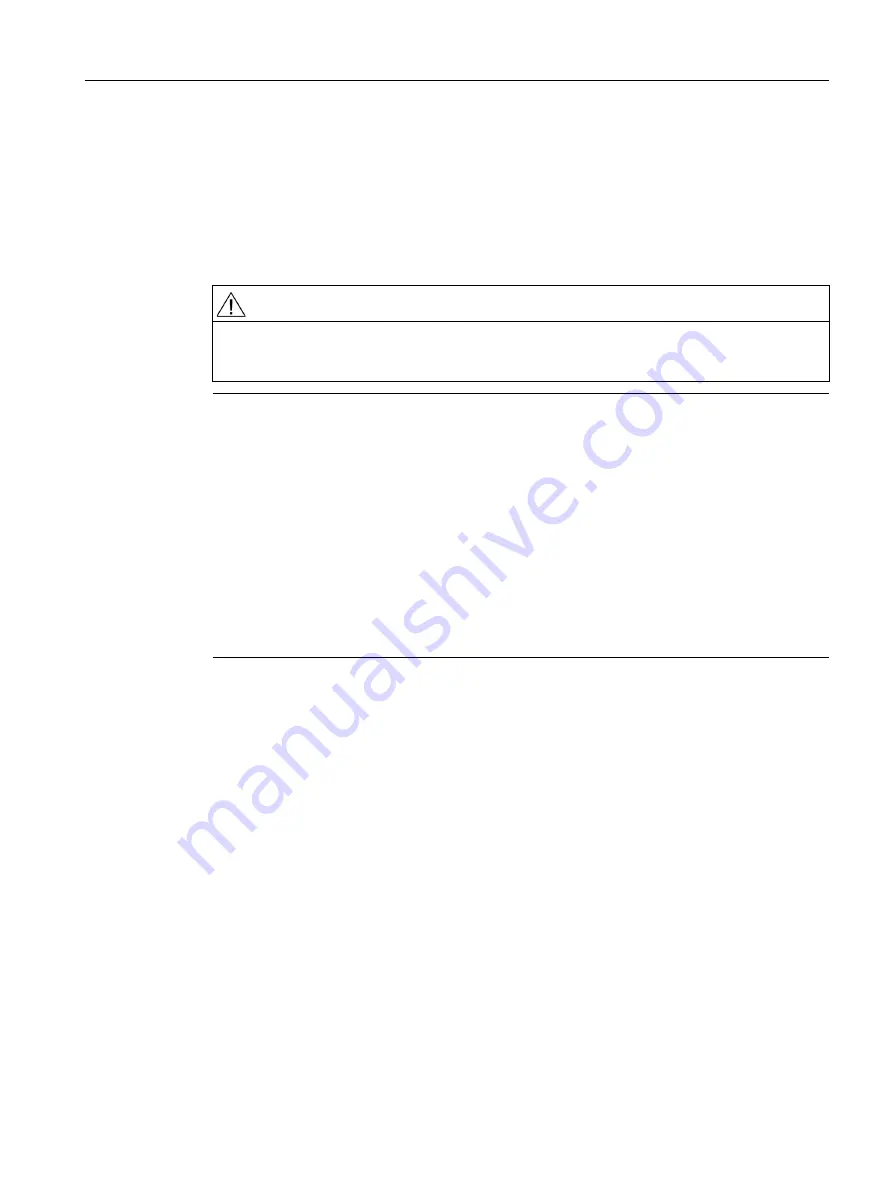
G2: Velocities, setpoint / actual value systems, closed-loop control
7.4 Setpoint/actual-value system
Basic Functions
Function Manual, 09/2011, 6FC5397-0BP40-2BA0
361
Reference point and position reference
In the case of gear changes, it is not possible to make a statement about the effect of the reference point or
machine position reference on the encoder scaling. In such cases, the control partially cancels the status "Axis
referenced/synchronized".
If the position reference to the machine, tool, etc., has been lost, it must first be restored through appropriate
adjustment or referencing of the lost reference point. This is especially important for the functions Travel to fixed
stop, Referencing to Bero, Cam and Zero marker.
7.4.4
Speed setpoint output
Control direction and travel direction of the feed axes
You must determine the travel direction of the feed axis before starting work.
Control direction
Before the position control is started up, the speed controller and current controller of the drive must be started
up and optimized.
Travel direction
With the machine data:
MD32100 $MA_AX_MOTION_DIR (travel direction).
the direction of motion of the axis can be reversed,
without affecting the control direction of the position control.
CAUTION
The control cannot detect all possible situations that can lead to loss of the machine position
reference. Therefore, it is the responsibility of the commissioning engineer or user to initiate
explicit referencing of zero marker synchronization in such cases.
Note
In order to permit new referencing without an interrupting RESET,
machine data:
MD34080 $MA_REFP_MOVE_DIST
and
MD34090 $MA_REFP_MOVE_DIST_CORR
are changed over to NewConfig effectiveness.
For more detailed information about referencing, please see:
References:
/FB1/ Functions Manual Basic Functions; Reference Point Travel (R1)