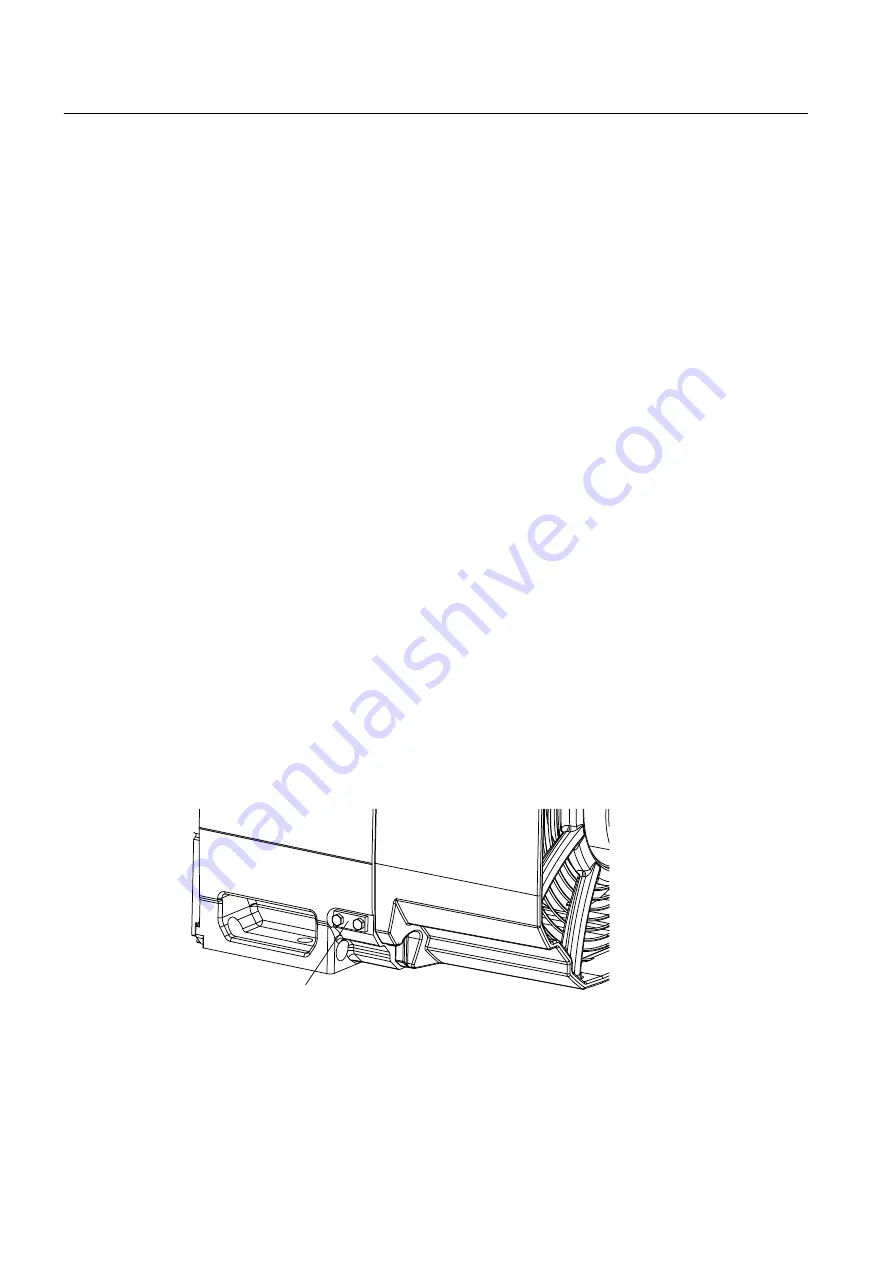
6.1
Preparation
6.1.1
Selecting cables
Take the following criteria into account when selecting the connecting cables:
● Rated current
● Rated voltage
● If required, service factor
● System-dependent conditions, such as ambient temperature, routing type, cable cross-
section as defined by required length of cable, etc.
● Configuration notes
● Requirements according to IEC/EN 60204‑1
6.1.2
Connect up the ground conductor
The grounding conductor of the motor must be in full conformance with the installation
regulations, e.g. in accordance with IEC/EN 60204-1.
● Connect the ground conductor to the end shield of the motor. There is a fixing lug
①
for
the ground conductor at the designated connection point.
– The fixing lug
①
is suitable for grounding high-frequency currents using HF ribbon cable
with appropriately formed conductor ends.
● When making connections, ensure the following:
– the connecting surface is bare and protected against corrosion using a suitable
substance, e.g. acid-free Vaseline
– the flat and spring washers are located under the bolt head.
Figure 6-1
Terminal lug
①
for the grounding conductor for a force-ventilated motor
Electrical connection
6.1 Preparation
SIMOTICS M-1PH8 1PH818., 1PH822., 1PH828.
68
Operating Instructions 10/2017
Summary of Contents for SIMOTICS M-1PH818
Page 2: ...20 10 2017 15 09 V20 00 ...
Page 14: ...Introduction SIMOTICS M 1PH8 1PH818 1PH822 1PH828 14 Operating Instructions 10 2017 ...
Page 28: ...Description SIMOTICS M 1PH8 1PH818 1PH822 1PH828 28 Operating Instructions 10 2017 ...
Page 104: ...Operation 8 10 Faults SIMOTICS M 1PH8 1PH818 1PH822 1PH828 104 Operating Instructions 10 2017 ...
Page 166: ...Quality documents SIMOTICS M 1PH8 1PH818 1PH822 1PH828 166 Operating Instructions 10 2017 ...
Page 171: ...171 ...
Page 172: ...172 ...
Page 173: ...173 ...
Page 174: ...174 ...
Page 175: ...175 ...
Page 176: ...176 ...
Page 177: ...177 ...
Page 178: ...178 ...
Page 179: ...179 ...
Page 180: ...180 ...
Page 181: ...181 ...
Page 182: ...182 ...
Page 183: ...183 ...
Page 184: ...184 ...
Page 185: ...185 ...
Page 186: ...186 ...
Page 187: ...187 ...
Page 188: ...188 ...
Page 189: ...189 ...
Page 190: ...190 ...
Page 191: ...191 ...
Page 192: ...192 ...
Page 278: ...278 ...
Page 308: ...308 ...