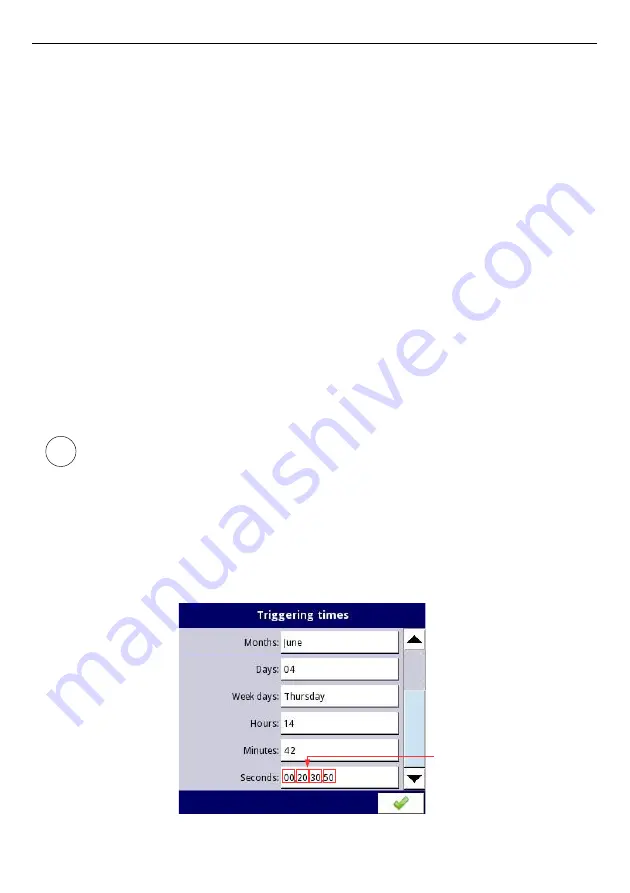
User Manual For - CONTROLLER/DATA RECORDER MultiCon CMC-N16
–
Idle value
– the value which occurs at the idle state, which means before and after
generating the Profile/timer,
–
Section list
– the submenu in which the user can define up to 100 sections
generated by the Profile/timer. For more information see
Chapter 7.12.1.
Profile/timer - General settings
–
Looping
– each Profile/timer has an ability to repeat its generated signal, this
parameter has the following options:
•
disabled
– the profile is not repeated,
•
counted
– allows to generate the profile a specified number of times defined in
the
Loop count
parameter,
•
from logical channel
– allows to run the profile a number of times that equals
the value in the selected logical channel determined by the
Looping source
parameter,
•
infinite
– allows to repeat the generated
Profile
infinitely,
–
Loop count
– this parameter is visible only if the
Looping
parameter is set as
counted
, defines the number of repetitions of the generated Profile,
–
Looping source
– this parameter is visible only if the
Looping
parameter is set as
from logical channel
. It allows to choose a logical channel from the list, whose
value will be compared with the number of already made cycles of the Profile,
–
Return to position
– this parameter is invisible if the
Looping
parameter is set as
disabled
, allows to select a fixed position from which every next generated Profile
has to start,
The parameters in the
Triggering times
submenu allow to define the moment of
generating the Profile with an accuracy of seconds. In every parameter the user can
select any number of options. If none of the options is selected in any parameter,
after accepting, the “
Press to select
” description appears next to the parameter.
Additionally, in that case, the Profile will not be generated.
we can see examples of Profile/timer: triggering times
configuration and output waveform. Operation of the Profile in
'on time'
mode is similar to
edge (once)
mode - see
Chapter 7.12.2. Profiles/timers - Triggering mode: level (gate),
because after the rising edge of the triggering source the
Profile
will be generated in whole, regardless of further changes of the signal source at the time of
generating the Profile.
Fig. 7.107. Samples of time settings for
Profile/timer
182
Respectively:
0 sec, 20 sec,
30 sec, 50 sec
i