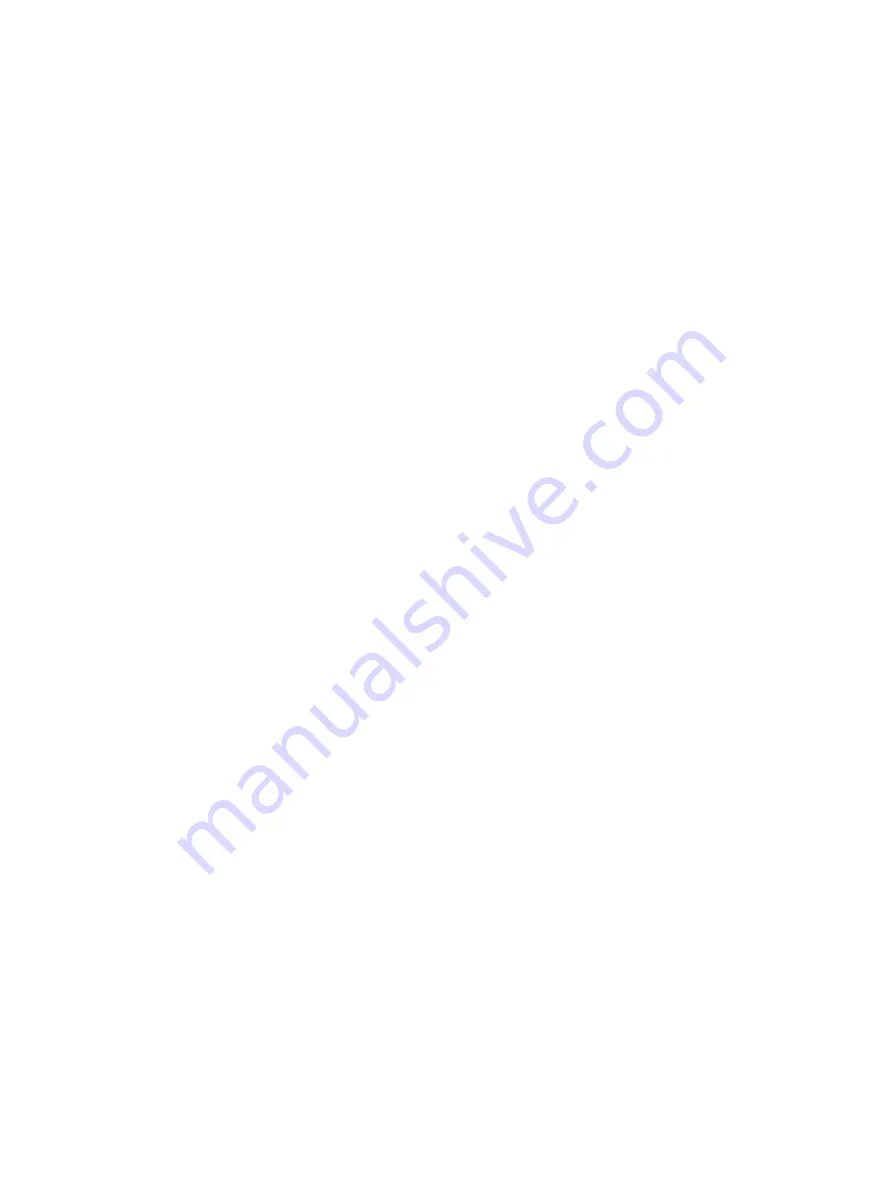
Basic Functions
Function Manual 09/2011, 6FC5397-0BP40-2BA0
1199
15
R1: Reference point approach
15.1
Brief Description
Function
The "Reference Point Approach" function is used to synchronize the measuring system of a machine axis with
machine zero. The machine axis is traversed to machine zero and the measuring system set to zero.
If it is not possible to approach machine zero directly, a reference point within the traversing range of the machine
axis is used whose position with reference to machine zero precisely known.
After the reference point approach, the measuring system of the machine axis is not set to zero but to the
corresponding reference point value.
Measuring systems and referencing methods
The "Reference point approach" function enables machine axes to be referenced using the following measuring
systems and referencing methods:
• Measuring systems
- Incremental rotary measuring system with at least one zero mark
- Incremental linear measuring system
- Rotary measuring system with distancecoded reference marks (supplied by Heidenhain)
- Linear measuring system with distancecoded reference marks (supplied by Heidenhain)
- Absolute rotary measuring system
- Absolute linear measuring system
• Referencing methods
- Referencing with incremental measuring systems with BERO and one-edge and two-edge detection
- Referencing with incremental measuring systems with replacement of homing cam with BERO
- Referencing with incremental measuring systems with BERO with configured approach velocity for spindle
applications
- Referencing with measuring systems with distancecoded reference marks by overtravelling 2 or 4 zero
marks
- Referencing of passive measuring systems using measuring system adjustment
- Referencing in followup mode
- Referencing with cam switch at the drive
Start
The reference point approach of a machine axis can be started manually or via the part program:
• Manual: Operation mode JOG and MDA, machine function REF
• Part program: Part program command
G74