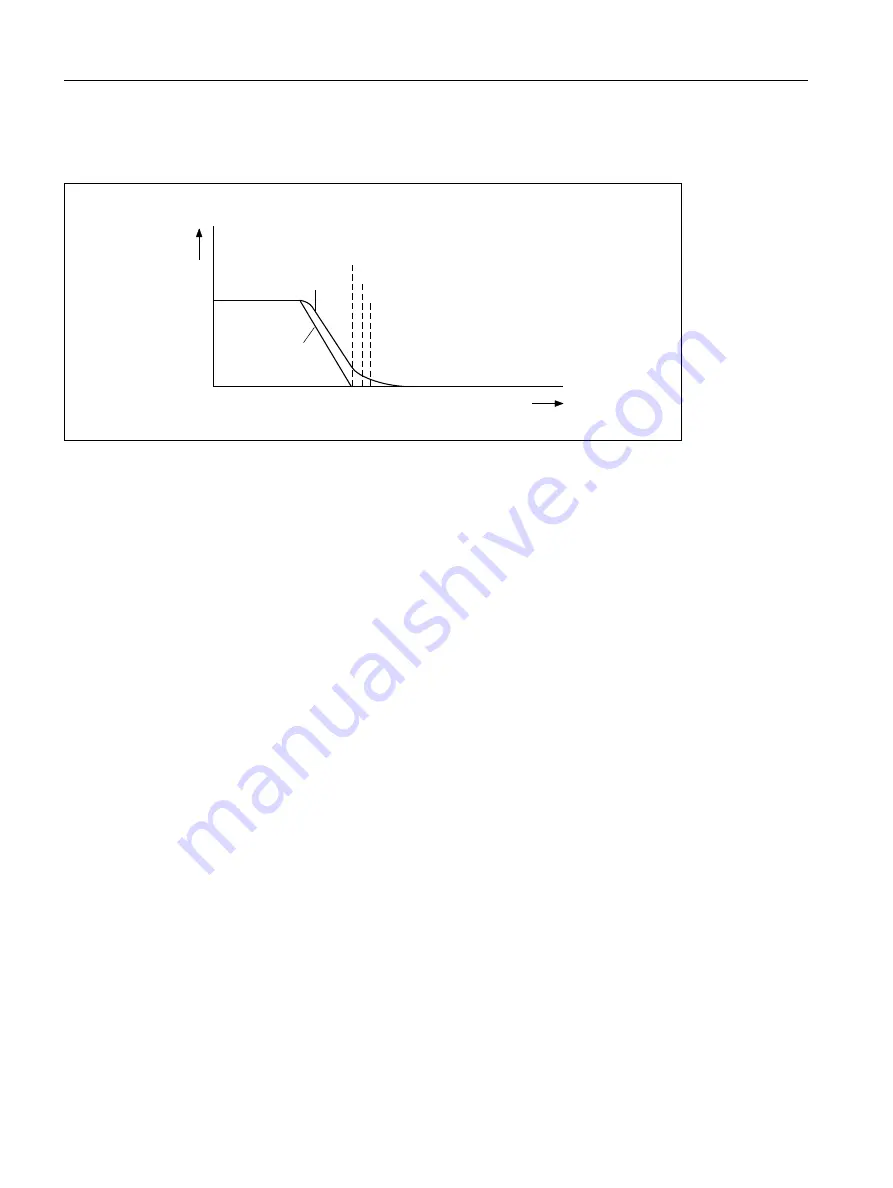
B1: Continuouspath Mode, Exact Stop, LookAhead
3.2 Exact stop mode
Basic Functions
152
Function Manual, 09/2011, 6FC5397-0BP40-2BA0
Block change depending on exact-stop criteria
The figure below illustrates the block change timing in terms of the selected exact stop criterion.
Figure 3-2
Block change accordance to selected exact stop criterion
Evaluation factor for exact stop criteria
A parameter set-dependent evaluation of the exact stop criteria can be specified via the following axis-specific
machine data:
MD36012 $MA_STOP_LIMIT_FACTOR (exact stop coarse/fine and standstill factor)
Applications:
• Adaptation of the positioning response to different mass ratios, such as after a gearshift
• Reduction in positioning time, depending on various machining states, such as roughing and finishing
Assignable specification of the active exact stop criterion
The active exact stop criterion can be permanently specified for the part program commands of the first
G function group irrespective of the exact stop criterion programmed in the part program. This specification can
be made independently for each of the following part program commands:
• Rapid traverse:
G0
• Machining commands:
G1
,
G2
,
G3
,
CIP
,
ASPLINE
,
BSPLINE
,
CSPLINE
,
POLY
,
G33
,
G34
,
G35
,
G331
,
G332
,
OEMIPO01
,
OEMIPO02
,
CT
The setting is done in a channel-specific manner via the following machine data:
MD20550 $MC_EXACT_POS_MODE (exact stop conditions for G0 and G1)
Coding
Each exact stop criterion is location-coded:
MD20550 $MC_EXACT_POS_MODE = <ZE>
• Ones position E: Rapid traverse
• Tens position Z: all other part program commands in the first G function group
6HWSRLQW
$FWXDOYDOXH
:LWK*
:LWK*
:LWK*
%ORFNFKDQJH
Y
W