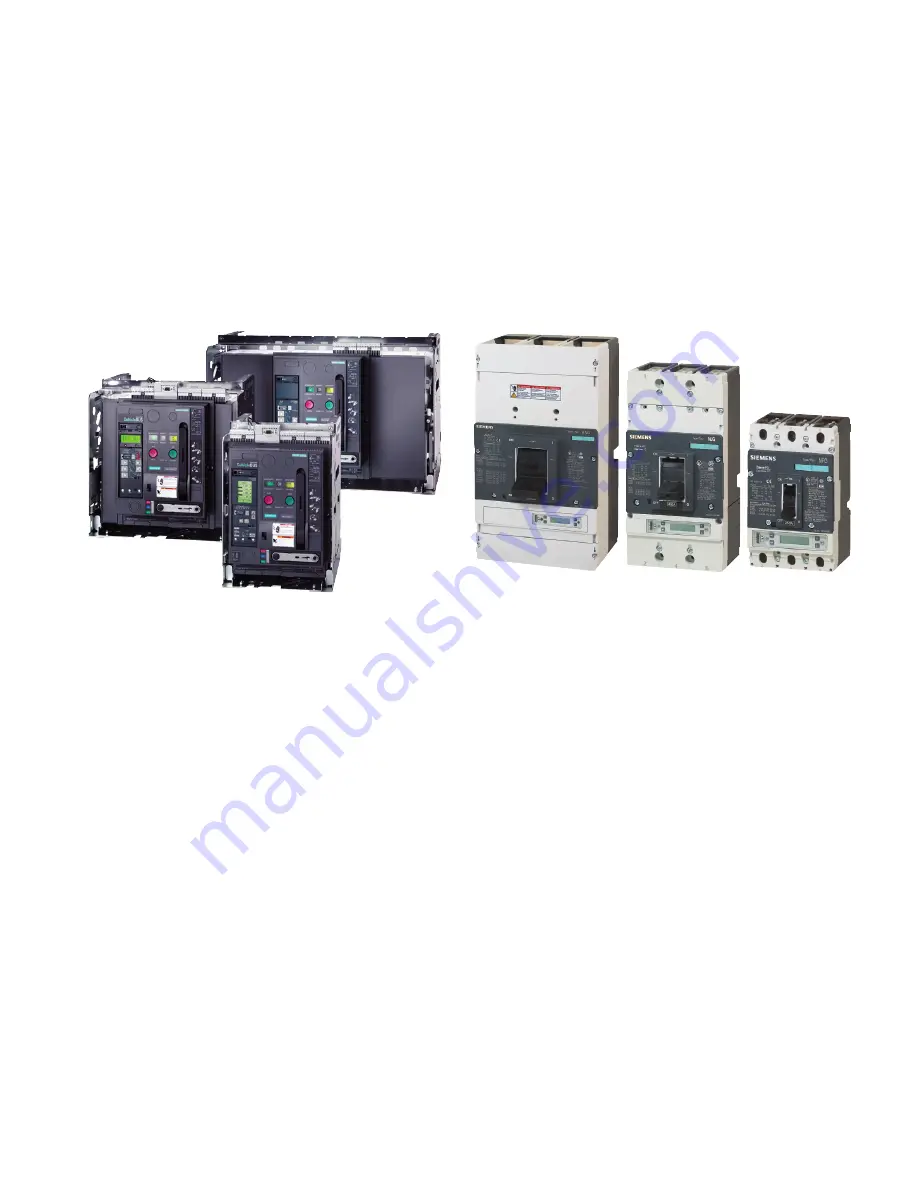
Chapter 2
Sm@rt DAS System
Breaker Requirements
The Sm@rt DAS system requires certain features in both the
WL and VL breakers. This section highlights the requirements
for breakers as well as the features for each breaker with
Sm@rt DAS.
WL
Features
ETU 776 required
COM16
Normal settings
Parameter A on breaker
Default settings are minimum
Adjust on breaker to change
DAS (maintenance mode) settings
Parameter B on breaker
Default settings are minimum
Adjust on breaker to change
VL
Features
ETU 586
COM21
Normal settings
Parameters on breaker
Default settings are minimum
Adjust on breaker to change
DAS (maintenance mode) settings
Stored in controller
Default settings are minimum
Adjustable settings are:
- Short time delay (A)
- Short time delay (ms)
- Instantaneous (A)
To adjust settings, see Chapter 4
Figure 2.5:
WL Breakers
Figure 2.6:
VL Breakers
7