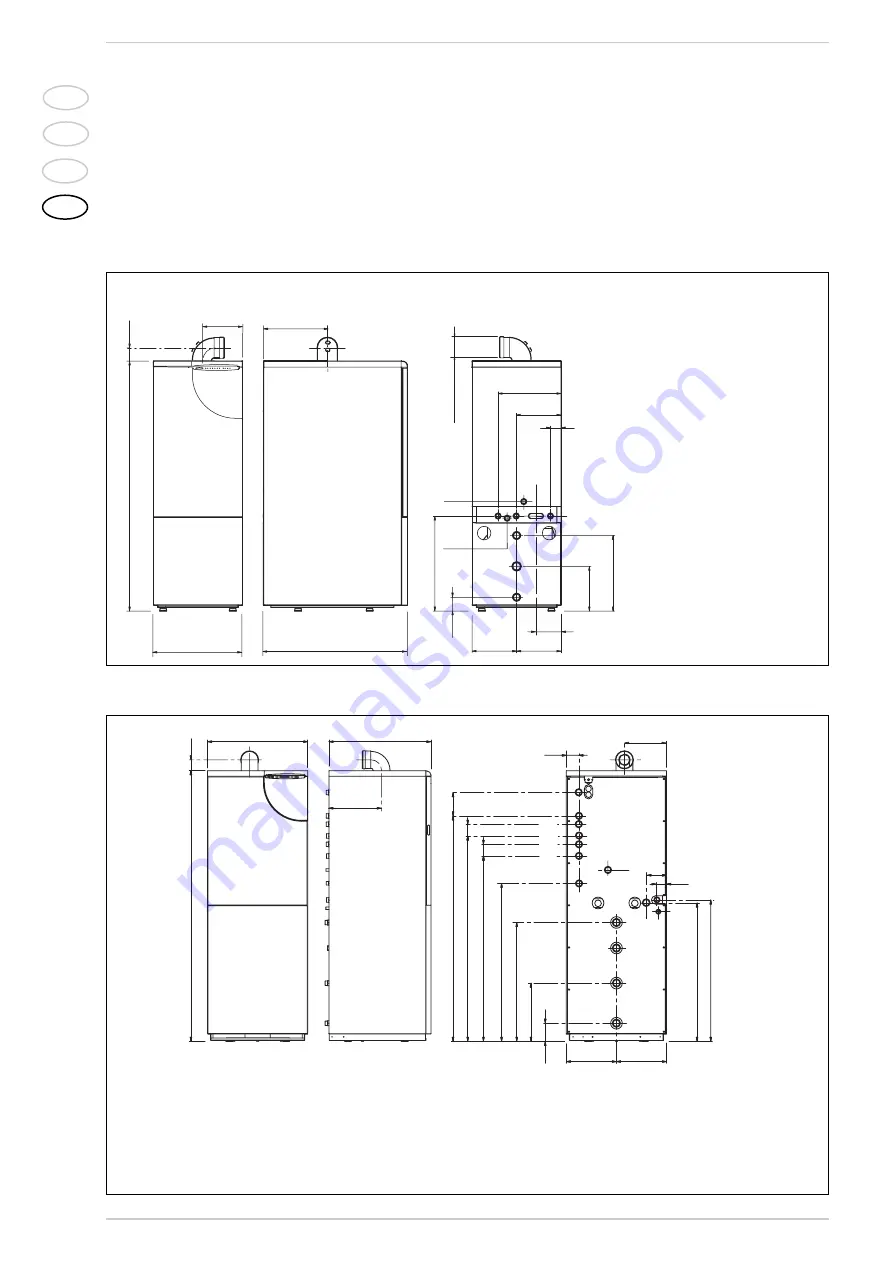
IT
ES
PT
GB
94
1.1
INTRODUCTION
“DEWY”
boilers are premix condensation
thermal appliances which use microproces-
sor technology for function control and
management. They comply with the euro-
pean
directives
90/396/CEE,
89/336/CEE, 73/23/CEE, 92/42/CEE
and with the european specifications EN
483 - EN 625.
These appliances can be fired by natural
gas (methane) and propane gas (G31).
The instructions given in this manual are
provided to ensure proper installation and
perfect operation of the appliance.
1
DESCRIPTION OF THE BOILER
1.2
DIMENSIONS
1.2.1
“30/80” model
330
G
240
310
M
R
55
S2
C
U
S1
E
70
490
390
130
S3
230
230
745
Ø 60/1
00
230
65
1
290
460
215
Fig. 1
CONNECTIONS
R
C.H. return
3/4” (UNI-ISO 228/1)
M C.H. flow
3/4” (UNI-ISO 228/1)
G
Gas connection 3/4” (UNI-ISO 228/1)
E
D.H.W. inlet
3/4” (UNI-ISO 228/1)
U
D.H.W. outlet
3/4” (UNI-ISO 228/1)
C
Recirculation
3/4” (UNI-ISO 228/1)
S1 C.H. safety relief valve
S2 Tank unit safety relief valve
S3 Condensation outlet ø 25
600
65
1
620
610
315
252
76
M2
R2
M1
R1
M
R
S1
C1
S3
G
S2
117
62
U
C
E
10
9
34
9
71
2
94
6
70
11
0
9
1
229
70
1
3
49
1
4
0
300
300
828
84
6
1.2.2
“30/130” model
CONNECTIONS
R
Zone 1 system return
3/4” (UNI-ISO 228/1)
R1
Zone 2 system return (optional)
3/4” (UNI-ISO 228/1)
R2
Zone 3 system return / Low
temperature return (optional)
3/4” (UNI-ISO 228/1)
M2
Zone 3 system delivery / Low
temperature delivery (optional)
3/4” (UNI-ISO 228/1)
M1
Zone 2 system delivery (optional)
3/4” (UNI-ISO 228/1)
M
Zone 1 system delivery
3/4” (UNI-ISO 228/1)
G
Gas connection
3/4” (UNI-ISO 228/1)
E
D.H.W. inlet
3/4” (UNI-ISO 228/1)
U
D.H.W. outlet
3/4” (UNI-ISO 228/1)
C
Recirculation
3/4” (UNI-ISO 228/1)
C1
Recirculation pump kit (optional)
1/2” (UNI-ISO 228/1)
S1/S2 C.H. safety relief valve/tank
S3
Condensation outlet ø 25
Fig. 1/a
Summary of Contents for DEWY 30/130
Page 33: ......