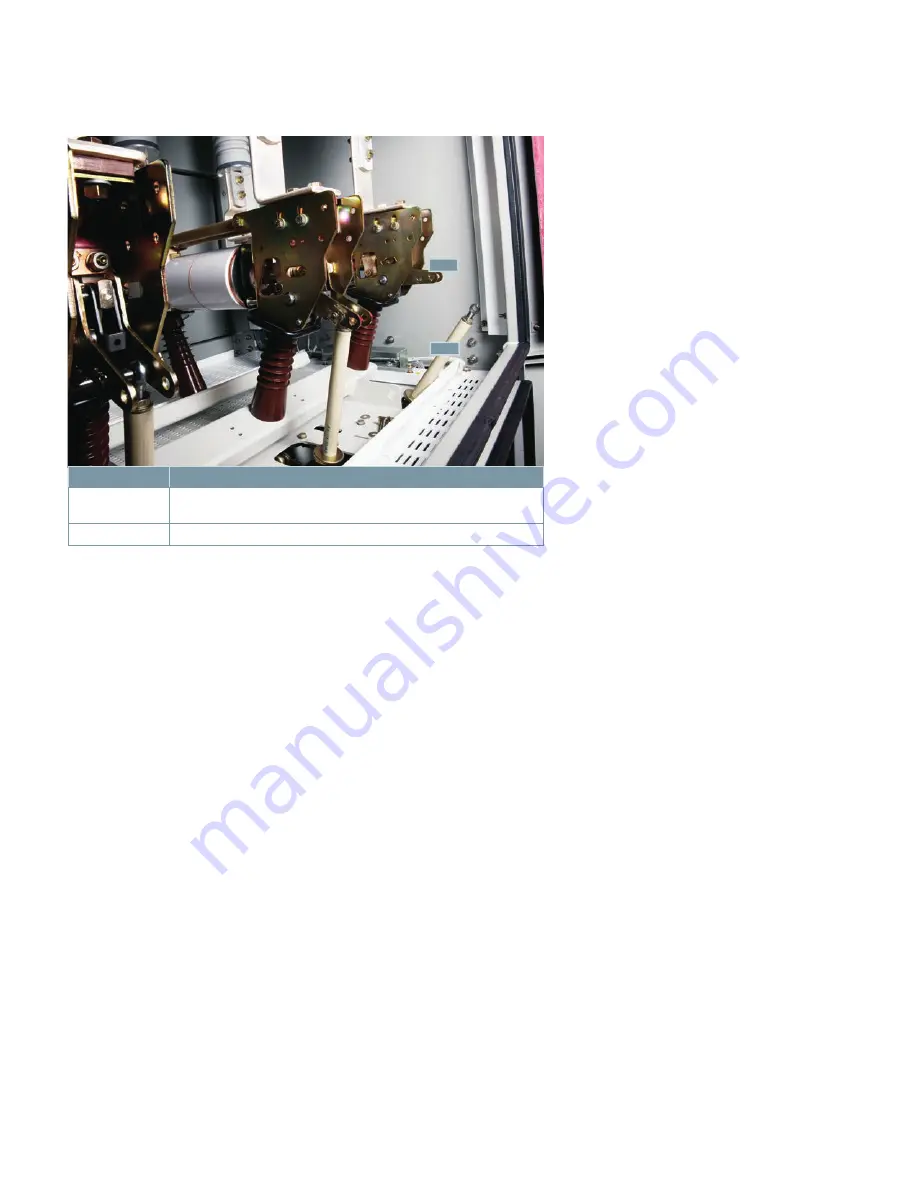
34
Figure 19: Manual check of vacuum integrity
48.0
Identification
Description
48.0
Insulating coupler (shown disconnected on right pole for checking
vacuum integrity)
48.6
Lever
Insulation and contact-resistance test
procedure
1. Observe safety precaution listed in the
danger and warning advisories for the
vacuum integrity check tests (refer to
pages 31-32).
2. Close the circuit breaker. Ground the
frame of the circuit breaker, and ground
each pole not under test. Use manual
charging, closing and tripping procedures.
3. Apply the proper ac or dc (refer to Table 4:
High-potential test voltages on page 33)
high-potential test voltage between a
primary conductor of the pole and ground
for one minute.
4. If no disruptive discharge occurs, the
insulation system is satisfactory.
5. After test, ground both ends and the
middle of each vacuum interrupter to
dissipate any static charge.
6. Disconnect the leads to the spring-
charging motor.
7. Disconnect secondary circuits for the
operating mechanism by disconnecting
the multiple pin-plug at the lower left
corner of the operator, and connect all
pins on the operator side with a shorting
wire. Connect the shorting wire to the
high-potential lead of the high-voltage
tester, and ground the circuit breaker
housing. Starting with zero voltage,
gradually increase the test voltage to
1,500 volts rms, 60 Hz. Maintain test
voltage for one minute.
8. If no disruptive discharge occurs, the
secondary control insulation level is
satisfactory.
9. Disconnect the shorting wire, reattach the
multiple pin-plug and reattach the leads
to the spring-charging motor.
10. Perform contact-resistance tests of the
primary contacts. The resistance should
be determined between the fixed-end
connection pad and the moving-end
connection pad (refer to Figure 5: Pole
assembly on page 11). Contact resistance
should not exceed the values listed in
Table 5: Maximum contact resistance on
page 35.
48.6
Summary of Contents for 3AH35-SE Series
Page 46: ...46 Table 13 Remarks ...
Page 47: ...47 Table 13 Remarks continued ...