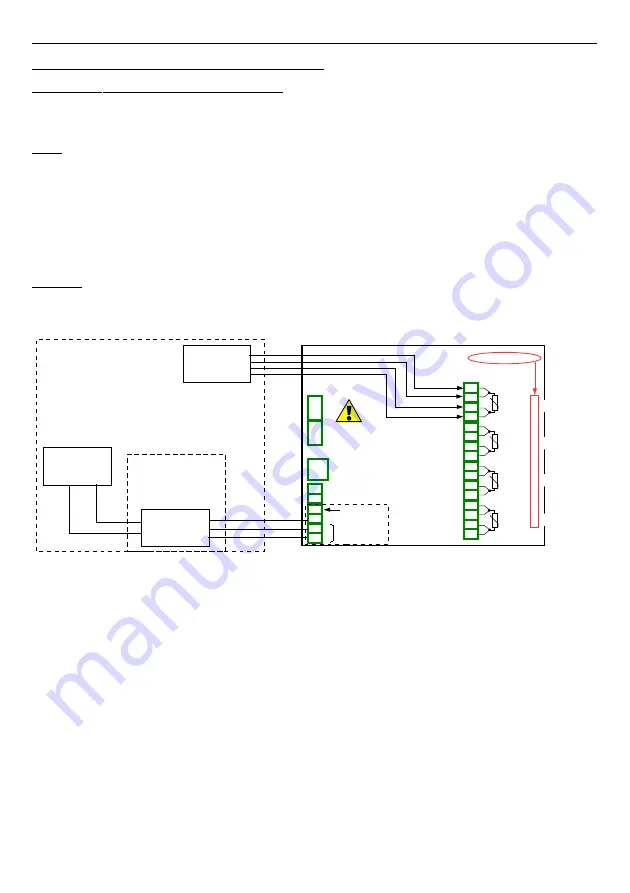
User Manual For - CONTROLLER/DATA RECORDER MultiCon CMC-99/141
7.13.2.
Examples of Controller configuration
s
7.13.2.1.
A
pplication of the Controllers
See also:
Chapter 7.13. CONTROLLERS
Task:
The task is to configure the controller which will control (via RS-485) the heater in order
to obtain a constant object temperature. Logical channels with a set point value and
temperature from the PT100 sensor are connected to the controller. After pre-analysis of
the sensor type and the transmittance of the object, we set the controller coefficients to the
following values: P=0.3, I=0.5, D=0.02. We do not want the controller to respond to a
deviation lower than 2ºC. On controller's output set 0-20mA range because that is the range
of the converter we use to control the heater in this task.
Solution:
First configure the controller, then connect the Pt100 sensor and Current converter to
the device. An example of this connections in presented in
Fig. 7.130. The connection scheme for RT4 module and Modbus MB1 port
In the first step we define
Controller
settings:
–
touch the screen and press
Menu
button,
–
press the
Device configuration
button,
–
enter the
Controllers
menu,
–
using the arrows in the top navigation bar, select any
Controller
such as
1
,
–
in the
Controller name
parameter write
Controller 1
,
–
Mode
parameter set as
PID
,
–
in the
Dead zone
parameter write
2
,
–
for
Controller parameters
parameter block:
•
in
P coefficient
parameter write
0.3
,
•
in
I coefficient
parameter write
0.5
,
•
in
D coefficient
parameter write
0.02
,
•
Differentiated signal
parameter set as
error (deviation)
,
214
Power supply
(depending on version)
1
2
8
5
6
7
3
4
+24V DC ±5%
(
I
max. = 200mA)
digital input
0/15..24V DC
RS-485
GND
GND
A+
B-
isolated
Pt100
sensor
Slot B
RT4
4 RTD inputs
Current
converter
Slave device
Slave address: 1
Register: 1h
Heater
Control system
0÷5A
RS-485
I
N
1
I
N
2
I
N
3
I
N
4
n01
n02
n03
n04
n05
n06
n07
n08
n09
n10
n12
n13
n14
n15
n16
n11
GND
Inp.B1 : RTD
Inp.B2 : RTD
Inp.B3 : RTD
Inp.B4 : RTD
SERVICE