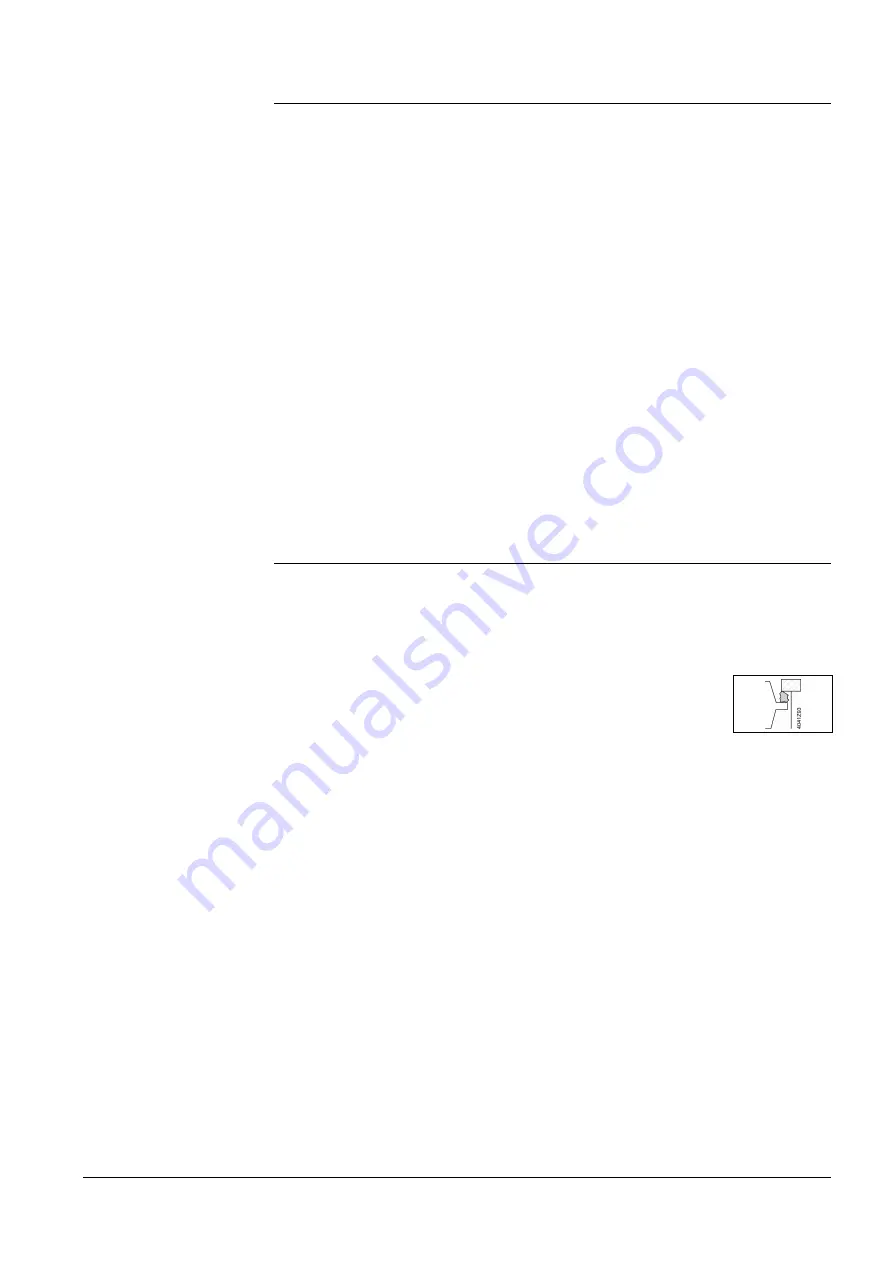
35 / 60
Siemens
Actuators SAS.., SAT.. for valves
CE1P4041en
Smart Infrastructure
Functions
and control
2019-04-09
4.2.5
Detection of valve seat
The actuators feature force-dependent valve seat detection. After calibration, the
exact valve stroke is filed in the actuator’s memory.
If no force is built up in the calculated end position (e.g. in the event of temperature
effects for instance), the actuator continues to operate at a reduced positioning
speed until the nominal positioning force is restored. This ensures that the valve
always fully closes.
After a power failure, valve seat identification is not active – the actuators without
fail safe function define their stroke position on power resoration to be at 50%.
From now on, the actuator follows the positioning signal.
When the valve plug reaches its seat for the first time, the actuator readjusts its
stroke model.
The supposed position is 50%, Y = 2 V, the actuator travels 30% of the stored
valve stroke in the direction of "Actuator’s stem retracted".
If the actuator reaches the seat within this 30% travel, it interprets the position as
"Valve fully closed" and shifts the position of the valve’s stroke accordingly without
changing the extent of travel.
From now on, the actuator follows the changed valve stroke position.
This means: New position 0%, Y = 2 V, actuator travels 20% of the stored valve
stroke in the direction "Actuator’s stem extended".
4.2.6
Detection of foreign bodies
The actuator detects when the valve is clogged and adjusts its operational behavior
accordingly to prevent damage to itself or the valve.
If the actuator hits an obstacle within the calibrated stroke and is not able to
overcome it with its nominal positioning force, it stores the position at which the
obstacle was hit. Depending on the direction of travel, as …
"Upper limit of valve clogging", if the clogging was detected when
traveling in the direction of "Actuator’s stem extending".
Now, the status LED blinks red and the actuator only follows the positioning signal
between the positions "Actuator’s stem retracted" and "Lower limit of valve
clogging".
After detection of clogging, 3 attempts are made to overcome clogging by traveling
about 15% in the opposite direction and then trying again to overcome the position
of clogging. If the attempts made are unsuccessful, the actuator continues to follow
the positioning signal within the restricted range only and the LED continues to
blink red (see "Status indication " page 43).
SAS..
Example