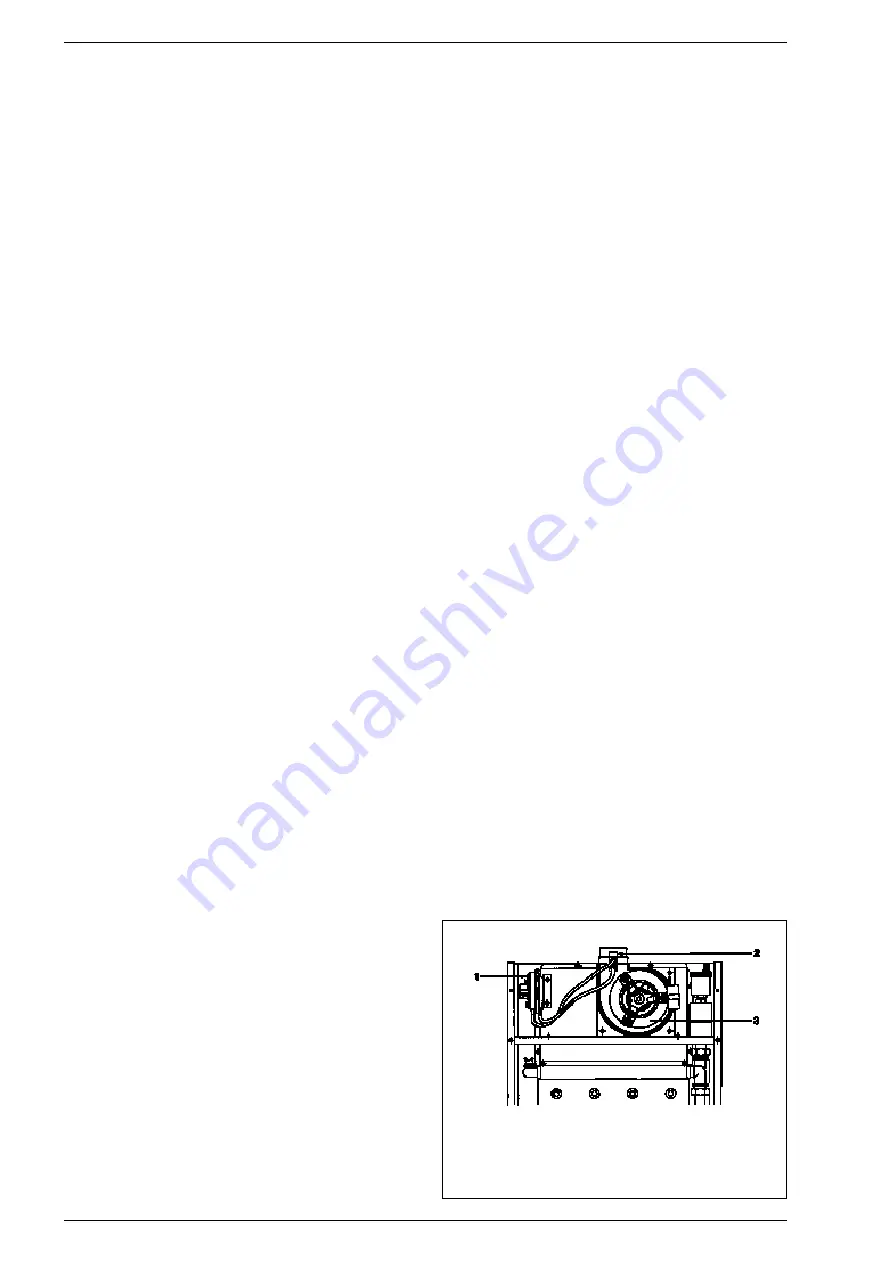
21
2.15.1 Operating cycle
Before igniting the boiler, use a voltmeter to make sure
that the electrical connection to the terminal block has
been made properly, respecting the position of line and
neutral, as shown in the diagram. Press the switch on the
control panel and check for the presence of voltage sup-
ply (warning lamp lights up). The boiler is now ready to
start working upon demand for heating or drawing off of
D.H.W.; a discharge current is sent to the ignition elec-
trode through the FM11 programmer, and the gas valve
opens at the same time. Burner ignition normally takes
place within 2 or 3 seconds.
