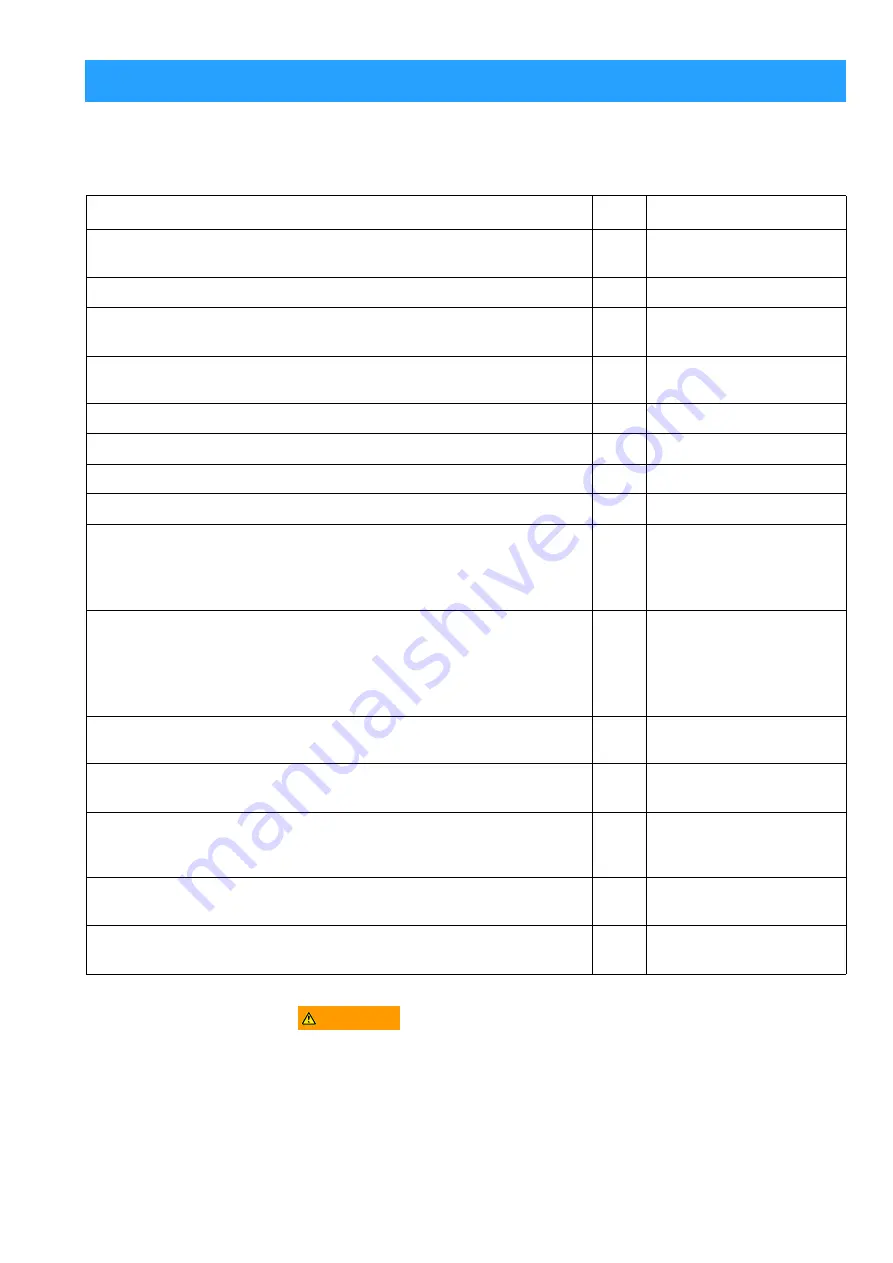
Operation
9229 0025 176 0E
69
2021-11-15
Operation
Commissioning
Before commissioning, check the following points to ensure that the vacuum circuit-
breaker is functioning faultlessly at operating temperature:
Faulty or damaged vacuum circuit-breaker
There is a risk of injury if the vacuum circuit-breaker is damaged or malfunctions!
• Immediately take the vacuum circuit-breaker out of operation.
• Do not put vacuum circuit-breaker back into operation.
• If the malfunctions or the damage cannot be remedied, contact a sales repre-
sentative or Siemens Service and, if necessary, send back the vacuum circuit-
breaker.
Checklist
Notes
Does the information on the name plate (see page 34) match the order
data?
Ensure the correct operating voltage.
Is the ambient air temperature at least -5 °C / 23 °F (with addition A40 to -
25 °C / -13 °F)?
If necessary, clean the vacuum circuit-breaker (details on this in section
“Cleaning” on page 73).
Check that bolted joints are tightened securely.
Check that the plug-in connection of the connector strip is seated firmly.
If necessary, check and adjust the customer’s devices.
If there is a closing lock: Is closing unlocked accordingly?
Test operation without supply voltage
Charge the closing spring with the hand crank (see Fig. 112), then press
the CLOSE pushbutton and, once closing has been performed, press the
OPEN pushbutton.
Test operation with supply voltage
To perform a test operation with the motor, switch on the supply voltage.
The motor starts up immediately and charges the closing spring. Check the
indicator for the charge state of the closing spring (mechanically and elec-
trically).
Electrically check auxiliary switch S1 and position switch in both end posi-
tions – operate the vacuum circuit-breaker to do so.
Check functioning of the closing solenoid Y9 and all existing shunt
releases by operating them electrically.
If there is a 3AX1103 undervoltage release (Y7): Has the retaining screw
of the striker pin been shifted from position A to B (see “Removing the
transport block from the undervoltage release”, on page 52)?
If there are interlocks and a retrofitted key-operated interlock: Check if the
function of the interlocks as per IEC 62271-200 is guaranteed.
After completion of the tests:
Has the cover been replaced and fastened?
WARNING