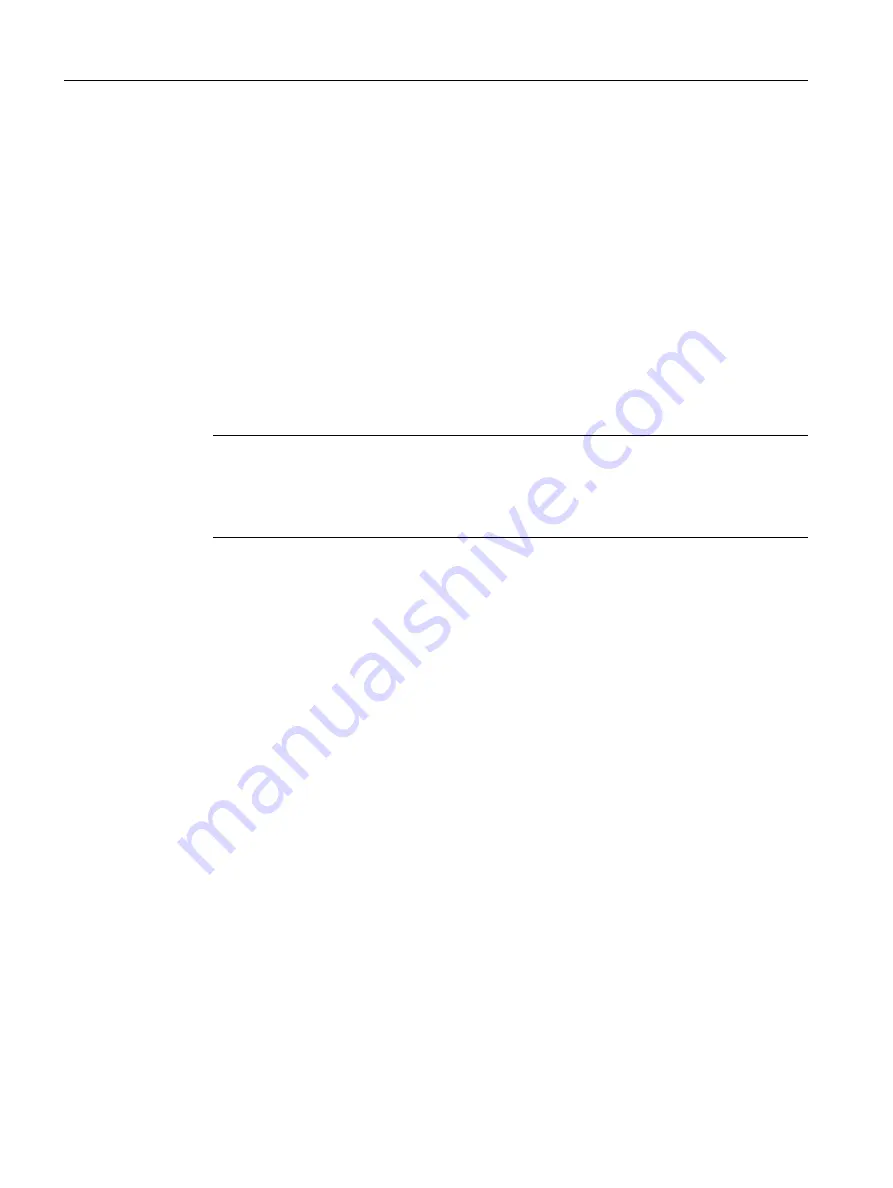
W1: Tool offset
18.2 Tool
Basic Functions
1428
Function Manual, 09/2011, 6FC5397-0BP40-2BA0
• If tool management is active,
D4
refers to tool "5".
T2=50 defines the tool for the secondary spindle, whose tool does not influence the path compensation. The
path is determined exclusively by the tool programmed for the master spindle.
•
D4
relates to tool "50" without active tool management and with the machine data:
MD20096 $MC_T_M_ADDRESS_EXT_IS_SPINO = FALSE (significance of address extension on T, M tool
change).
The address extensions of neither T nor M are evaluated in the NCK.
Each tool change command defines a new path compensation.
•
D4
relates to tool "5" (as when tool management is active) without active tool management and with the
machine data:
MD20096 $MC_T_M_ADDRESS_EXT_IS_SPINO = TRUE.
Address extension 1 (
T1=
...,
M1=
...) addresses the master spindle.
18.2.5
Free assignment of D numbers
"Relative" D numbers
In the NCK, it is possible to manage the D numbers as "relative" D numbers for the tool compensation data sets.
The corresponding D numbers are assigned to each T number. The maximum number of D numbers was
previously limited to 9.
Note
Previously, when tool management was not activated, each tool change command
(programmed with T or M) caused the tool compensation to be recalculated in the path.
The address extension is not defined further by this operation. The significance of the
extension is defined by the user (in the PLC user program).