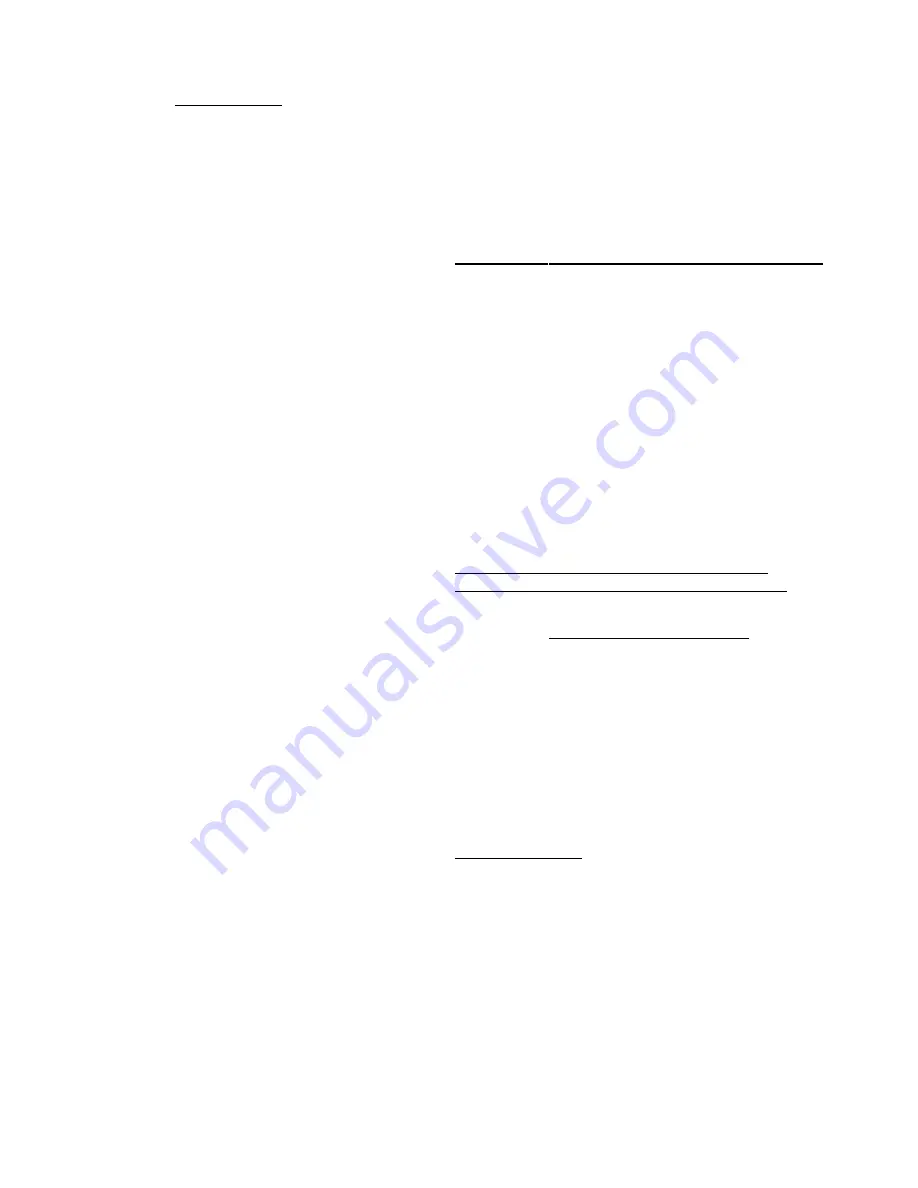
KEEP AWAY FROM FIRE AND HEAT. Keep your
equipment away from excessive heat which tends
to soften packings and cause leakage. Heat also
weakens the structure of hose and packings. For
best performance, DO NOT expose equipment
to temperatures above 160˚ F.
SAFETY
A. WORKING PRESSURE
The pump's maximum working pressure is 10,000
PSI (700 kg/cm 2). Make sure that all hydraulic
equipment such as rams, hoses, etc. used with this
pump are rated at 10,000 PSI operating pressure.
B. HYDRAULIC CONNECTIONS
Never disconnect or connect any hydraulic hoses
or fittings without first unloading the ram, then shift,
or open all hydraulic controls several times to
assure that the system has been depressurized. If
the system includes a gauge, double check the
gauge to assure pressure has been released.
When making connections with quick-disconnect
couplings, make sure the couplings are fully
engaged. Threaded connections such as fittings,
gauges, etc. must be securely tightened and leak
free.
DO NOT overtighten connections. Connections
need only be secure and leak free. Overtightening
can cause premature thread failure.
CAUTION: Loose or cross threaded fittings can be
potentially dangerous if pressurized. Never hold or
stand directly in line with any hydraulic connections
while pressurizing. Never grab, touch or in any
way come in contact with a hydraulic pressure leak.
Escaping oil can penetrate the skin and a serious
injury can result.
C. JACKING SAFELY
You should know the weight of what you intend to
lift and choose a ram with at least 10% more
capacity. The ram must be placed on a solid
foundation so that the base of the ram is fully sup-
ported. The load must be centered on the ram, or
equally distributed on multiple rams. Off-center
loading can result in the ram slipping out and loss
of the load. Never crawl or place any part of your
body under any load at any time. Insert blocking or
cribbing under the load as you lift. Hydraulic rams
are meant for lifting only and should not be used to
support the load for any period of time. You should
obtain and be familiar with the American National
Standards Institute rules that apply to hydraulic
rams and jacks (ANSI B30.1).
D. HOSES
DO NOT DROP HEAVY OBJECTS ON HOSE. A
sharp impact may kink wire strands on which the
strength of the hose depends.
AVOID SHARP KINKS IN HOSE. Never apply
pressure when hose is swung in sharp curves or
when the hose is visibly kinked.
OPERATING INSTRUCTIONS
A. Keep the control valve handle in neutral position.
Operate pump handle several times to remove air
from the system and to prime the pump. Pushing
directional control valve lever to the right directs
pump output to right-hand port. Pushing lever to
the left directs pump output to the left-hand port.
Center position is neutral/hold. Pump output is
directed back to tank.
B. You may operate a single-acting cylinder with this
style pump by merely connecting one hose to the
single-acting cylinder. Move the valve lever to the
side that is connected to the cylinder in order to
advance, move the lever to the center in order to
hold, and to the opposite of the advance position in
order to retract.
C. Be sure the pump reservoir is full of hydraulic oil.
NEVER FILL THE RESERVOIR UNLESS THE
CONNECTED RAMS ARE FULLY RETRACTED.
MAINTENANCE
Completely change oil at least twice a year. The following
conditions require more frequent oil changes:
a.
Rigorous duty, where oil may leak out or become
contaminated.
b. High humidity environment and extreme changes in
temperature that can result in condensation inside
the reservoir.
c.
Dirty or dusty environments that may contaminate
the oil.
Flushing the pump. If you suspect your pump has been
contaminated or discover sludge or other deposits on
internal components, you should thoroughly flush the
pump.
a.
Remove the old oil from the reservoir, then thor-
oughly clean the reservoir and refill with a clean,
nonflammable flushing oil.
b. Reassemble the pump head to the reservoir
and pump the pump handle approximately 50 times
with the valve in neutral.
c.
Empty the reservoir and refill with clean Simplex oil.