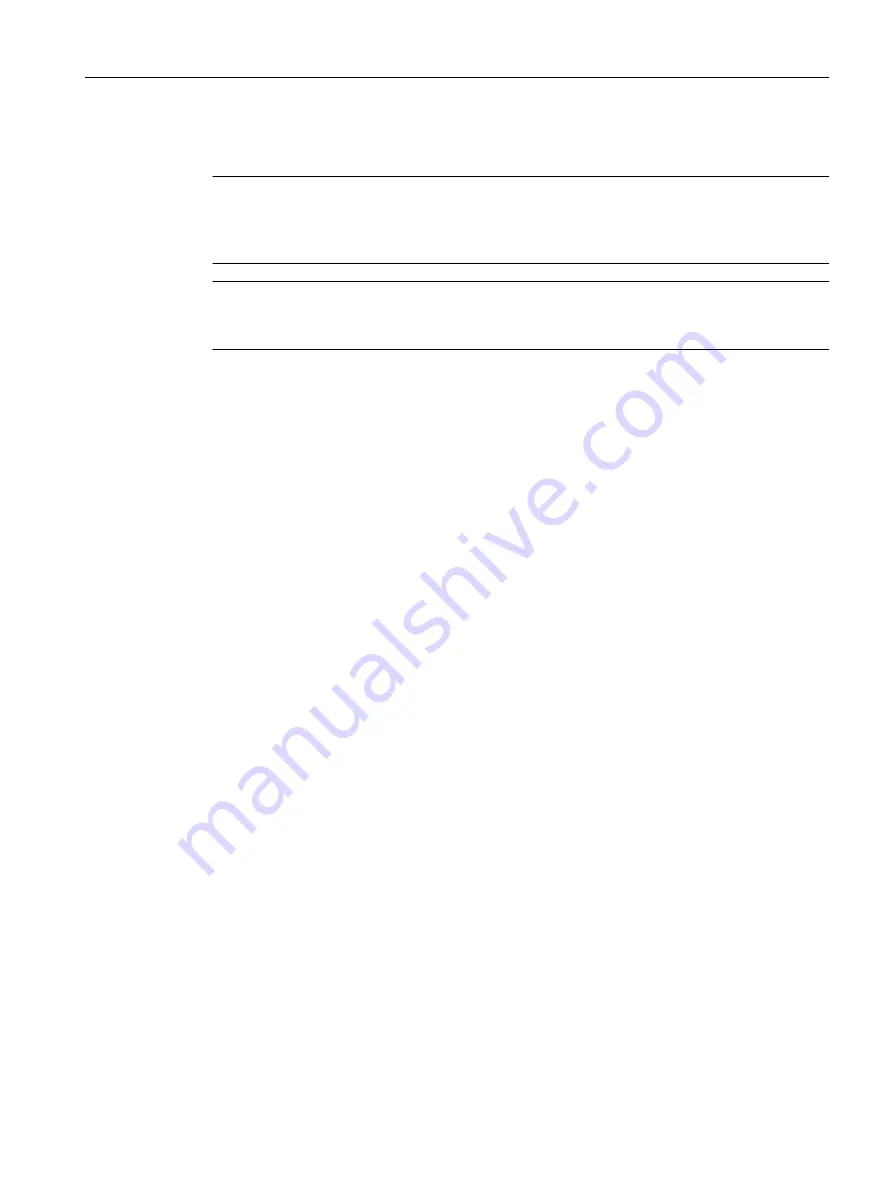
4.4.2.10
M20 Procedure - Actuator Reassembly
Note
It is extremely important that, when reassembling the actuator, that the assembly area be clean
and dust free. Hands of maintenance personnel must be clean and not oily and tools must also
be clean.
Note
Be certain valve cap (1) does not rest on abrasive surface and valve cap has completely air
dried before reassembly. Rest valve cap on a clean lint free cloth.
1. Install the three large Belleville washers (20) in cylinder valve base (14). Washers must be
positioned in an alternating bevel up, bevel down manner (to form a spring). Refer to Figures
5-1 and 5-2.
2. Apply a bead of Krytox 240 AC lubricant, or equivalent; in "O" ring grooves of spring-loaded
piston (15).
3. Install new silicon O-rings (18 and 19) in spring loaded piston (15) and apply a coating of
lubricant over each "O" ring.
4. Apply bead of lubricant in upper groove of air loaded piston (12a).
5. Install a new silicon "O" ring (19) in the upper groove of air loaded piston (12a) and apply
a coating of lubricant over the "O" ring.
6. Place upper piston (12a) over the small diameter of lower piston (15). Position pistons using
guide pin (12b) for proper orientation.
7. Apply Krytox 240C lubricant to each of the six finger spring (12c) pressure points. This is
the point where the spring fingers contact the plunger body (13).
8. Position the valve upright with its three ports on the left. Install a #6-32 screw in the center-
threaded hole of air loaded piston assembly (12) and bottom spring-loaded piston (15).
9. Lift the combined assembly (12 and 15), and orient it with the upper piston guide pin (12b)
facing toward maintenance person.
10.Press the piston assembly into the cylinder base (14). After installation, remove the #6-32
screw.
11.Align plunger valve body (13) and insert the piston guide pin (12b) into one of the three
bottom holes of plunger valve body (13).
12.Rotate plunger valve body (13) to align body screw holes with cylinder base (14) threaded
holes.
13.Install three #10-32 7/8" socket head screws (16) and Belleville washers (17).
14.Hand tighten screws. DO NOT compress the Belleville washers (20) into the cylinder base
(14).
15.Install six plungers (6) into the plunger valve body (13). Plunger recess must face up.
A clean plunger will fall with its own weight, and, when dropped into the valve body (13), it
will bounce.
Valves
4.4 Model 20 Valve
Maxum II Valves and Oven Components
Service Manual, 10/2018, A5E42019844001
65