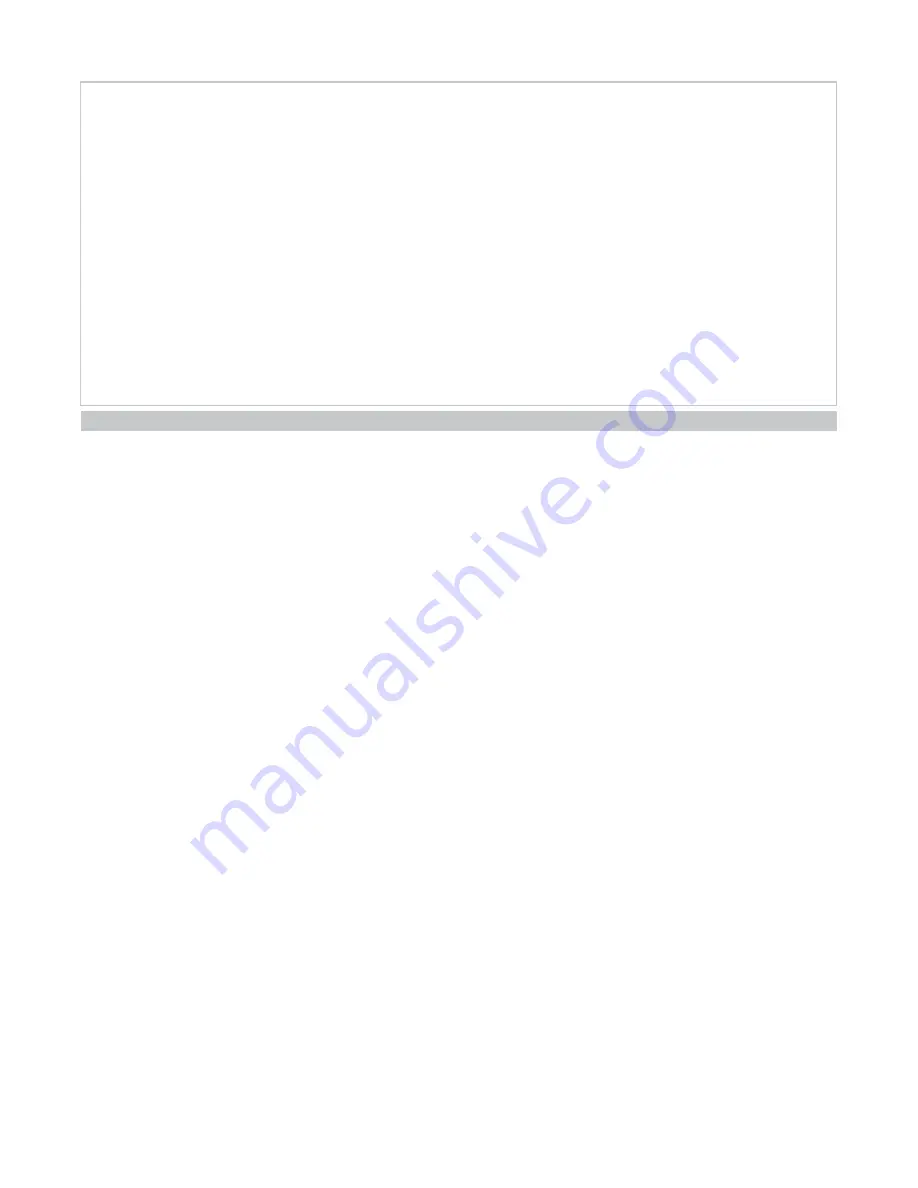
VI. Figures
A. Correct Handle Installation ................................................................ 4
B. PCB Layout and Belt Idler Assembly................................................. 5
C. Location of Nozzle Cover Screws ..................................................... 6
D. Agitator/Brushroll Assembly .............................................................. 8
E. Belt Placement .................................................................................. 9
F. Clean Air Motor Wiring ..................................................................... 12
G. Ametek Clean Air Motor Wiring ....................................................... 12
H. Clean Air Motor Placement ............................................................. 12
I. Handle to Body Harness Connector ................................................. 19
J. Location of Winged Rocker Switch .................................................. 22
K. Location of Micro Switch ................................................................. 22
L. Proper Position for Tools Activation Dial/Rotational Valve Handle ... 23
M. Agitator/brushroll Jam Screw - FBI Screw Position ........................ 27
N. Handle Assembly ............................................................................ 30
O. Body Assembly ............................................................................... 31
P. Nozzle Assembly ............................................................................. 32
Q. Handle Wiring ................................................................................. 33
R. Main Body Wire Harness .5 and .6 Models ..................................... 34
S. Main Body Wire Harness .4 and Older Models ............................... 35
T. Description of Vacuum ..................................................................... 36
IMPORTANT SAFETY INSTRUCTIONS
When using or servicing any electrical appliance, basic precautions should always be
followed, including the following:
WARNING: To reduce the risk of fire, electrical shock, or injury:
1. Do not leave vacuum unattended when plugged in. Unplug from outlet when not in use.
2. Turn off all controls before unplugging.
3. Do not attempt to service vacuum while plugged in.
4. Before handling PC board, discharge static electricity by using anti-static mat and
ground strap. If anti-static mat is not available, touch a metal object that is grounded and
only handle PC board by outside edges.
WARNING:
ELECTRIC SHOCK COULD OCCUR IF USED OUTDOORS OR ON WET SURFACES.