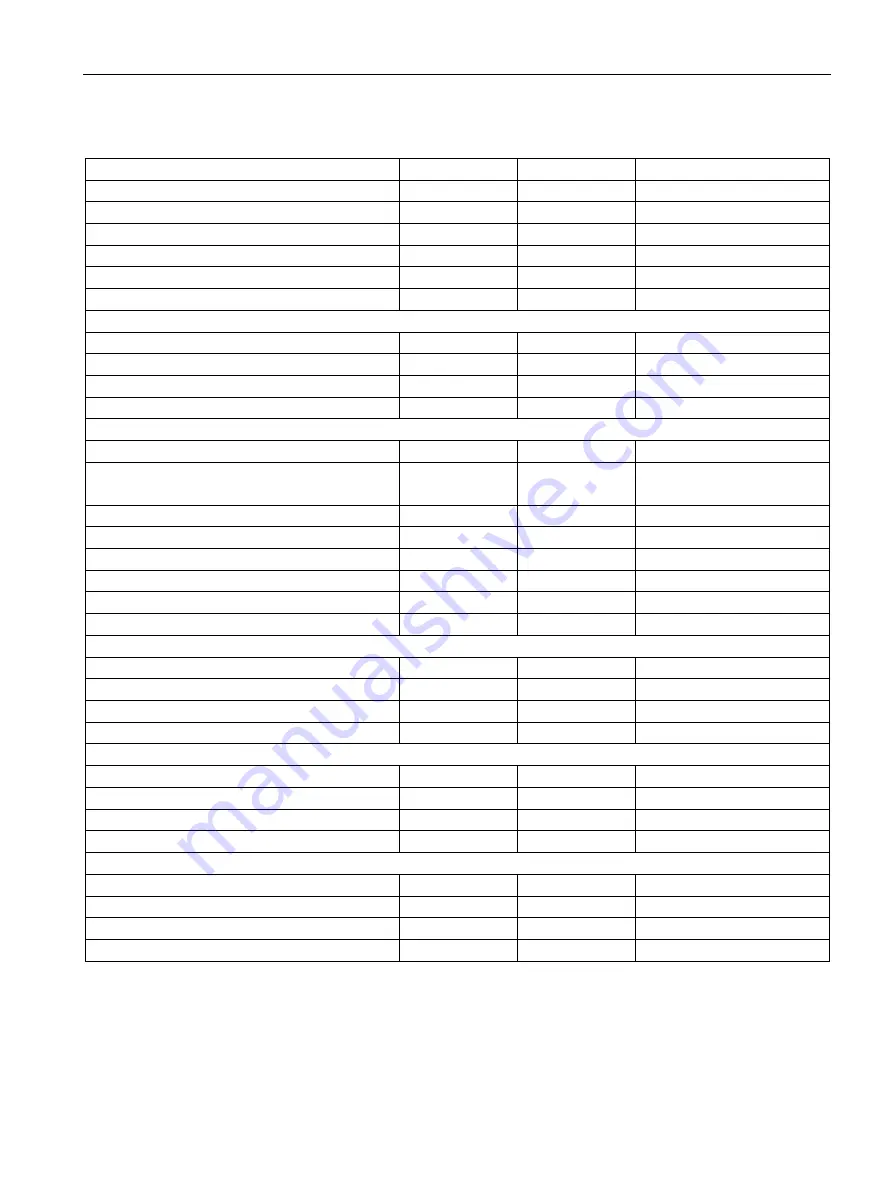
Technical data and characteristics
6.3 Data sheets and characteristics
1FW3 complete torque motors
Configuration Manual, 08/2020, A5E46027705B AA
219
Table 6- 33 1FW3206, rated speed 300 rpm
Engineering data
Code
Unit
1FW3206-1
☐
H
Rated speed
n
N
rpm
300
Rated torque (100 K)
M
N (100 K)
Nm
1500
Rated power (100 K)
P
N (100 K)
kW
47.0
Rated current (100 K)
I
N (100 K)
A
118
Static torque (100 K)
M
0 (100 K)
Nm
1575
Stall current (100 K)
I
0 (100 K)
A
121
Limiting data
Max. permissible speed (mech.)
n
max mech.
rpm
1000
Max. permissible speed (converter)
n
max Inv
rpm
700
Maximum torque
M
max
Nm
2775
Maximum current
I
max
A
255
Motor data
Number of poles
2p
28
Ratio of speed measurement
(belt-driven encoder)
i
enc
--
-3.5
Torque constant (100 K)
k
T(100 K)
Nm/A
12.8
Voltage constant (at 20 °C)
k
E
V/1000 rpm
820
Winding resistance (at 20 °C)
R
ph
Ω
0.076
Rotating field inductance
L
D
mH
2.7
Electrical time constant
T
el
ms
35.5
Thermal time constant
T
th
min
16.0
Mechanical data: Hollow-shaft version
Mechanical time constant
T
mech
ms
1.3
Moment of inertia
J
mot
kgm
2
0.97
Shaft torsional stiffness
c
t
Nm/rad
1.24E+07
Weight
m
kg
280
Mechanical data: Solid shaft version
Mechanical time constant
T
mech
ms
1.2
Moment of inertia
J
mot
kgm
2
0.84
Shaft torsional stiffness
c
t
Nm/rad
1.24E+07
Weight
m
kg
345
Mechanical data: Plug-on shaft version
Mechanical time constant
T
mech
ms
1.3
Moment of inertia
J
mot
kgm
2
0.94
Shaft torsional stiffness
c
t
Nm/rad
2.65E+07
Weight
m
kg
315
The specified rated data are valid for a 600 V DC link voltage
Summary of Contents for SIMOTICS T-1FW3
Page 1: ...1FW3 complete torque motors ...
Page 2: ......
Page 8: ...Introduction 1FW3 complete torque motors 6 Configuration Manual 08 2020 A5E46027705B AA ...
Page 12: ...Table of contents 1FW3 complete torque motors 10 Configuration Manual 08 2020 A5E46027705B AA ...
Page 353: ......
Page 354: ......