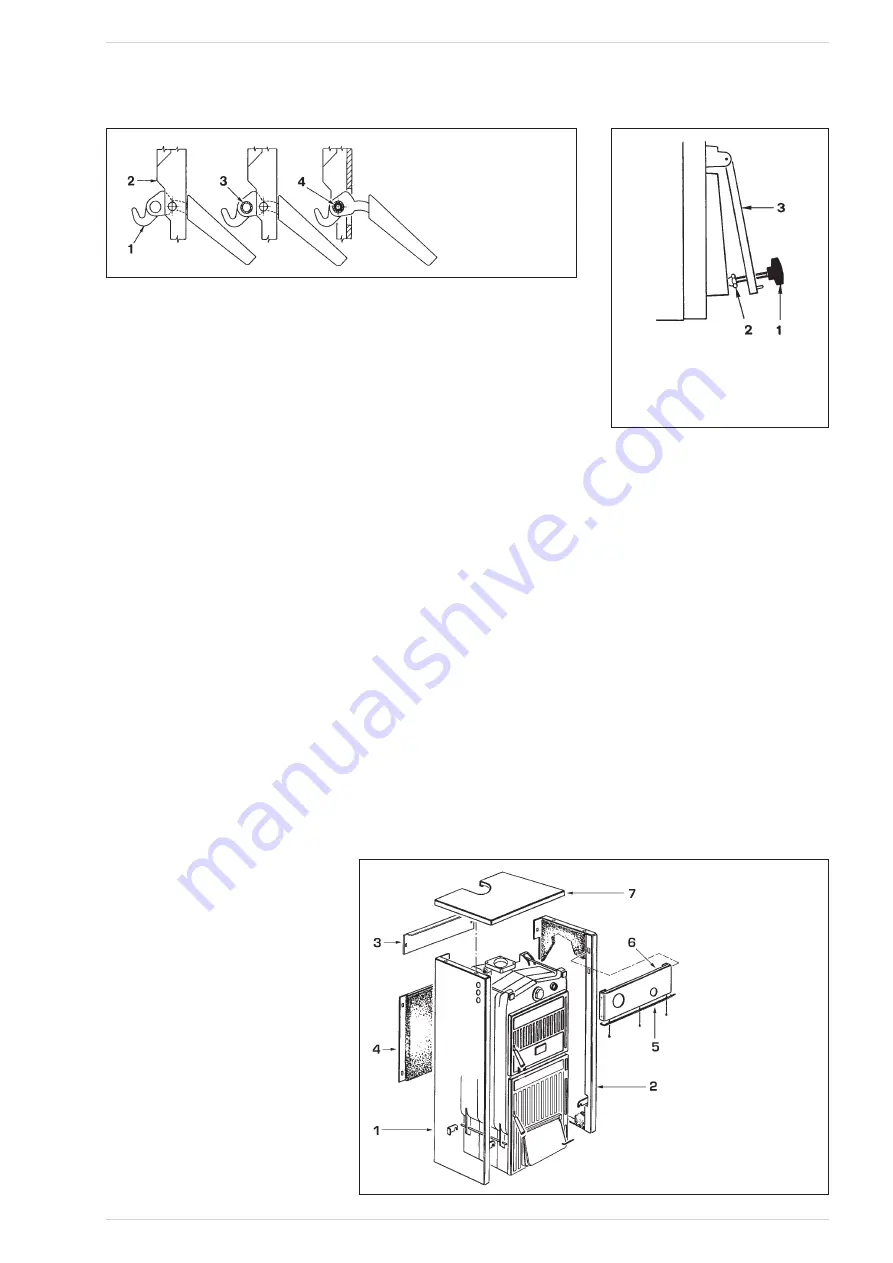
6
not be less than 0.5 bar.
Features of the feed water
The system water must be treated in accord-
ance with BS7593.
The inhibitor concentration must be checked
frequently particularly in the following cir-
cumstances.
– Large systems ( high water contents)
– Frequent replenishments due to system
leakages.
– If the system is drained.
