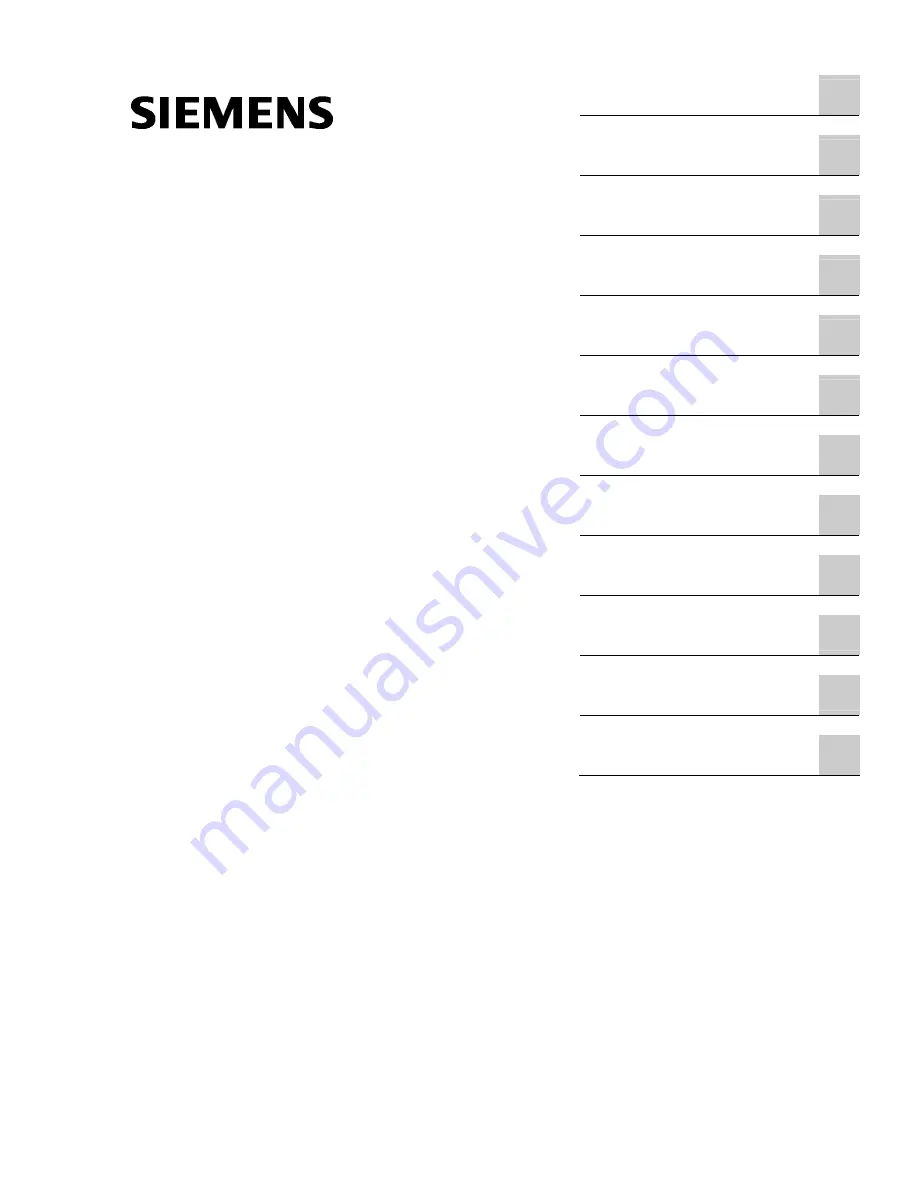
RF180C communication module
___________________
___________________
___________________
___________________
___________________
___________________
___________________
___________________
___________________
___________________
___________________
___________________
SIMATIC Ident
RFID systems
RF180C communication module
Operating Instructions
12/2012
J31069-D0177-U001-A6-7618
Introduction
1
Description
2
Installation
3
Connecting
4
Parameterization
5
Maintenance and service
6
Diagnostics
7
Technical data
8
Dimension drawings
9
Connecting cable to the
reader
10
Ordering data
11
Service & Support
12