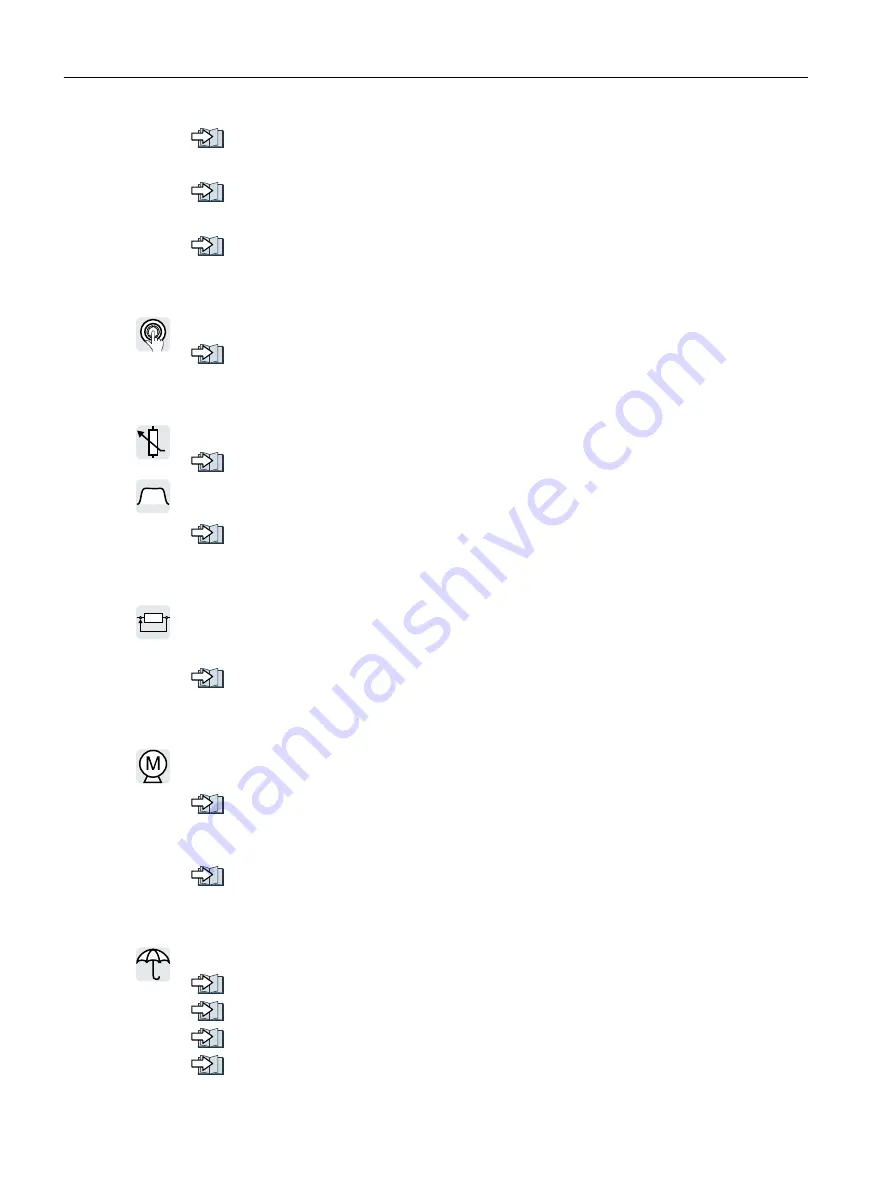
Motor holding brake (Page 206)
The free function blocks permit configurable signal processing within the inverter.
Free function blocks (Page 210)
You can select in which physical units the inverter represents its associated values.
Selecting physical units (Page 211)
Safety functions
The safety functions fulfill increased requirements regarding the functional safety of the drive.
Safe Torque Off (STO) safety function (Page 215)
Setpoints and setpoint conditioning
The setpoint generally determines the motor speed.
The setpoint processing uses a ramp-function generator to prevent speed steps occurring and
to limit the speed to a permissible maximum value.
Setpoint calculation (Page 243)
Technology controller
The technology controller controls process variables, e.g. pressure, temperature, level or flow.
The motor closed-loop control either receives its setpoint from the higher-level control - or from
the technology controller.
PID technology controller (Page 252)
Motor control
The motor closed-loop control ensures that the motor follows the speed setpoint. You can
choose between various control modes.
The inverter has various methods to electrically brake the motor. When electrically braking,
the motor develops a torque, which reduces the speed down to standstill.
Electrically braking the motor (Page 283)
Drive protection
The protection functions prevent damage to the motor, inverter and driven load.
Overcurrent protection (Page 292)
Inverter protection using temperature monitoring (Page 293)
Motor protection with temperature sensor (Page 296)
Motor protection by calculating the temperature (Page 299)
3,'
Advanced commissioning
6.1 Overview of the inverter functions
SINAMICS G120C converter
158
Operating Instructions, 09/2017, FW V4.7 SP9, A5E34263257B AF