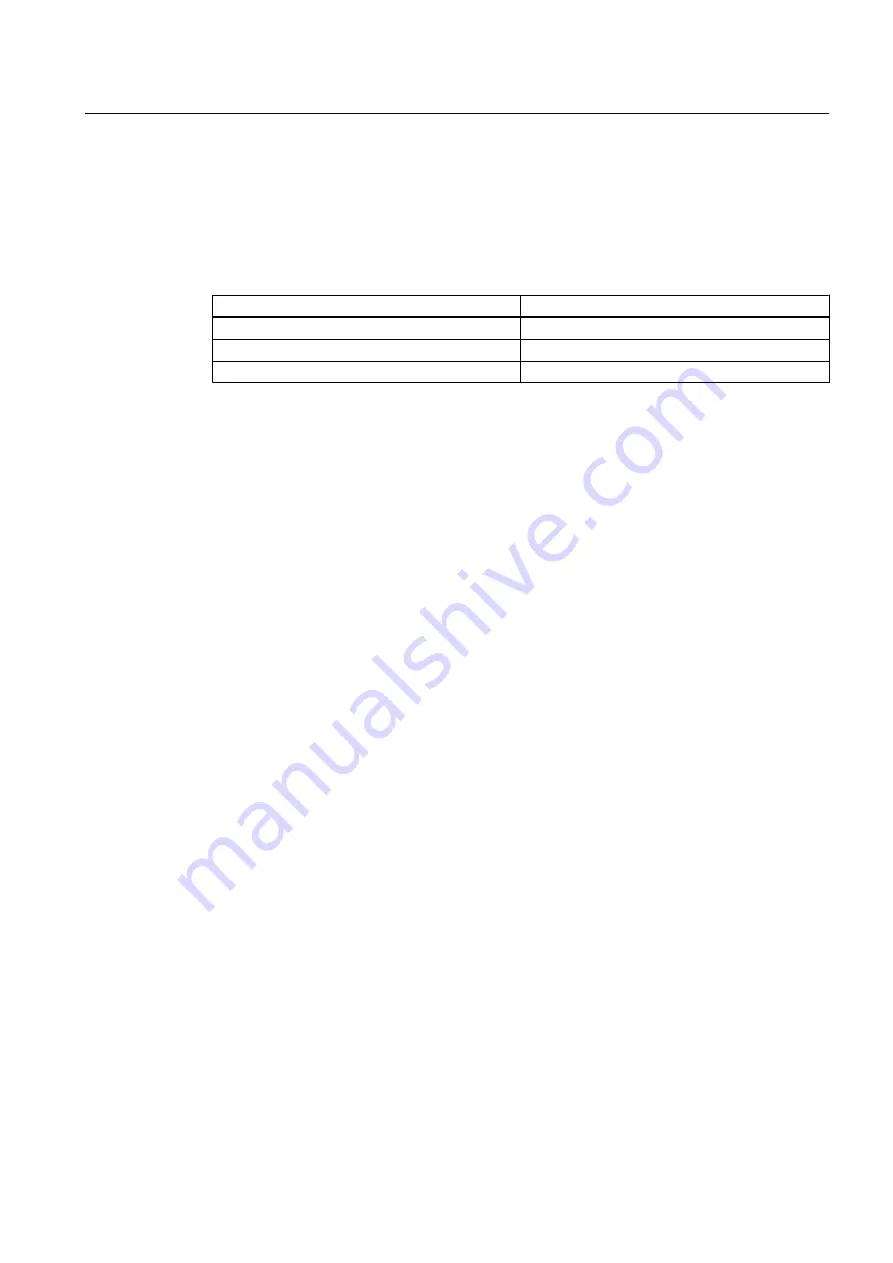
Example
This current limit corresponds to the following upper power limits, depending on the relationship
between the starting current I
A
and rated current I
N
and on the voltage dip (up to approximately
20%) while the machine is starting up:
Table 4-1
Power limits
Rated voltage V
N
Power limit
3 kV
750 kW
6 kV
1500 kW
10 kV
2500 kW
See also
Prior to commissioning (Page 71)
4.14
Thermal protection
The machine is equipped with measuring equipment to directly monitor the motor temperature
to protect the machine against overheating during operation. Plan a corresponding circuit for
monitoring. You will find more information in the Technical Data in the "Explanatory text for the
machine dimension drawing".
4.15
Transport and storage
Observe the following when carrying out any work on the machine:
● Comply with the general safety instructions (Page 13)
● Comply with the applicable national and sector-specific regulations at the place of
installation
● When using the machine within the European Union, comply with the specifications laid
down in EN 50110‑1 regarding safe operation of electrical equipment.
4.15.1
Transport markings
The packing differs depending on the transport type and size. If not otherwise contractually
agreed, the packaging corresponds to the packing guidelines for International Standards for
Phytosanitary Measures (ISPM).
Preparations for use
4.14 Thermal protection
SIMOTICS HV M 1RN76308PR900CG0-Z
Operating Instructions 07/2018
27
Summary of Contents for SIMOTICS HV M
Page 2: ...03 07 2018 13 28 V3 00 ...
Page 22: ...Description SIMOTICS HV M 1RN76308PR900CG0 Z 22 Operating Instructions 07 2018 ...
Page 86: ...Operation 8 11 Faults SIMOTICS HV M 1RN76308PR900CG0 Z 86 Operating Instructions 07 2018 ...
Page 122: ...Service and Support SIMOTICS HV M 1RN76308PR900CG0 Z 122 Operating Instructions 07 2018 ...
Page 128: ...Quality documents SIMOTICS HV M 1RN76308PR900CG0 Z 128 Operating Instructions 07 2018 ...
Page 130: ...Additional documents SIMOTICS HV M 1RN76308PR900CG0 Z 130 Operating Instructions 07 2018 ...
Page 135: ......