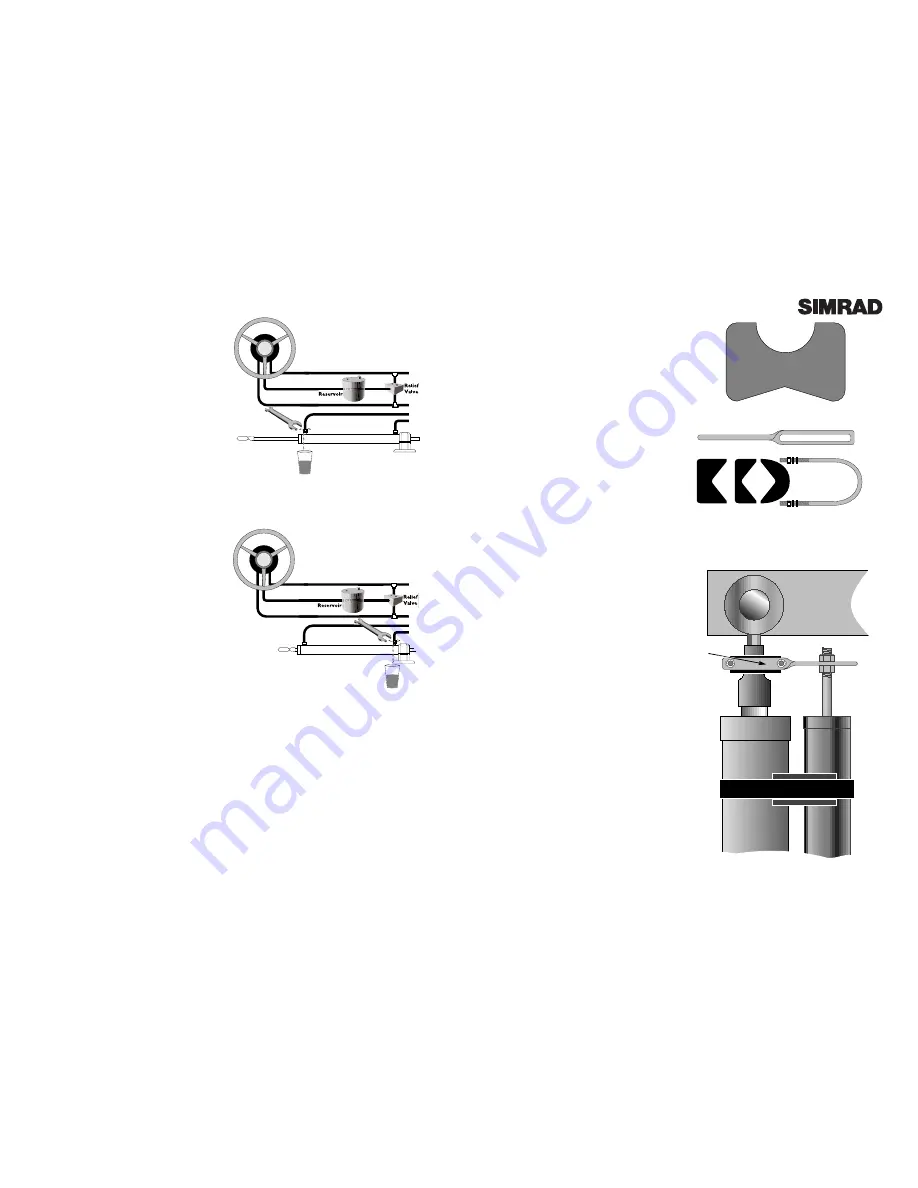
Page 19
Page 18
voir is kept topped up while doing this.
NOTE
- Running the pump dry for more than a few
seconds can damage it. The hoses running to
the pump must be primed by following steps
6 to 9.
13. After completing the cycle with each helm
position to the lowest position (including the
SRP12 pump) loosen the bleed valves (or the
hose fittings if there are no bleed valves) on the
ram cylinder one at a time, allowing air to bleed
out until a steady stream of oil comes out of the
bleeder with no air bubbles. Drain at least
1
⁄
2
litre
(1 pint) of oil to ensure all air is purged from the
system. Retighten the bleed valve.
14. Check the reservoir level. If it is less than
half full, depressurise the system, remove the
filler cap and top up the oil level. Pressurise the
system until the manufacturer’s recommended
pressure is reached.
15. Repeat steps 10 to 14, turning each helm in
the opposite direction.
16. Retighten the two relief valve screws.
17. Turn one of the helms hard over.
18. Open the bleed valve/fitting on the ram
cylinder at the end that the ram is
extended
from. Bleed until there is a steady stream of oil
with no air bubbles (Fig 4.9). Retighten the
bleed valve.
19. Turn the helm hard over in the opposite
direction. Repeat step 18, opening the opposite
bleed valve this time (Fig 4.10).
20. Check the reservoir fluid level - leave reser-
voir
1
⁄
2
to
2
⁄
3
full.
21. Pressurise the system until the manufactur-
er’s recommended pressure is reached.
22. The manufacturer’s instructions should
give details of the correct number of turns lock
to lock when the system is properly bled. An
excessive number of turns indicates that there is
still air in the system.
Fig 4.9 - Bleeding first hydraulic line
Fig 4.10 - Bleeding second hydraulic line
Fig 4.13 - Ram mounting using fixing kit
4.3 Linear Feedback Unit SLF12
The Linear Feedback Unit SLF12 measures the
rudder position and can be installed on most
types of boat, including I/O or Outboard dri-
ves. It is important that the SLF12 is properly
installed with the maximum possible stroke
(minimum 150mm [6.0 in]), or it will not give an
accurate reading.
The SLF12 is mounted onto the hydraulic ram
cylinder using two mounting saddles (Fig 4.11).
Make sure that the maximum stroke of the
hydraulic ram is less than the 300 mm (12.0 in)
maximum stroke of the SLF12. The saddles
support the SLF12 body, and can then be posi-
tioned on the back of the ram cylinder. Check
that the SLF12 and ram are exactly parallel.
Use the cable ties supplied to secure the SLF12
and saddles onto the ram.
The SLF12 rod is attached to the ram using the
fixing kit supplied (Fig 4.12). Fit the U-bolt and
bracket to the ram, checking that it will not
interfere with the movement of the ram at any
point of steering. Rotate the assembly until the
SLF12 rod can be fixed to the slot in the bracket
using the two nuts supplied (Fig 4.13)
Refer to
section 6.3 before tightening the nuts.
When satisfied with the positioning, tighten the
U-Bolt nuts fully, and then turn the helm hard
over from lock to lock, checking that the SLF12
rod does not bend at any time - this means that
the SLF12 is not exactly parallel to the ram, and
should be adjusted accordingly.
If the SLF12 cannot be fixed to the ram as
described, an accessory kit is available separate-
ly (part
LFK500
) which can be ordered through
your local Simrad agent. This contains a sepa-
rate mounting foot and balljoint assembly for
the end of the feedback rod, allowing the SLF12
to be independently fixed to the rudder arm.
•
Do not fix the SLF12 directly to the rudder
arm if it is attached to the ram using the
mounting saddles, as the feedback rod will
bend when the rudder is at full lock.
• If connecting to a Teleflex HC5345 steering
cylinder the optional LFKSeastar kit should
be ordered.
FIg 4.11 - Mounting saddles (x 2)
Fig 4.12 - Fixing kit
Rudder Arm
Ram Cylinder
Cable Tie
SLF12
Fixing
Kit
Summary of Contents for AP14
Page 1: ...Manual Simrad AP14 Autopilot ...
Page 22: ......