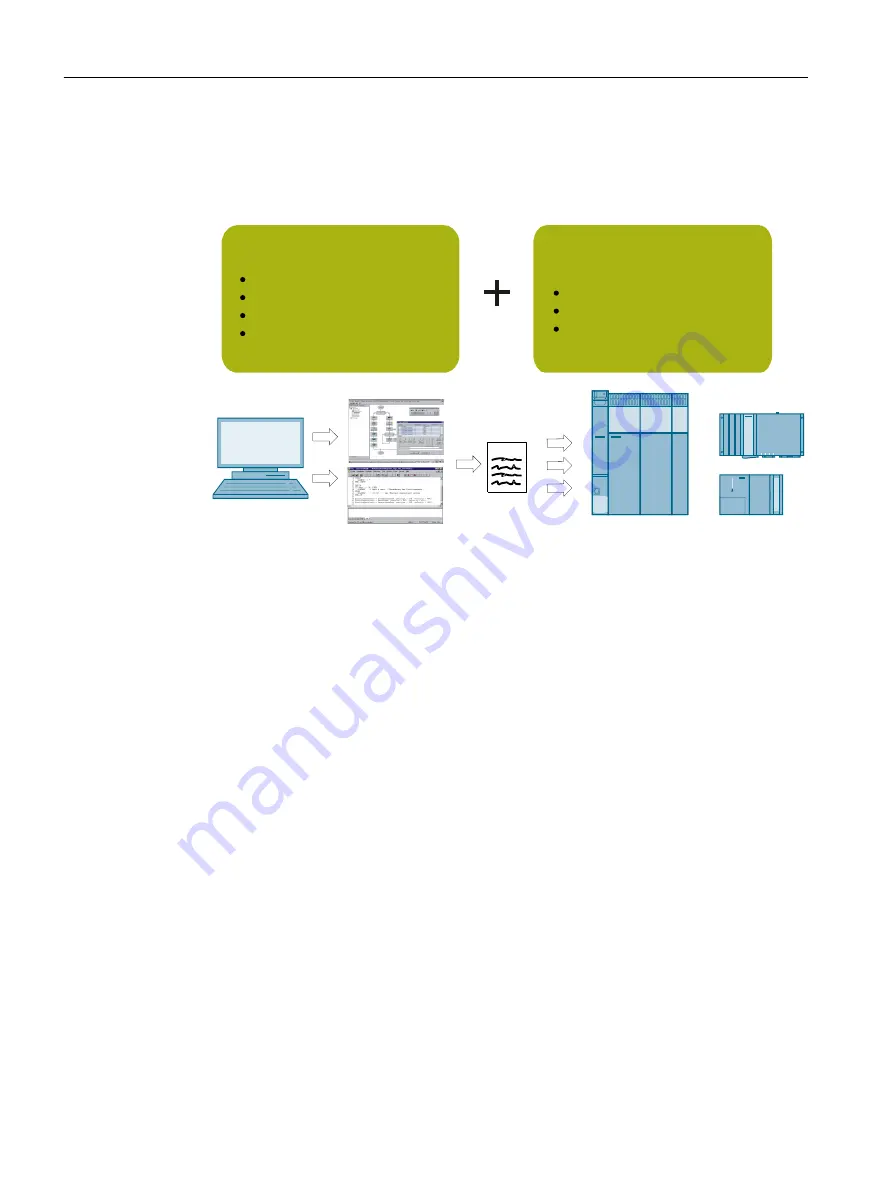
The following tasks are graphically supported with operator guidance:
● Creation of the hardware and network configuration
● Creation, configuration and parameter assignment of technology objects
such as axes, output cams and cams.
6,027,21'
6,027,21&
6,027,213
21(UXQWLPHV\VWHPIRU
YDULRXVSODWIRUPV
7HFKQRORJ\SDDUGZDUHSODWIRUPV
6,027,216&287
HQJLQHHULQJV\VWHP
21(6&287HQJLQHHULQJV\VWHP
57FRGH
IRUFRQILJXULQJ
SDUDPHWHUL]LQJJUDSKLFRU
WH[WXDOSURJUDPPLQJ
IRUGLDJQRVWLFVWURXEOHVKRR
WLQJGHEXJJLQJ
&RQWUROOHUEDVHG6,027,21&
3&EDVHG6,027,213
'ULYHEDVHG6,027,21'
Figure 3-1
SIMOTION system overview
The automation topology is defined in the first engineering steps. The hardware and network
configuration is created by parameterizing the required components and networks.
3.3
SIMOTION hardware platforms
To meet the complex requirements of machine construction, SIMOTION offers three hardware
variants with different performance, packaging formats and expandability options. The basic
system characteristics, like the engineering, are identical.
SIMOTION D (Drive-based)
SIMOTION D is a compact, drive-based version of SIMOTION based on the SINAMICS S120
drives family. For SIMOTION D, the SIMOTION runtime environment and the SINAMICS drive
software run concurrently on the controller hardware in the SINAMICS S120 packaging format.
SIMOTION P (PC-based)
SIMOTION P is a PC-based, open motion control system from SIMOTION. Control, motion
control, and HMI functions are executed together with standard PC applications on the
SIMOTION P hardware platform.
Introduction
3.3 SIMOTION hardware platforms
SIMOTION SCOUT
18
Configuration Manual, 11/2016