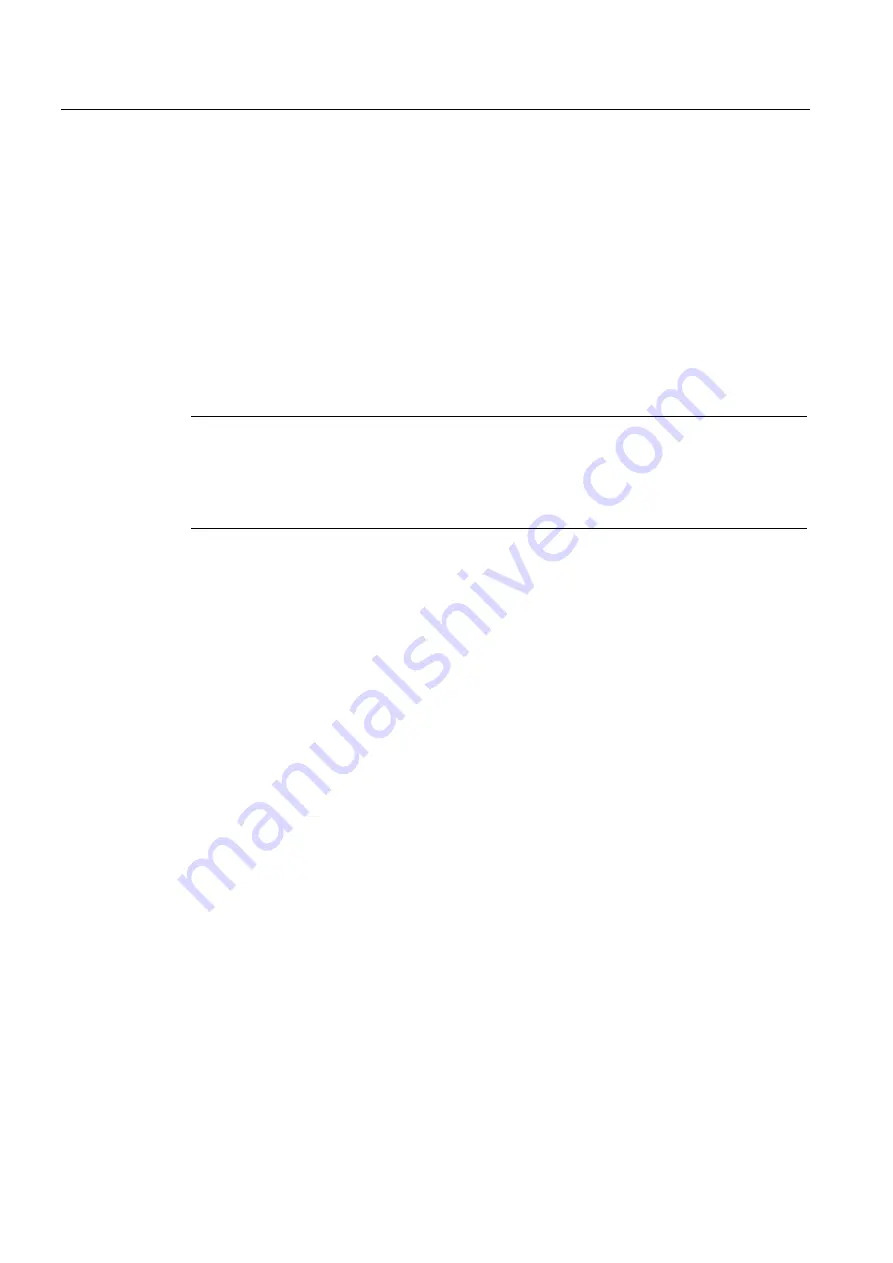
Detailed Description
2.5 Toolholder with orientation capability
Basic logic functions: Tool Offset (W1)
122
Function Manual, 11/2006, 6FC5397-0BP10-2BA0
Activation
A toolholder becomes active when both a toolholder and a tool have been activated. The
selection of the toolholder alone has no effect. The effect of selecting a toolholder depends
on the G code
TCOABS
/
TCOFR
(modal G-code group for toolholders).
Changing the G code in the
TCOABS
/
TCOFR
group causes recalculation of the tool length
components when the toolholder is active. With
TCOABS
, the values stored in the toolholder
data for both angles of rotation α1 and α2 are used to determine the tool orientation.
With
TCOFR
, the two angles are determined from the current frame. The values stored in the
toolholder data are not changed, however. These are also used to resolve the ambiguity that
can result when the angle of rotation is calculated from one frame. Here, the angle that
deviates least from the programmed angle is selected from the various possible angles.
Note
For more explanations on the programming of tool compensations with toolholder kinematic
and for the system variables see:
References:
/PGA/ Programming Manual Work Preparation
2.5.7
Supplementary conditions and control system response for orientation
Full orientation
For a given data set that describes a certain kinematic, all the conceivable special
orientations can only be displayed when the following conditions are satisfied:
•
The two vectors v
1
and v
2,
that describe the rotary axes, must be defined (i.e., must not be
equal to zero).
•
The two vectors v
1
and v
2
must be perpendicular to each other.
•
The tool orientation must be perpendicular to the second rotary axis.
Non-defined orientation
If these conditions are not satisfied and an orientation that cannot be achieved by an active
frame is requested with
TCOFR
, an alarm is output.
Vector/angle of rotation dependencies
If vector v
1
or v
2
, which describes the direction of a rotary axis, is set to zero, the associated
angle of rotation α1 or α2 must also be set to zero. Otherwise, an alarm is produced. The
alarm is not output until the toolholder is activated, i.e., when the toolholder is changed.
Summary of Contents for SINUMERIK 840D sl
Page 282: ...Index Basic logic functions Acceleration B2 64 Function Manual 11 2006 6FC5397 0BP10 2BA0 ...
Page 388: ...Basic logic functions Travel to fixed stop F1 Function Manual 11 2006 6FC5397 0BP10 2BA0 52 ...
Page 962: ...Index Basic logic functions Emergency Stop N2 20 Function Manual 11 2006 6FC5397 0BP10 2BA0 ...
Page 1704: ...Constraints Basic logic functions Spindles S1 94 Function Manual 11 2006 6FC5397 0BP10 2BA0 ...
Page 1716: ...Index Basic logic functions Spindles S1 106 Function Manual 11 2006 6FC5397 0BP10 2BA0 ...
Page 1996: ...Index Basic logic functions Tool Offset W1 208 Function Manual 11 2006 6FC5397 0BP10 2BA0 ...
Page 2150: ...Table of contents Basic logic functions Appendix 4 Function Manual 11 2006 6FC5397 0BP10 2BA0 ...
Page 2184: ...Glossary Basic logic functions Appendix 38 Function Manual 11 2006 6FC5397 0BP10 2BA0 ...