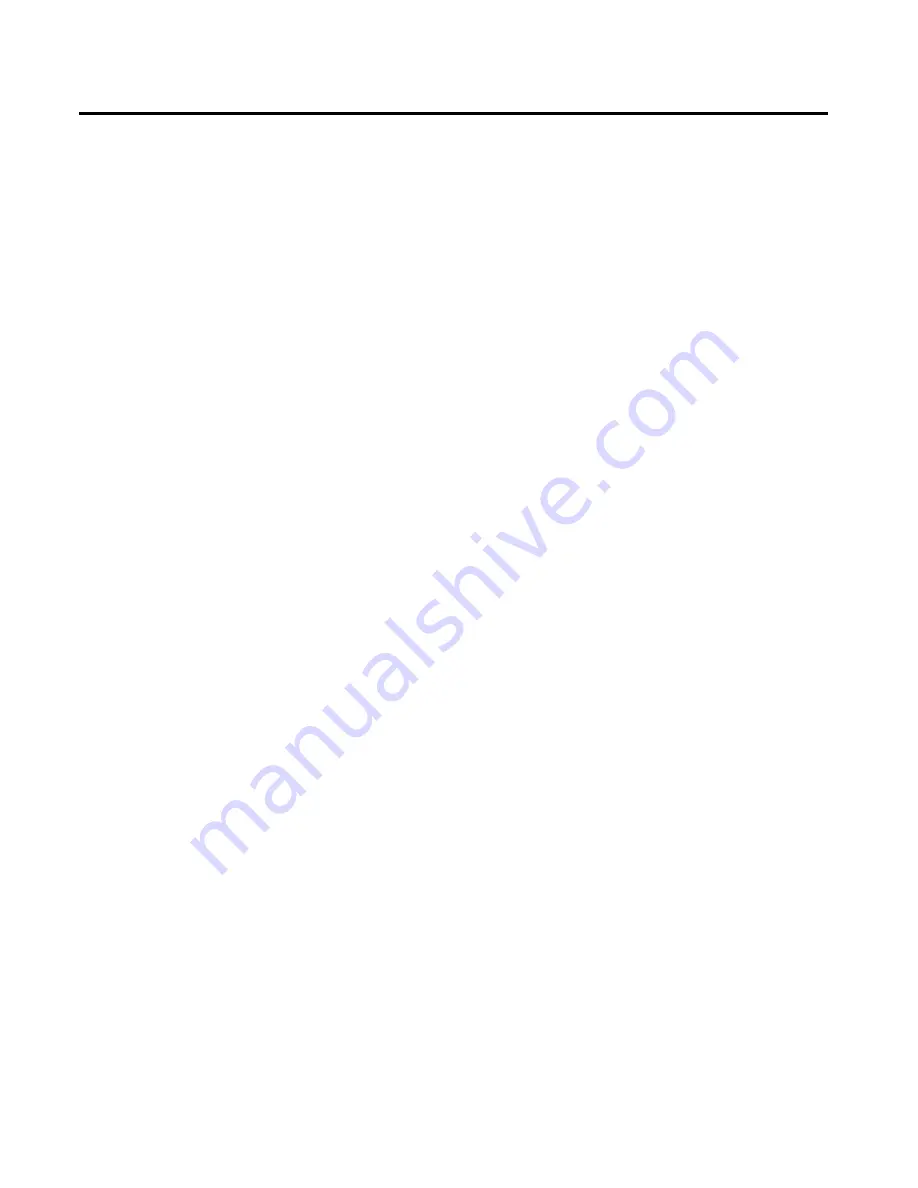
- 18 -
Maintenance
Insulated Bearings
One or both bearings may be insulated to prevent
shaft currents from pitting bearing surfaces. The
insulation is located at the joint between the bearing
housing or bracket and the bearing. Insulated
bearings are designated by an instruction plate on
the bearing housing.
Check periodically to be sure the insulation has not
been weakened or destroyed.
The bearing insulation can be checked using an
ohmmeter or circuit test light. For sleeve bearing
motors with one bearing insulated, the shaft must be
raised a few mils at the non-drive end of the motor so
that it is not in contact with the bearing and the shaft
coupling must be parted so that the shaft is not
grounded through the driven equipment. For motors
with both bearings insulated, disconnect bearing
grounding strap before testing for insulation integrity.
Bearing temperature devices must be disconnected
and oil rings must not be in contact with both the
shaft and the bearing.
Antifriction Bearings
Antifriction bearings are selected to give long service
when they are given proper maintenance. Bearing
failure can be caused by too little or too much
lubrication, contamination, excessive bearing load,
improper installation, alignment, or vibration.
The symptoms of antifriction bearing failure are
excessive vibration, noise, and excessive heat
generation. The races and balls should be
periodically inspected for damage. Any damage
requires replacement of the bearing.
Sleeve Bearings
Check sleeve bearings daily to be sure the oil rings
are turning properly. See motor outline drawing to
determine proper oil level. Add oil through the oil ring
sight glass opening or oil inlet pipe, if so equipped.
Be careful not to overfill.
Drain the oil reservoir by removing pipe plug. Clean
and flush with solvent and refill with fresh filtered oil
every three months to one year, depending on
severity of service. Use a high grade turbine oil
having a viscosity of 300-350 SSU at 100°F for units
of 1800 rpm and lower, and 140-160 SSU at 100°F
for machines above 1800 rpm to 3600 rpm.
In addition, seasonal oil changes are desirable if unit
is subject to wide variations in temperature.
Bearing babbitt temperatures that exceed 90°C
(194°F) or a sudden rise in temperature should be
investigated.
Common causes of hot bearings are:
1. Lack of oil.
2. Incorrect
viscosity.
3. Poor quality oil.
4. Inoperative oil ring.
5. Misalignment of couplings or bearings.
6. Insufficient bearing clearance.
7. Oil seal rubbing on shaft.
8. Shaft or bushing rough spots.
9. Plugged oil passages on circulating oil systems.
(Note that circulating oil systems include a filter in
the oil line to strain the oil after it leaves the
pump. Check and clean or replace filter when
necessary.)
10. End thrust on bearing face.
Sleeve bearings are bored to an even dimension and
shaft journals are slightly smaller to obtain running
clearance. Side reliefs are provided to distribute oil
axially and reduce friction. During normal operation,
the shaft is supported on an oil film 0.001 to 0.005
inch thick, depending on speed, load and viscosity.
Unless adverse conditions exist which tend to break
down the oil film, metallic contact occurs only during
starting and stopping. Under normal circumstances,
bearing wear is very small.
Oil Rings
Inspect oil level and oil ring operation frequently. Oil
ring operation can be observed through the oil sight
glass. Oil rings should be perfectly round, free of
burrs or rough edges, turn at a constant speed, and
carry a noticeable amount of oil to the top of the
bearing journal. Failure of the oil ring to turn freely
may be caused by:
1. Ring out of round - rings should be round within
0.062 inch.
2. Fouling on a projection of the bearings, bushing,
or housing.
3. Ring not balanced (heavy side will tend to remain
down).
4. Adhesion to guide slot (trapezoidal section
reduces adhesion).
5. Oil too cold, too viscous, or oil level too high.
6. Shaft not level – oil rings tend to bind.
7. Vibration causing oil ring to bounce and slow
down.