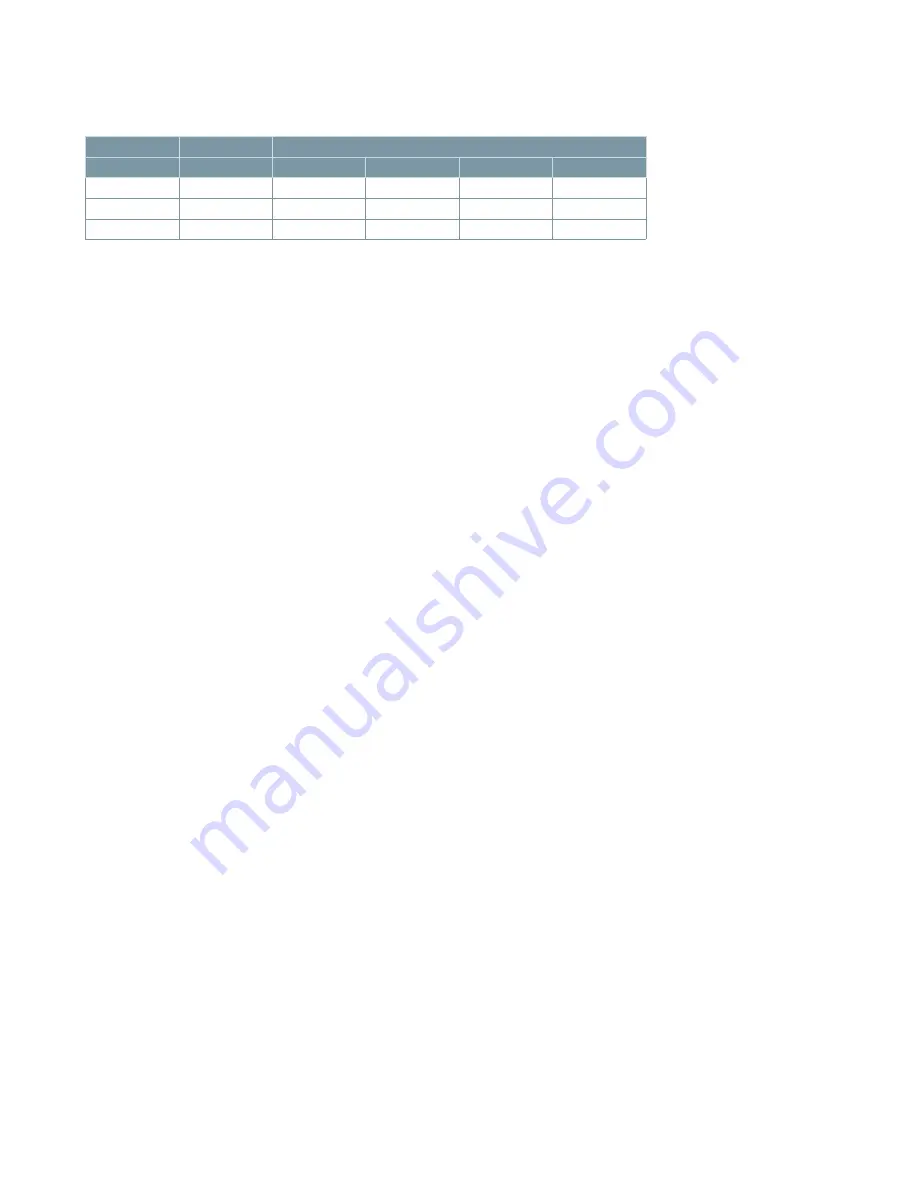
41
Insulation and contact-resistance test
procedure
1. Observe safety precautions listed in the
danger and caution advisories for the
vacuum integrity check tests.
2. Close the circuit breaker. Ground each
pole not under test. Use manual charging,
closing and tripping procedures.
3. Apply the proper high-potential test
voltage (refer to Table 2 (or 3): High-
potential test voltages on page 23 (or 33)
between a primary conductor of the pole
and ground for one minute.
4. If no disruptive discharge occurs, the
insulation system is satisfactory.
5. After test completion, ground both ends
and the middle arc chamber of the
vacuum interrupter to dissipate any static
charges.
6. Disconnect the leads to the spring-
charging motor.
7. Test each individual wire, when they are
connected to the operator 64-pin
plug,
connect the high-voltage tester to a
particular pin and ground the circuit
breaker housing. Starting with zero volts,
gradually increase the test voltage to
1,125 volts, 60 Hz (750 volts, 60 Hz on
pins A1 and D16 for motor circuit for
stored-energy operator). Maintain test
voltage for one minute.
8. If no disruptive discharge occurs, the
secondary control insulation level is
satisfactory.
9. Disconnect the shorting wire and reattach
the leads to the spring-charging motor.
10. Perform contact-resistance tests of the
primary contacts using a micro-
ohmmeter. Contact resistance should not
exceed the values listed in Table 6:
Maximum contact resistance (micro-
ohms). The contact resistance is measure
across the phase terminals (outside
terminals of roof bushings).
11. Make a permanent record of all tests
performed.
Inspection and cleaning of circuit breaker
insulation
1A. (For stored-energy operator) perform
the spring discharge check.
A. De-energize control power.
B. Press red open button on the
operating mechanism.
C. Press black close button on the
operating mechanism.
D. Again press red open button on the
operating mechanism.
E. Verify spring condition indicator shows
DISCHARGED.
F. Verify main contact status indicator
shows OPEN.
1B. (For magnetic-actuator operator) use the
manual opening handle on the right side
of the enclosure (refer to Figure 8: Relay
and control and operator compartments
for type SDV7-MA circuit breaker with
magnetic-actuator operator on page 30 to
open the circuit breaker.
2. Remove the phase barriers (if provided) as
shown in Figure 5: Type SDV7 distribution
circuit breaker with interphase barriers
and bushing current transformers
installed in primary compartment on
page 16.
Voltage
Interrupting
Continuous current
kV
kA
1,200 A
2,000 A
2,500 A
3,000 A
15.5
20/25/31.5/40
160
105
----
95
27.6
20/25
160
105
----
----
38.0
20/25/31.5/40
160
105
100
----
Table 6: Maximum contact
resistance (micro-ohms)
Summary of Contents for SDV7
Page 54: ...54 Table 16 Remarks ...
Page 55: ...55 Table 16 Remarks continued ...