However, it is possible for ignition failures to occur, with
consequent activation of signal indicating that the equip-
ment has “locked out”.
–
Gas failure
This may occur upon first ignition or after long periods
of boiler lay-off when there is air in the pipes. It may be
caused by the gas cock being closed or by one of the
valve coils having a break in the winding, so that the
valve cannot open.
The appliance runs through the cycle normally sen-
ding electric power to the ignition electrode. The elec-
trode continues spark discharge for a maximum of 10
sec. If the burner does not ignite, the equipment
“locks out”.
–
Ignition electrode fails to spark
This may be due to there being a break in the wire to
the electrode or to the wire not properly fastened to
the equipment electric terminal; or else, the transfor-
mer has burnt out.
In the boiler, only the gas to the burner is seen to
open. After 10 sec. the equipment “locks out”.
–
No detection of flame
This occurs when the position of phase and neutral
has not been respected on the terminal block.
There is a break in the wire to the sensing electrode or
the electrode itself is touching earth: the electrode is
worn out and needs replacing.
The continuous spark discharge of the electrode is
noted starting from ignition even though the burner is
lit. After 10 seconds have elapsed, the sparks cease,
the burner goes out, and the warning light indicating
equipment “lock-out” lights up.
When there is a sudden voltage failure, the burner shuts
out immediately; when power supply returns, the boiler
will start up again automatically.
2.16
INTERRUPTION OF THERMOCOUPLE
“MURELLE 20 CE - 20 BF CE”
The boiler is equipped with total safety devices, with
extinguishing of main burner and pilot if an accidental
overtemperature heppens in the water-gas exchanger.
Control comes about via a limit thermostat (6, Fig. 3 - 7,
Fig. 3/a) set at 85°C and a safety thermostat (11, Fig. 3 -
12, Fig. 3/a) set at 100°C, arranged in series in the circuit
of the interrupted thermocouple and overheat cut-off
device of the gas valve.
To enable re-ignition of the pilot burner (12, Fig. 3 - 5, Fig.
3/a), so restoring boiler operation, it will be necessary to
wait until the temperature in the exchanger drops below
the thermostat setting value.
2.17
SMOKE SAFETY DEVICE “MURELLE
20 R CE IONO - 20 CE - 20/25 CE IONO”
This is a safety device against possible smoke emission
into the ambience.
The safety device goes into action by blocking operation
of the gas valve when the return of smoke into the
ambience is continuous and in quantities that might con-
stitute a danger. To enable restart of the boiler, it is neces-
sary first to unscrew the cover of the thermostat and reset
the push-button (2, Fig. 18).
Before carrying out this operation, make sure that electric
power is not reaching the control panel.
Should the boiler continue to “lock out” , it will be neces-
sary to make a careful check on the flue pipe, making all
the necessary modifications and adaptations so that it
can function efficiently.
2.18
SMOKE PRESSURE SWITCH
“MURELLE 20 TX CE IONO - MURELLE BF”
Impurities and possible formations of condensate, which
are more likely in cold periods of the year, could cause
the pressure switch not to function and the boiler to fail to
start. The pressure switch is set in the factory at the opti-
mal values of 4.5 - 6 mm H
2
O for the
“20 TX - 20 BF”
ver-
sions, and 8 - 9 mm H
2
O for the
“25 BF”
version. This is
able to guarantee operation of the boiler even with air
intake and flue outlet pipes at the maximum limit of length
allowed.
In the case of replacement, the type of pressure switch
originally mounted must be used without fail. Under no
circumstances must the pressure switch for the
“20 BF”
version be installed on the
“25 BF”
version, since
otherwise the safety of operation of the appliance would
be jeopardized.
KEY
1 Smoke pressure switch
2 Venturi (
“20 TX CE IONO - 25 BF CE IONO”
versions)
3 Fan
Fig. 26