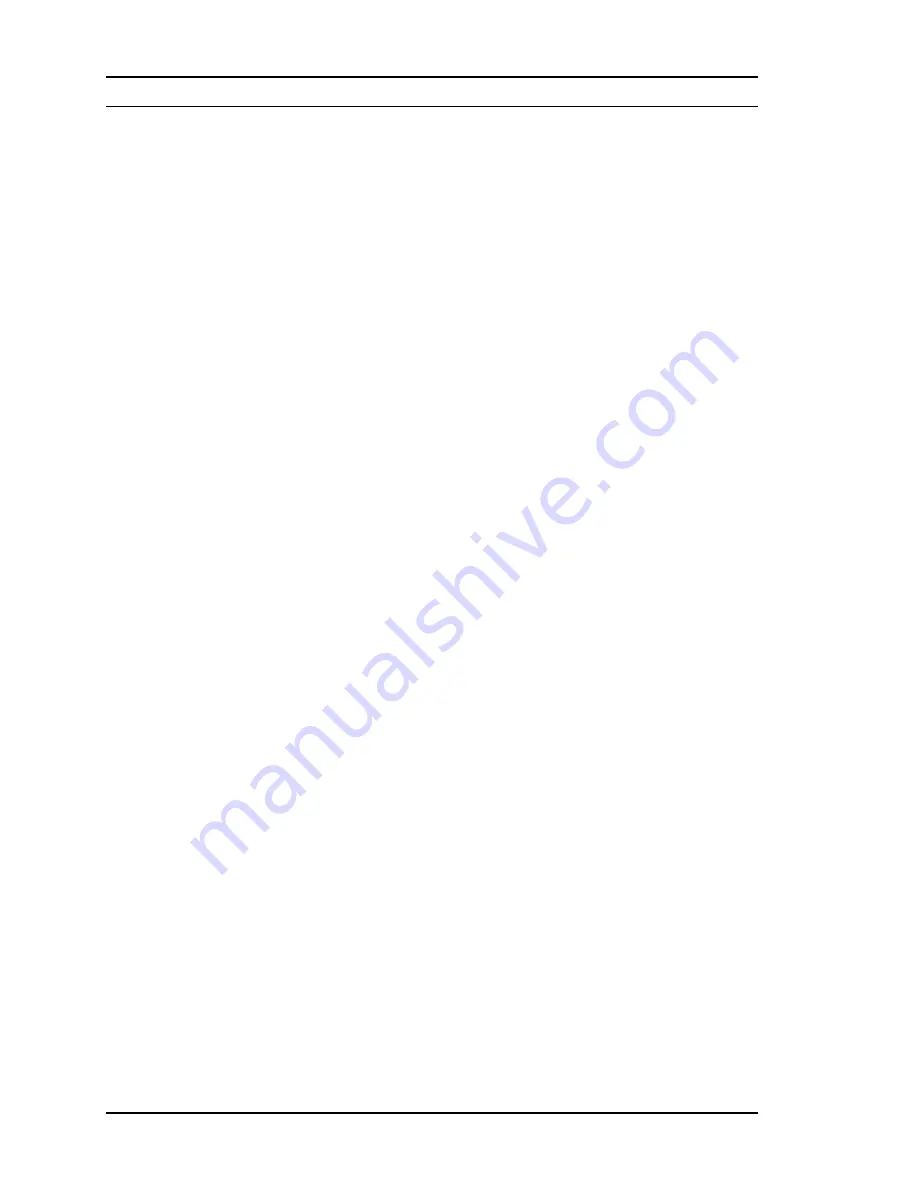
Chapter 4 Troubleshooting & Repair
Series 220/221 Instruction Manual
2. Mechanical installation may be incorrect. Verify the straight run is
adequate as described in Chapter 2. For in-line meters, make sure
the meter is not installed backwards and there are no gaskets protrud-
ing into the flow stream. For insertion meters, verify the insertion
depth and flow direction.
3. The meter may be reacting to actual changes in the flow stream. The
output can be smoothed using a time constant. The displayed values
can be smoothed using the time constant in the Display Menu. The
analog outputs can be smoothed using the time constant in the Out-
put Menu. A time constant of 1 will result in the change in value
reaching 63% of its final value in one second. A time constant of 4
is 22%, 10 is 9.5% and 50 is 1.9% of the final value in one second.
The time constant equation is shown below (TC = Time Constant).
= 100
(
1 – e
(-1/TC)
)
% change to final value
in one second
4. The vortex coefficient Ck may be incorrectly set. The Ck is a value
in the equation used to determine if a frequency represents a valid
vortex signal given the fluid density and signal amplitude. In prac-
tice, the Ck value controls the adaptive filter, fi, setting. During
flow, view the f and fi values in the first column of the hidden diag-
nostics. The fi value should be approximately 10-20 % higher than
the f value. If you raise the Ck setting in the Calibration Menu, then
the fi value will increase. The fi is a low pass filter, so by increasing
it or lowering it, you can alter the range of frequencies that the meter
will accept. If the vortex signal is strong, the fi value will increase to
a large number – this is correct. Note: at high frequencies, the dis-
play may not be able to display all the digits of the fi value (for ex-
ample, 114 may be displayed and the actual value is 1140).
Symptom: No Output
1. For remote mounted electronics, carefully check all the wiring con-
nections in the remote mount junction box. There are 6 connections
that must be correct, verify each color (black and red), shield, and
wire number.
2. Check the density value in the Calibration Menu to see if it is correct
for the current operating conditions.
3. Using ESD precautions and hazardous area precautions, remove the
electronics enclosure window cover. Disconnect the vortex sensor
from the analog board (the analog board is the first board below the
microprocessor (display) board. Measure the resistance from each
outside pin to the meter ground - each should be open. Measure the
resistance from the center pin to the meter ground – this should be
grounded to the meter. With the sensor still disconnected, go the
first column of the hidden diagnostics and display the vortex shed-
ding frequency, f. Hold a finger on the three exposed pins on the
4-4
IM-22-C