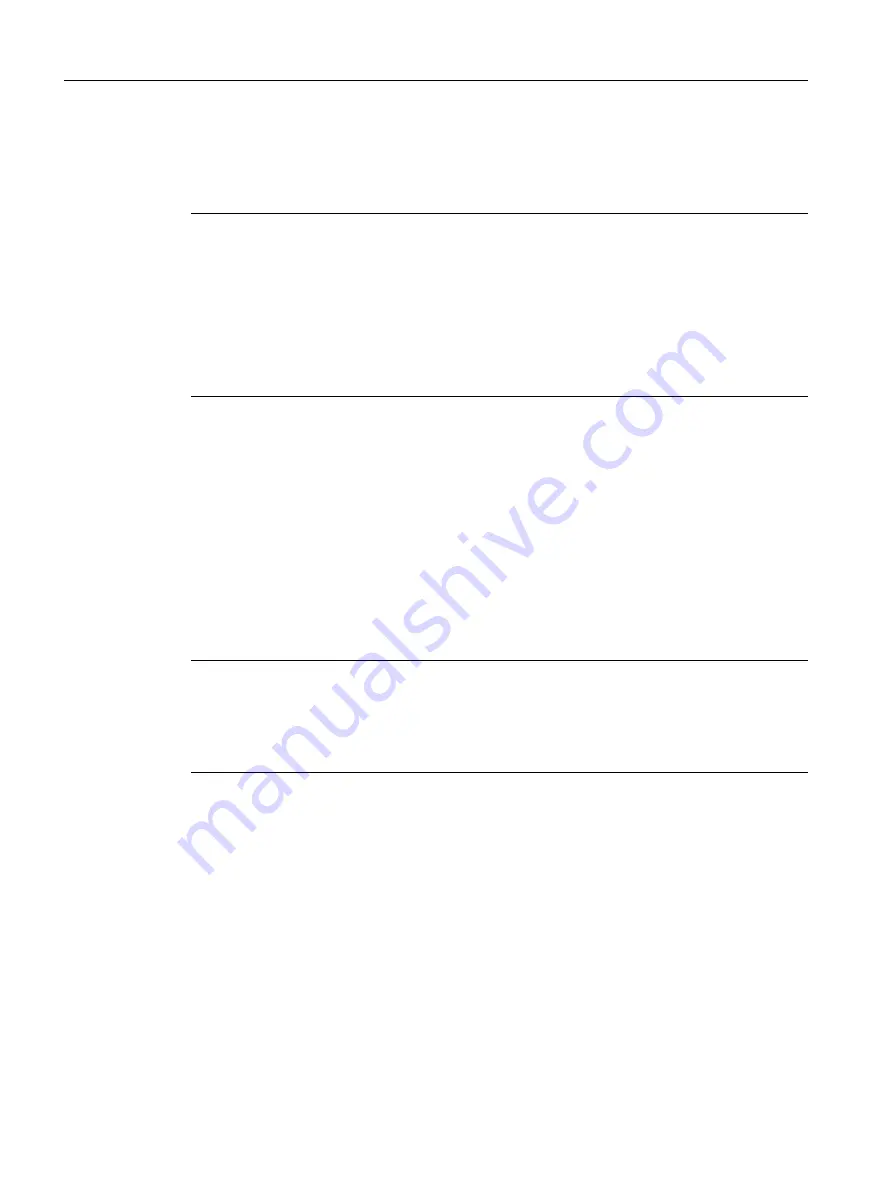
S1: Spindles
16.2 Operating modes
Basic Functions
1270
Function Manual, 09/2011, 6FC5397-0BP40-2BA0
Phase 5
Spindle speed > Position-control activation speed
Position control remains active and holds the spindle in the programmed position.
Spindle speed < Position-control activation speed (Phase 5, 5a)
The spindle is stationary and it has reached the position. The position control is active and stops the spindle in
the programmed position.
If the distance between the spindle actual position and the programmed position (spindle setpoint position) is less
than the configured exact stop fine and coarse limits, the following NC/PLC interface signals are set:
DB31, ... DBX60.7 (Position reached with coarse exact stop)
DB31, ... DBX60.7 (Position reached with fine exact stop)
The exact stop limits are defined with the machine data:
MD36010 $MA_STOP_LIMIT_FINE (exact stop fine)
MD36000 $MA_STOP_LIMIT_COARSE (exact stop coarse)
Note
The maximum encoder limit frequency of the spindle position actual-value encoder is
monitored by the control (it may be exceeded); in position control mode, the setpoint speed is
reduced to 90% of the measuring system limit speed.
The following NC/PLC interface signal is set:
DB31, ... DBX83.1 (programmed speed too high)
If "MS limit frequency exceeded" is still pending following a reduction in the setpoint speed,
an alarm is output.
Note
The positioning procedure is considered complete when the end-of-positioning criterion is
reached and signaled.
The condition is "Exact stop fine". This applies to
SPOS
,
M19
or
SPOSA
from the part program,
synchronized actions and spindle positioning by the PLC using FC 18.