BRAZIER GRID ASSEMBLY
1.2.4
(OPTIONAL)
In order to carry out the assembly proceed in
the following way (fig. 3):
– Carefully break out the cast as shown in
A (fig. 3). Then using a bit of 10 mm as
indicated in the detail (B).
– Place the back grid (12) in the combustion
chamber.
– Place the front grid (10) and block it to the
hub (9) with the screws (8) and the nuts
(7); block the front grid from the right side
of the boiler body with the screws (5).
– Hook the tie rod (6) to the seats extracted
from the front and rear grid.
– Place the intermediate grids (11).
– Introduce the ring (4) and the lever (3) on
the hub (9), fixing then everything with the
washer (2) and the screw (1).
ASSEMBLY OF THE
1.2.5
ACCESSORIES
The closing handles for the ports and the
screw with the adjustment knob for the blast
gate damper are supplied separately, to avoid
damaged during the transport.
Both the handles and the screws with knob
are packed in a nylon bag, placed inside the
ash collection basin.
For the assembly of the handles proceed as
following (fig. 4):
– Take a handle (1), insert it in the opening
of the load port (2) and insert the roller (3)
in the opening of the handle; secure the
handle with split pin (4).
– Carry out the same operation for the han-
dle of the ash box port.
To assemble the screw with the knob, pro-
ceed as follows (fig. 5):
– Remove the screw M8 x 60, which fixes
the air blast damper to the ash box port
and screw the screw with the bakelite
knob (1) on, which is supplied in the pack-
aging.
Place the blind nut with cap (2) at the end
of screw M 10.
– Fix lever M6 to the air blast damper (3)
placing it in a horizontal direction on the
right. The lever has an opening at its end,
where the chainlet of the thermostatic reg-
ulator will be connected.
CASING ASSEMBLY
1.2.6
Assemble the casing as shown in figure 6.
The side panes are secured with brackets
to the tie rods that hold the cast sections
together:
– Loosen the second or third nut of each tie
rod.
– Hook the left side (1) on the lower tie rod
and superior of the boiler and adjust the
positposition the nut and locknut to cor-
rectly locate the side panel.
– Fit the RHS (2) panel in the same way as
LHS (1).
– Hook the front upper board (3) on to the
two splines in the opening, on each side.
– Carry out the same operation to fix the
back lower board (4).
– The protection deflector (5) is fixed to the
control board (6) with three self-threading
screws.
Fix the board by means of the press fit-
tings.
Then uncoil the capillary of the thermom-
eter and place it in the left pocket in the
rear section of the heat exchanger and
secure with the clip.
The right pocket is used for a temperature
gauge.
– Fix the cover (7).
NOTE: Remove the test certificates and
boiler documentation from the combus-
tion chamber and keep safe.
DRAUGHT REGULATOR
1.2.7
The boilers
SOLIDA
can be supplied with 2
types of thermostatic regulators.
NOTE: In order to fix the lever with the
chainlet in the regulator holder it is nec-
essary to remove the deflector, which is
assembled on the control board, by unscrew-
ing the three screws that fix it (fig. 6).
Replace the protection deflector after the
assembling and related adjustment.
LEGEND
1 Handle
2 Load port
3 Roll
4 Elastic split pin
Fig. 4
LEGEND
1 Screw with knob M10 x 70
2 Blind nut with cap
3 Blast gate damper
C<><E;Û
~ÛÛ C]^lÛka\]Û
ÛÛ Ia_`lÛka\]Û
ÛÛ Ggkl]jagjÛkmh]jagjÛZgYj\Û
ÛÛ Ggkl]jagjÛaf^]jagjÛZgYj\Û
ÛÛ Gjgl][lagfÛ\]^d][lgjÛ
ÛÛ :gfljgdÛZgYj\Û
ÛÛ :gn]j
Fig. 5
Fig. 6
Summary of Contents for SOLIDA 5
Page 1: ...IEB 7 IEB 7 IEB 7 FB IEB 7 FB KA...
Page 2: ...9D8JB CI G A 6H KZg 9ZhXg ei dc Lg iZg 9ViZ...
Page 37: ...37 DEJ I...
Page 38: ...38 DEJ I...
Page 39: ......