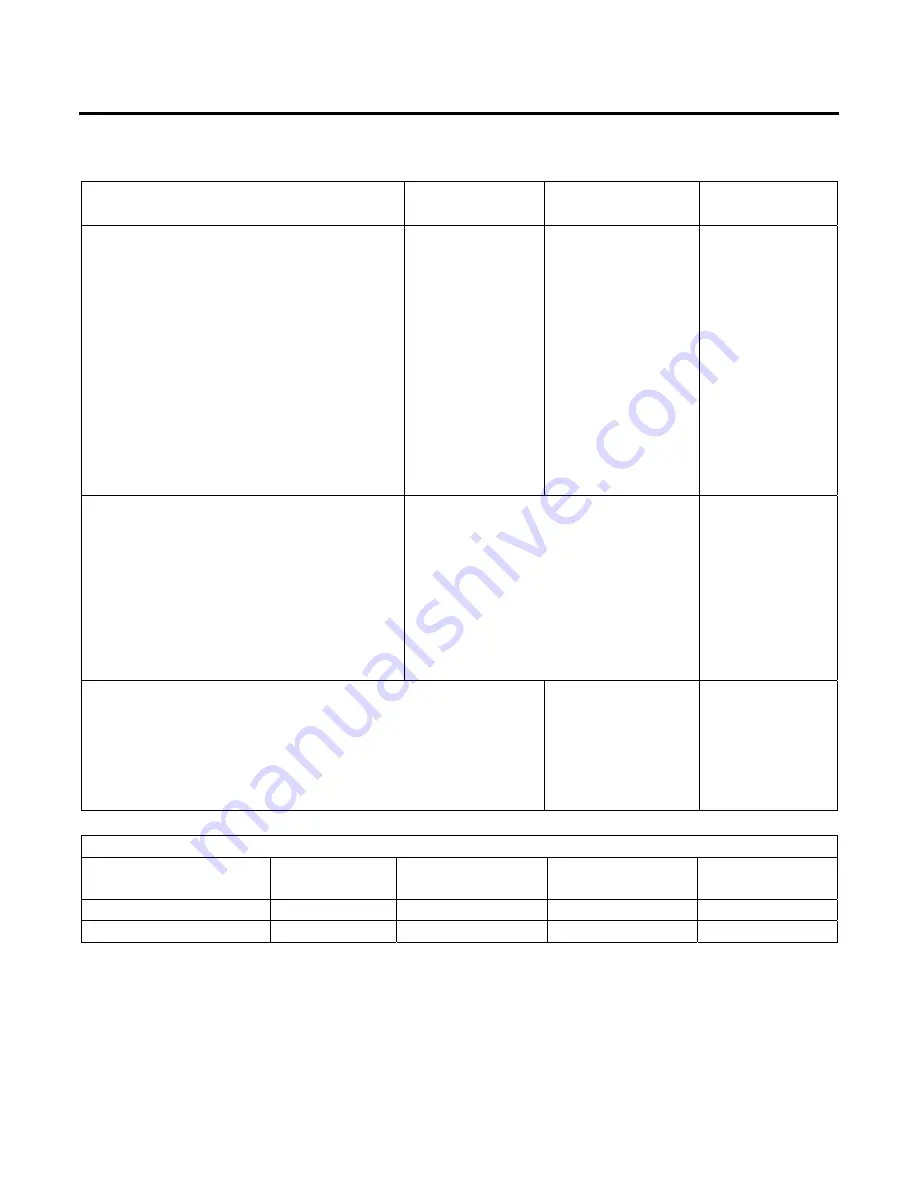
- 9 -
Installation
Typical Motor Control Settings
Alarm
Trip
(Shutdown)
Timer Trip
Setting
(1)
Winding Temperature
•
Class B Insulation
•
Class F Insulation
130°C
155°C
155°C
170°C
Motor Bearing Temperature
(Thermocouple or RTD’s)
•
Sleeve Bearing
100
°C
105
°C
•
Antifriction Bearing
100°C 105°C
Ground Fault
4 Amps
(2)
Primary
Circuit
8 Amps
(2)
Primary
Circuit
0.2 sec.
(2)
Instantaneous Overcurrent
•
With ½ Cycle Delay
1.8 times Locked Rotor Amps
(2)
•
Without Time Delay
2.4 times Locked Rotor Amps
(2)
Maximum Voltage
110 % of Rated Voltage
10 sec.
Minimum Voltage
(the minimum voltage
also applies to starting unless otherwise
specified)
90 % of Rated Voltage
10 sec.
Maximum Frequency Deviation
±5%
10 sec.
Maximum of Voltage Plus Frequency Deviation
±10%
10 sec.
Maximum Voltage Unbalance
(3)
1%
15
sec.
Maximum Current Unbalance
(3)
8%
15
sec.
Suggested Vibration Limits
RPM 3600
1800 1200
900
and
Slower
Shaft (mils, pk-to-pk)
3.3
3.7
4.3
5.0
Housing (in./sec.)
0.25
0.25
0.25
0.25
(1)
Maximum time at maximum condition before control device is to operate.
(2)
Increase as necessary to avoid nuisance trips.
(3)
This is the maximum deviation from the average of the three phases.
Summary of Contents for HiPath 500
Page 26: ... 25 ...