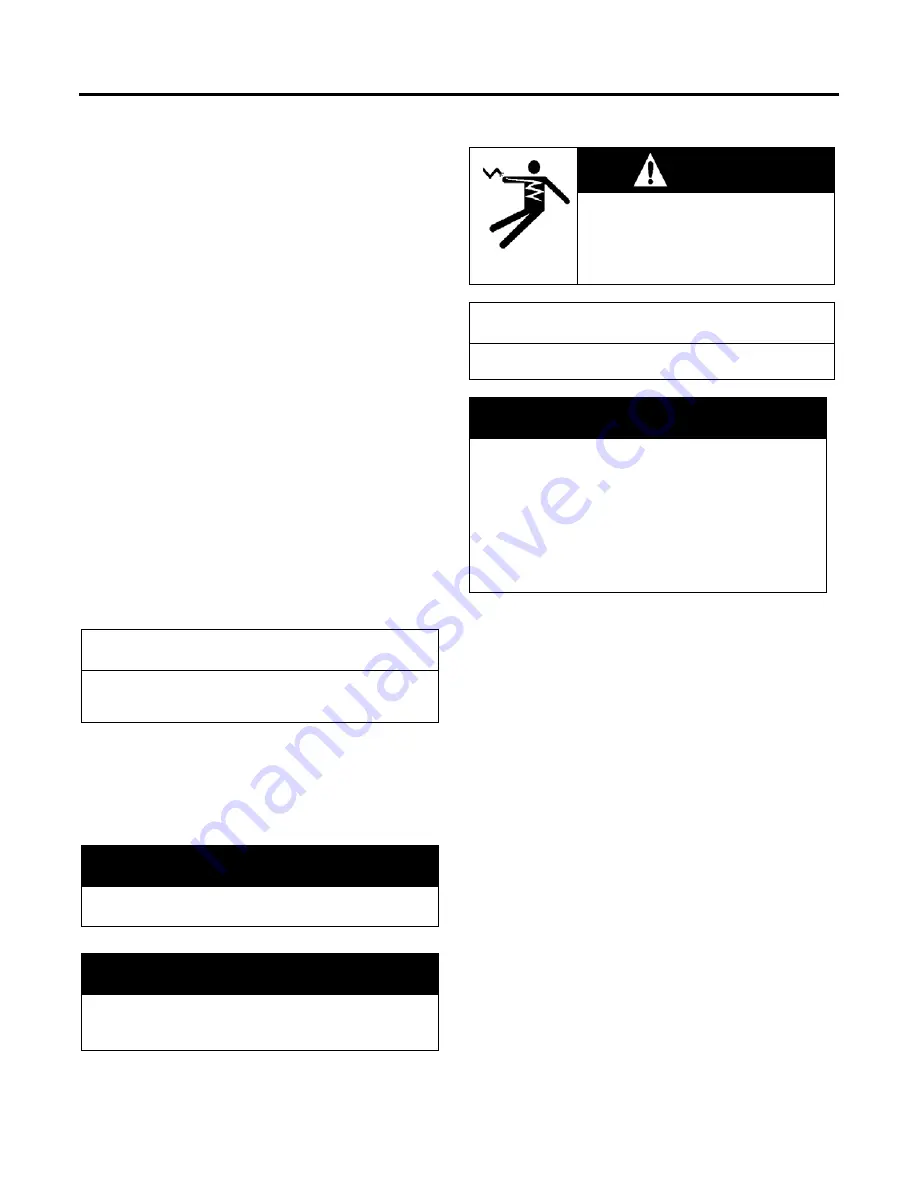
- 6 -
Installation
Hollow Shaft Motors
The motor should be set on its base first, and the
driven shaft inserted through the hollow shaft. There
are times, however, when these motors are lifted and
lowered over the driven shaft. In either case, do not
cause damage to the shaft by bending or scraping the
threads.
Proceed as follows:
1. Remove coupling cover and raise motor with sling
and hoist.
2. Slowly lower motor; carefully engage stud ( if
used) and rabbet. (Position motor to allow access
for power connection and lubrication.) Install
flange nuts (bolts, if used) and snug.
3. Insert pump drive shaft into hollow shaft; arrange
coupling and driven shaft in line with Gib Key Slot.
4. Insert Gib Key, connect driven shaft to coupling
and adjust pump nut for proper impeller clearance.
(Remove Locking Bar if provided.)
5. Turn shaft by hand to check for free rotation and
shaft alignment. There must be no binding,
scraping, or sticking.
6. If used, check the operation of the non-reverse
device: also check action of self-release coupling,
if that type of coupling is used (see Figure 12).
NOTE
A self-release coupling is shipped with three bolts
holding it in place. These bolts must be removed to
allow coupling to operate.
7. After alignment, uniformly and securely tighten all
flange nuts (bolts).
8. Turn shaft by hand again; check for free rotation.
9. Replace coupling cover.
CAUTION
Continuous upthrust may damage motors.
Eliminate upthrust before operating.
CAUTION
Improper lubrication can cause damage to bearings.
Check oil reservoir for proper oil grade and level before
stating or storing motor.
External Wiring
DANGER
Hazardous
voltage.
Will cause death, serious injury,
electrocution or property damage.
Disconnect all power before working on
this equipment.
NOTE
Before running motor, see
Initial
Start
in Operation
Section
.
CAUTION
FOR MOTORS EQUIPPED WITH BACKSTOP OR
NON-REVERSE DEVICE
Attempting to rotate motor with non-reverse device
in wrong direction may result in severe damage to
the motor.
Connect power supply phases to motor terminals exactly
as indicated on motor nameplate to insure proper
direction of rotation. Any other connection will result in
wrong direction of rotation.
Starting and overload control devices must be matched
to motor rating. For safety or convenience they may
need to be installed some distance from the motor.
Follow the control manufacturer’s instructions to make
proper installations and connections. Observe the
following:
1. Connect electrical power supply to conform to
National Electric Code and any local regulations.
Line voltage and wire capacity must match motor
rating stamped on the nameplate.
2. With the driven equipment disconnected,
momentarily energize the motor to check rotation.
3. If motor is three-phase type, reverse rotation (if
required) by interchanging any two of the three
power leads.
Summary of Contents for CAZBHS
Page 25: ... 24 Maintenance UPPER BEARING ARRANGEMENTS Figure 7 Figure 8 ...
Page 26: ... 25 Maintenance LOWER BEARING ARRANGEMENTS Figure 9 Figure 10 Figure 11 ...
Page 27: ... 26 Maintenance Self Release Coupling Arrangement At Top Of Motor Figure 12 ...
Page 30: ... 29 Spare Parts Figure 16 ...
Page 31: ... 30 Spare Parts Figure 17 ...
Page 32: ... 31 Spare Parts Figure 18 ...
Page 33: ... 32 Spare Parts Figure 19 ...
Page 34: ... 33 Spare Parts Figure 20 ...