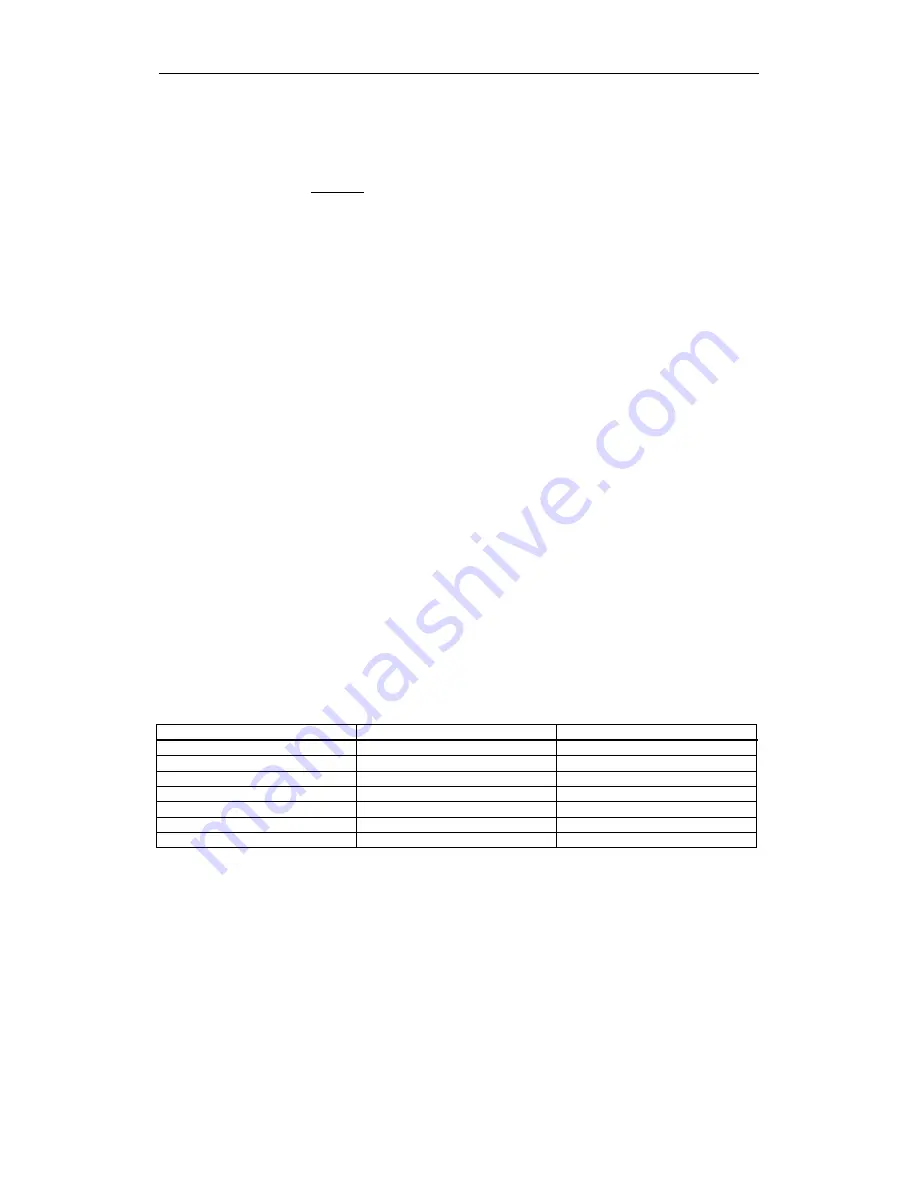
8 Application examples
11.03
8.3 Testing the function of the brake mechanical system
© Siemens AG 2003 All Rights Reserved
8-452
SINUMERIK 840D/SIMODRIVE 611 digital SINUMERIK Safety Integrated (FBSI) - Edition 11.03
This value must be entered with an additional safety margin in MD
$MA_SAFE_BRAKETEST_TORQUE. The magnitude of the margin is oriented
to the maximum holding force to be tested.
Example:
The weight of the vertical axis is 4000 N, the guaranteed braking force is 6000
N. On account of the weight of the axis, a torque of 32% of the holding torque
of the motor is obtained and displayed in MD 1728. Therefore 32% must be
parameterized in MD 1192. The correct value for $MA_BRAKETEST_TORQUE
is obtained as follows:
$MA_SAFE_BRAKETEST_TORQUE = 32% * 6000N / 4000N = 48%
In addition, the electronic weight equalization should be parameterized in the
axial NCK-MD 32460: $MA_TORQUE_OFFSET. This means that the
necessary holding torque is re-established much faster when the brake is
released (the brake is open).
The monitoring window for the maximum permissible movement in the brake
test is defined in the axial MD $MA_SAFE_BRAKETEST_POS_TOL. The PLC
actively monitors this position window – from the start of the brake test and not
only when it is detected that the fixed endstop has been reached. This is a
difference when compared to activating traversing to the fixed endstop from the
part program.
The contour deviation that is determined is always used in the brake test to
detect that the fixed endstop has been reached. The parameterization in
$MA_FIXED_STOP_BY_SENSOR is therefore irrelevant. The required
threshold value must be set in MD
$MA_FIXED_STOP_THRESHOLD
. This
means that the traversing distance from the PLC via FC 18 must be greater
than this threshold value. Furthermore, the drive must have reached its torque
limit parameterized via $MA_SAFE_BRAKETEST_TORQUE.
8.3.3 Sequence
The brake test in the PLC is carried out by calling data block FB11 (in the basic
program) from the user program. The brake test comprises the following steps:
Step Expected
checkback
Monitoring
time
value
Start brake test
DBX 71.0 = 1
TV_BTactiv
Close brake
Bclosed = 1
TV_Bclose
Output traversing command
DBX 64.6 Or DBX 64.7
TV_FeedCommand
Output traversing command test
DBX62.5 = 1
TV_FXSreached
Wait for the holding time
DBX62.5 = 1
TV_FXShold
De-select brake test/open brake
DBX71.0 = 0
TV_BTactiv
Output test O.K.
Declaration of the function
VAR_INPUT
Start: BOOL ; //Start of the brake test
Quit : BOOL ; //Acknowledge Error
Bclosed : BOOL ; //Brake closed input (single channel - PLC)
Axis : INT ; //Testing axis no.
TimerNo : TIMER ; //Timer from User
TV_BTactiv : S5TIME ; //TimeValue – brake test active
$MA_SAFE_BRAKE
TEST_POS_TOL
Function_Block FB 11