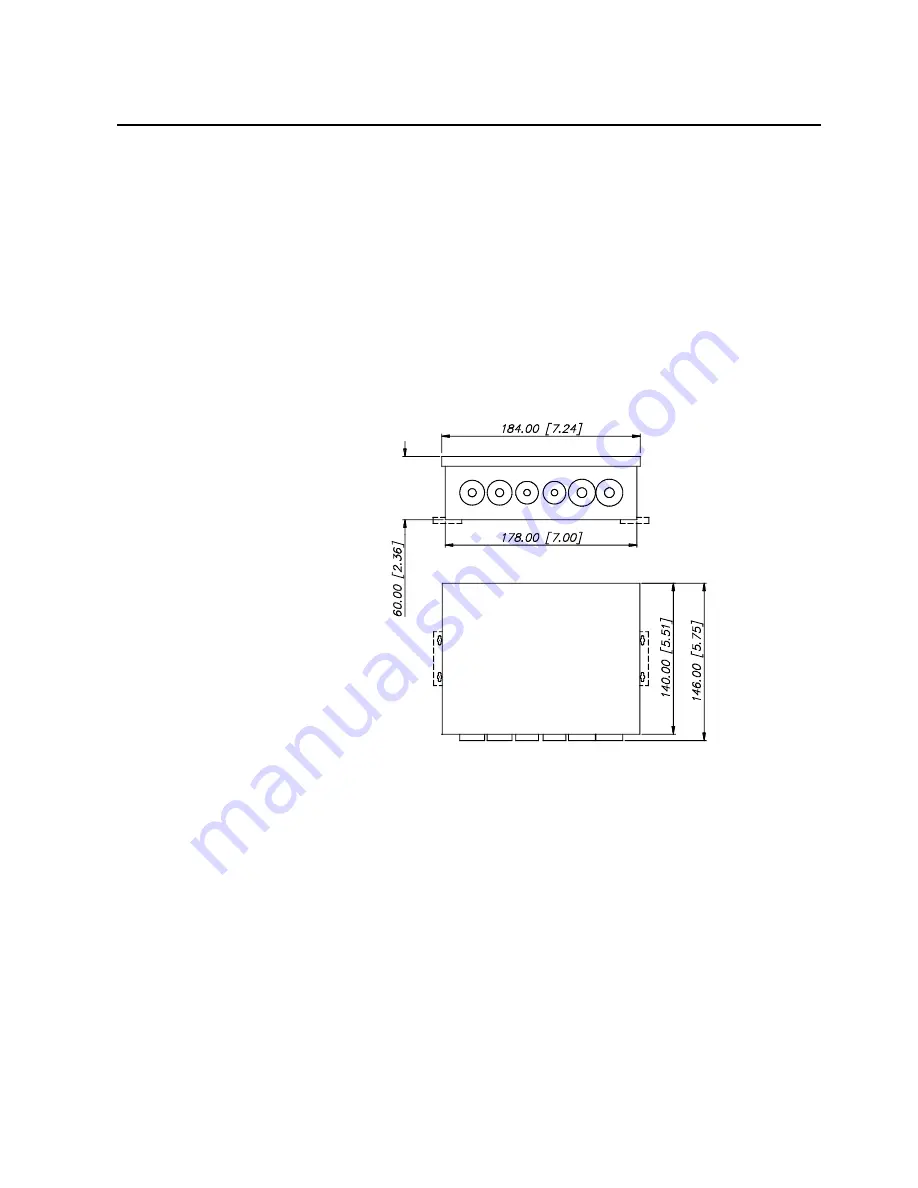
Page 4-4
Robertson AP45 Autopilot
Technical specifications
Simrad Robertson AS
Egersund - Norway
Dimensions: ................................................See Fig. 4-4
Signals in ....................................................- 6 step/degree with positive or
negative common
- Synchro signal, 90:1 or 360:1, gyro
excitated
- SKR80/82 current loop (9600 Baud)
Signal level in:............................................- Stepper signal: 20 - 70V DC
- Synchro signal: 40 - 115V, 50 - 400Hz
Load:............................................................Maximum 20mA
Supply voltage: ...........................................12V DC (autopilot supplied)
Power Consumption: ..................................2.4 W
Ambient temperature, storage: ............–25 - +70°C
operation: ........ 0 - +55°C
Fig. 4-4
G40A Gyro Interface - dimensions
Dimensions: ................................................See Fig. 4-8
Signals in
- Synchro signal, 1:1
Signal level in (S1, S2, S3):........................- High voltage, 80V L-L
- Low voltage, 11,6V L-L
Signal out (Synchro excitation): ................26V 400 Hz, max 5 VA
Supply voltage: ...........................................12V DC (autopilot supplied)
Ambient temperature, storage: ............–25 - +70°C
operation: ........ 0 - +55°C
G40A Gyro Interface
G45 Gyro Interface
Summary of Contents for ROBERTSON AP45
Page 1: ...INSTRUCTION MANUAL Robertson AP45 Autopilot 20220042 6 02...
Page 2: ...This page is intentionally left blank...
Page 6: ...Robertson AP45 Modification record Simrad Robertson AS Egersund Norway...
Page 32: ...Page 2 18 Robertson AP45 Autopilot Operation Simrad Robertson AS Egersund Norway...
Page 66: ...Page 5 16 Robertson AP45 Autopilot Installation Simrad Robertson AS Egersund Norway...
Page 88: ...Page 5 38 Robertson AP45 Autopilot Installation Simrad Robertson AS Egersund Norway...