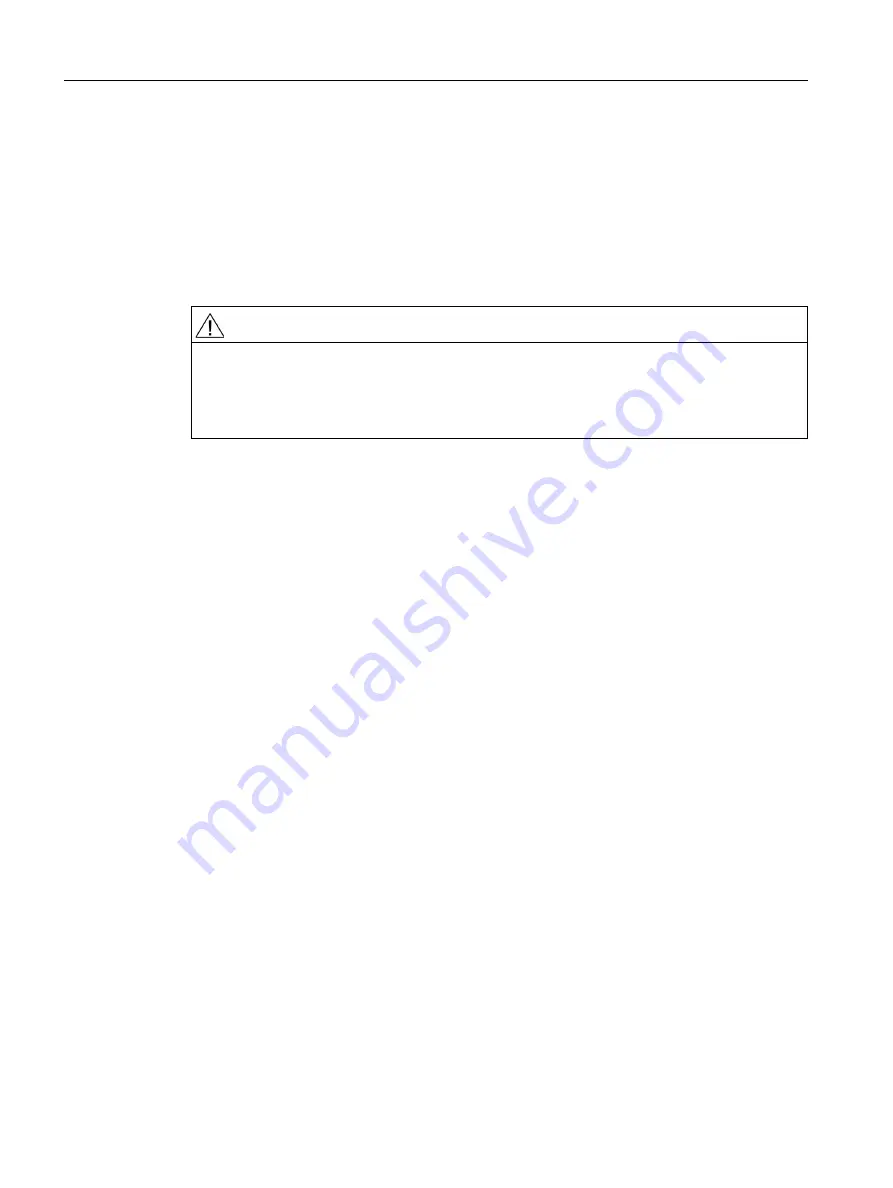
G2: Velocities, setpoint / actual value systems, closed-loop control
7.6 Optimization of the control
Basic Functions
386
Function Manual, 09/2011, 6FC5397-0BP40-2BA0
7.6.3
Position control with proportional-plus-integral-action controller
Function
As standard, the core of the position controller is a P controller.
It is possible to switch-in an integral component for special applications (such as an electronic gear). The
resulting proportional-plus-integral-action controller then corrects the error between setpoint and actual positions
down to zero in a finite, settable time period when the appropriate machine data are set accordingly.
Procedure
1. First optimize the position control loop as a proportional-action controller first using the tools described in the
previous subsections.
2. Increase the tolerances of the following machine data while measurements are being taken to determine the
quality of the position control with proportional-plus-integral-action controller:
- MD36020 $MA_POSITIONING_TIME
- MD36030 $MA_STANDSTILL_POS_TOL
- MD36040 $MA_STANDSTILL_DELAY_TIME
- MD36400 $MA_CONTOUR_TOL
3. Activate the position control loop as a proportional-plus-integral-action controller by setting the following
machine data:
MD32220 $MA_POSCTRL_INTEGR_ENABLE ; set value 1
MD32210 $MA_POSCTRL_INTEGR_TIME ; integral time [sec.]
Effect of integral time:
- T
n
→ 0:
The control error is corrected quickly; however, the control loop can become instable.
- T
n
→ ∞ :
The control error is corrected more slowly.
4. If you search for the optimum compromise for T
n
.
T
n
for the application between these two extreme cases, you should not select the value to be too close to the
instability limit, as otherwise, instability could occur and in turn damage the machine.
5. Use servo trace to trace the travel-in of an automatic program traveling to and from a target position.
CAUTION
When the proportional-plus-integral-action controller is active, overshoots occur in the actual
position. In this instance, you must decide whether this effect is admissible or acceptable for
the application in question. Closed-loop control know-how and measurements using the
servo trace are absolutely necessary in order to use the function. If the appropriate machine
data are incorrectly set, then machines could be damaged due to instability.