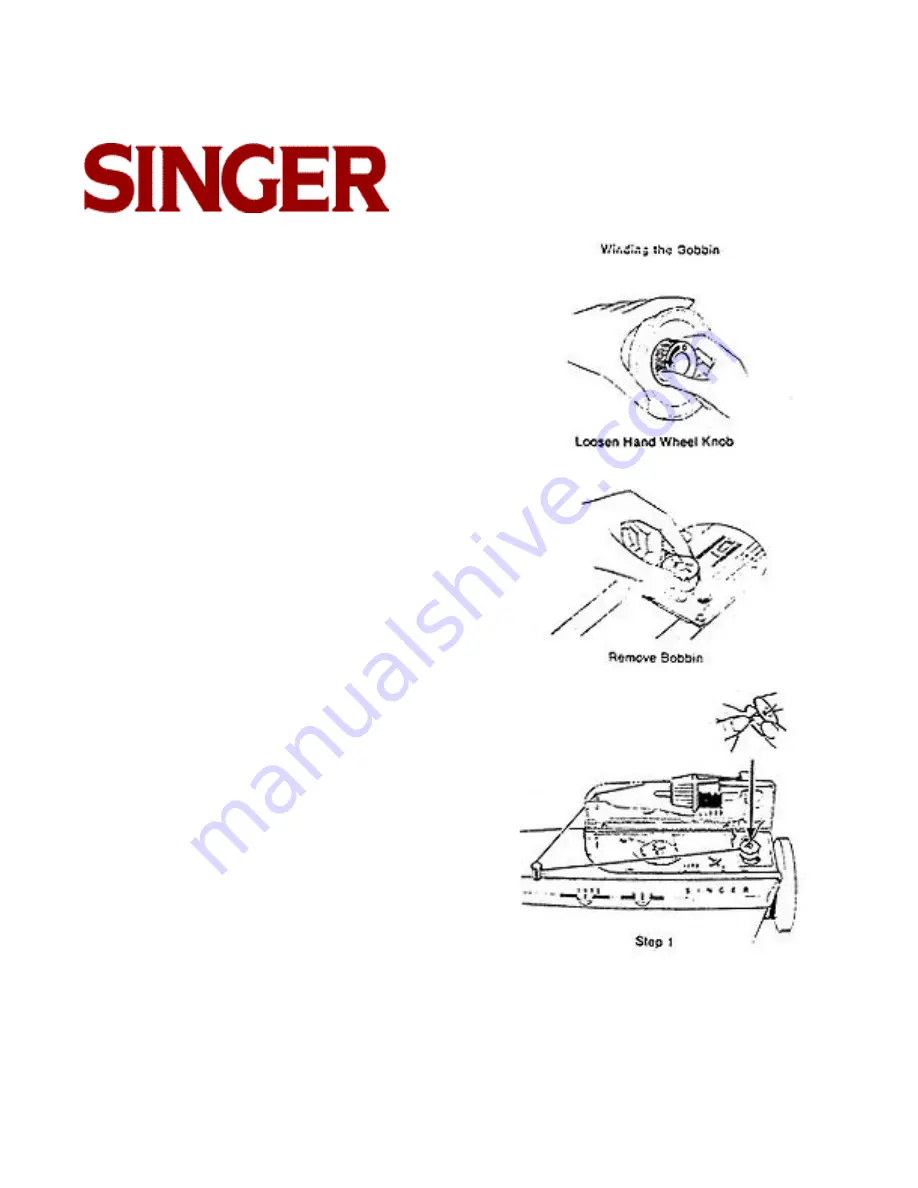
Singer
288
14
WINDING THE BOBBIN
It is best that you wind the bobbin before you thread
the needle.
Preparation:
• Raise pattern disc lid.
• Turn hand wheel toward you until needle is at its
highest position.
• Loosen the hand wheel knob with your right hand
while holding the hand wheel with your left hand.
• Open the slide plate and lift out bobbin.
Procedure
1. Place spool of thread on spool pin. Lead thread
around the bobbin-winder tension disc and through
small hole in bobbin (from inside out). Place bobbin
on spindle.