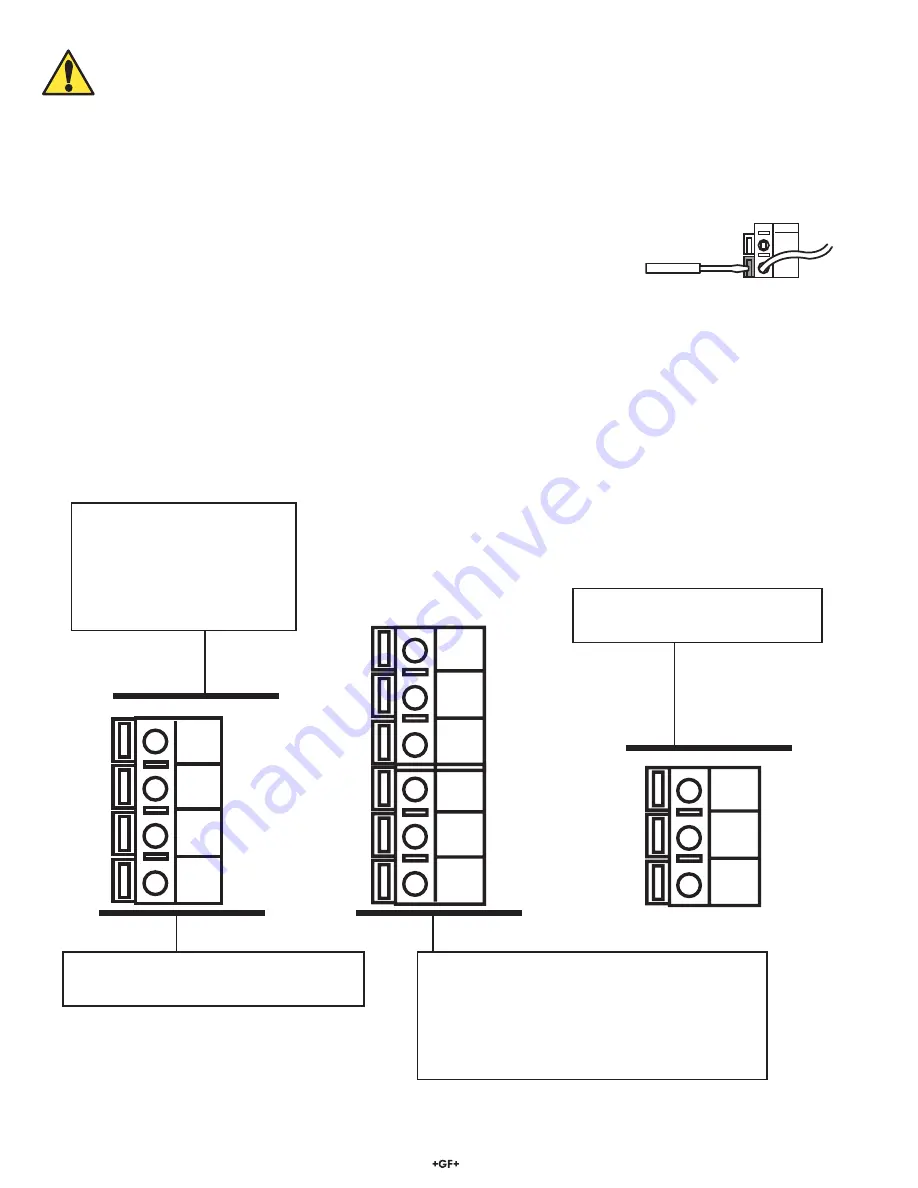
2
Signet 8450-2 Pressure Transmitter
3. Electrical
Connections
Caution:
Failure to fully open terminal jaws before removing wire may permanently damage instrument.
Wiring Procedure
1. Remove 0.5 - 0.625 in. (13-16 mm) of insulation from wire end.
2. Press the orange terminal lever downward with a small screwdriver to open terminal jaws.
3. Insert exposed (non-insulated) wire end in terminal hole until it bottoms out.
The terminals will accomodate conductors from 14 to 22 AWG.
4. Release orange terminal lever to secure wire in place. Gently pull on each wire to ensure a good connection.
Wiring Removal Procedure
1. Press the orange terminal lever downward with a small screwdriver to open terminal jaws.
2. When fully open, remove wire from terminal.
Wiring Tips:
• Do not route sensor cable in conduit containing AC power wiring. Electrical noise may interfere with sensor signal.
• Routing sensor cable in grounded metal conduit will help prevent electrical noise and mechanical damage.
• Seal cable entry points to prevent moisture damage.
• Only one wire should be inserted into a terminal. Splice double wires outside the terminal.
• The cable length from the sensor to the transmitter must not exceed 400 ft. (122 m)
• For best performance, ground the sensor SHIELD wire to a local earth ground at a point near the sensor.
(Experiment with connecting the sensor shield wire to different local ground points to identify best signal quality.)
2
1
4
3
2
1
13
12
11
10
9
8
7
6
5
System Pwr
Loop -
System Pwr
Loop +
AUX
Power -
AUX
Power +
Sensr Gnd
(WHITE)
Sensr IN
(RED)
Sensr V+
(BLACK)
Relay 2
(NO)
Relay 2
(COM)
Relay 2
(NC)
Relay 1
(NO)
Relay 1
(COM)
Relay 1
(NC)
Terminals 5-10: Relay Outputs
Two sets mechanical SPDT contacts, programmable
(see CALIBRATE menu) as:
• High or Low setpoint with adjustable hysteresis
• Proportional pulse output
• May be disabled (Off) if not used.
Terminals 3 and 4: Loop Power
12-24 VDC ±10% system power
and current loop output.
• Maximum loop impedance:
50
Ω
max. at 12 V
325
Ω
max. at 18 V
600
Ω
max. at 24V
Terminals 11-13: Digital sensor input
See next page for more information.
Terminals 1 and 2: AUXILIARY power
Provides power for relay operation.