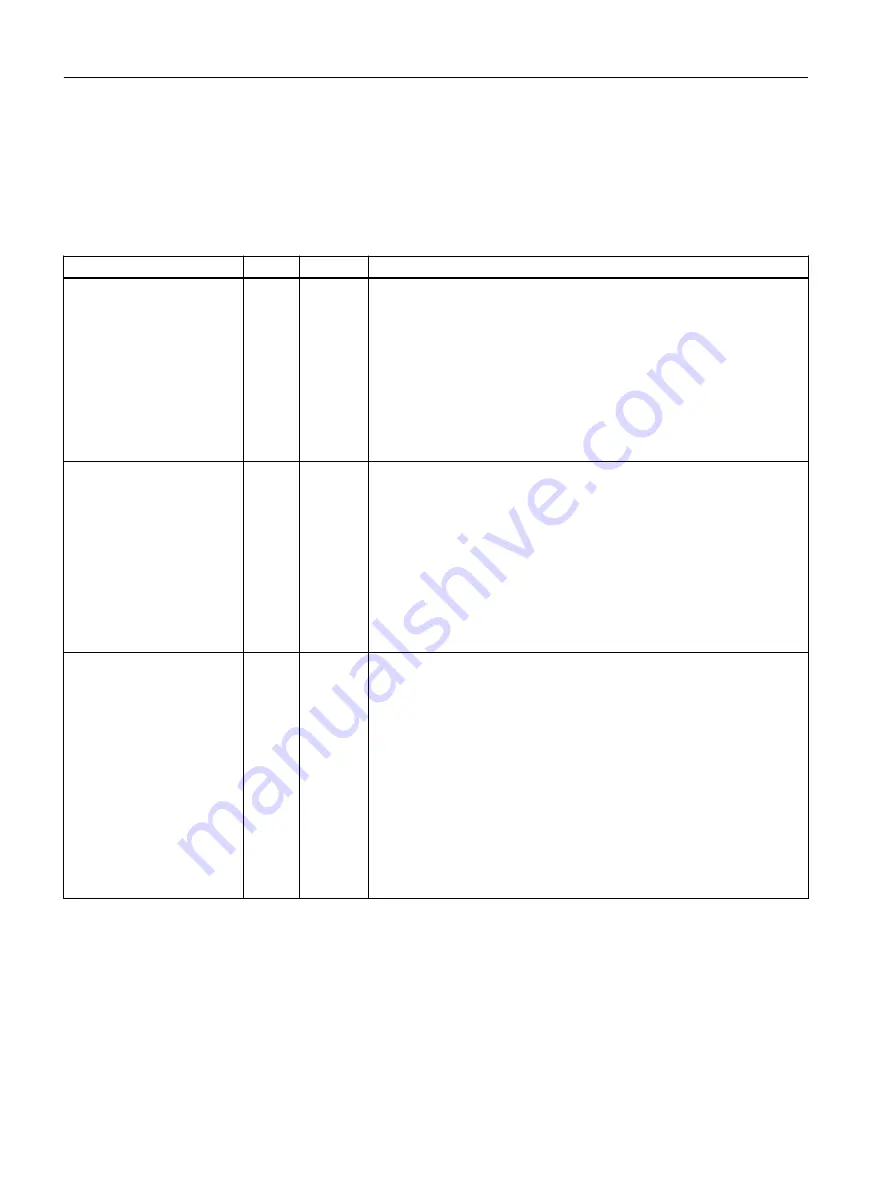
11.9
Drive Faults and Alarms User I/O Related
Handling Internal (User) I/O Related Faults
Table 11-8
Internal (user) I/O related faults
Fault display
Type
Enable
Potential causes and corrective actions
Loss of signal (1 to 12)
A
Menu/
SOP
Cause
The software detected a loss of signal on one of the 4 to 20 mA inputs (1
to 12). This is usually a result of an open circuit or defective driver on the
current loop.
Action
1. Check connection to the user I/O module's 4 to 20 mA input corre‐
sponding to the loss of signal message and associated wiring.
2. Replace affected user I/O module.
3. Contact Siemens customer service.
Int I/O Comm Fault
F
Fixed
Cause
This fault occurs when the system has had a problem communicating to a
user I/O module. A number attached to the fault message will indicate
which module the system was trying to communicate with when the error
occurred. However, this number may not always be the actual module
which has a problem. Noise on the fiber optic network may give cause an
erroneous result.
Action
1. Replace affected user I/O module.
2. Contact Siemens customer service.
Int I/O Internal Err
F
Fixed
Cause
This fault occurs when a module reports an error. The three types of mod‐
ule errors which are reported and therefore can generate this fault are:
• EEprom error
• board type error
• watchdog time out.
Which of those errors actually generated the fault may be identified by the
flashing LEDs on the module which reported the error. A number attached
to the fault message will indicate which module reported the error.
Action
1. Replace affected user I/O module.
2. Contact Siemens customer service.
Troubleshooting Faults and Alarms
11.9 Drive Faults and Alarms User I/O Related
Control Manual
460
Operating Manual, A5E50491925A
Summary of Contents for SINAMICS PERFECT HARMONY GH180
Page 2: ......
Page 22: ...Table of contents NXGPro Control Manual 20 Operating Manual A5E50491925A ...
Page 24: ...Security NXGPro Control Manual 22 Operating Manual A5E50491925A ...
Page 504: ...NEMA Table NXGPro Control Manual 502 Operating Manual A5E50491925A ...
Page 517: ...Index D NXGPro Control Manual Operating Manual A5E50491925A 515 ...
Page 518: ...Index NXGPro Control Manual 516 Operating Manual A5E50491925A ...
Page 530: ...Glossary NXGPro Control Manual 528 Operating Manual A5E50491925A ...
Page 537: ......