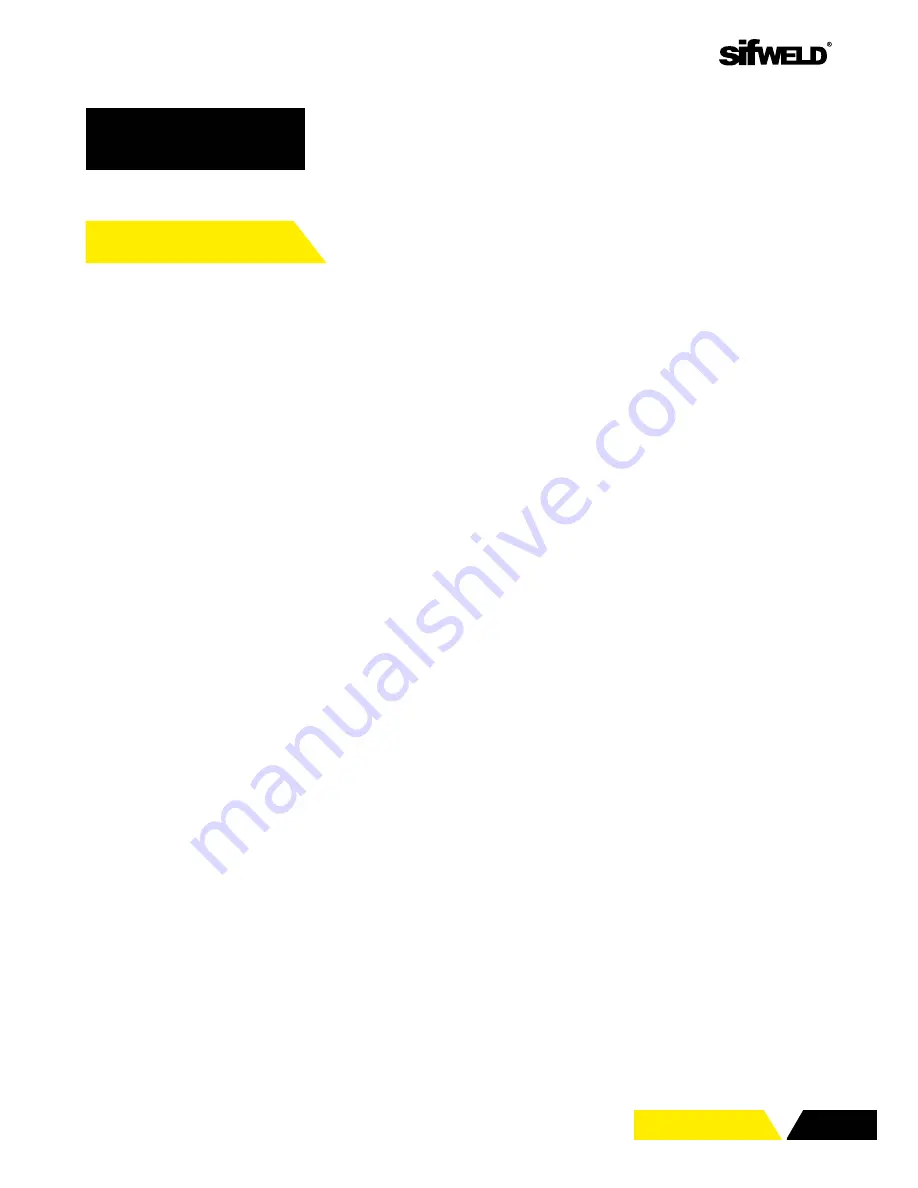
7
1. Preface
Congratulations on choosing your SifWeld TS200ACDC Inverter.
Used correctly, SifWeld products can significantly increase the productivity of your welding, and provide
years of economical service. This operating manual contains important information on the use,
maintenance and safety of your SifWeld product. Please read the manual carefully before using the
equipment for the first time. For your own safety and that of your working environment, pay particular
attention to the safety instructions in the manual.
For more information on SifWeld products, consult an authorised SifWeld dealer, or visit the SifWeld web
site at www.sifweld.com. The specifications presented in this manual are subject to change without prior
notice.
Disclaimer
While every effort has been made to ensure that the information contained in this guide is accurate and
complete, no liability can be accepted for any errors or omissions. We reserve the right to change the
specification of the product described at any time without prior notice. Do not copy, record, reproduce
or transmit the contents of this guide without prior permission.
1.1 General