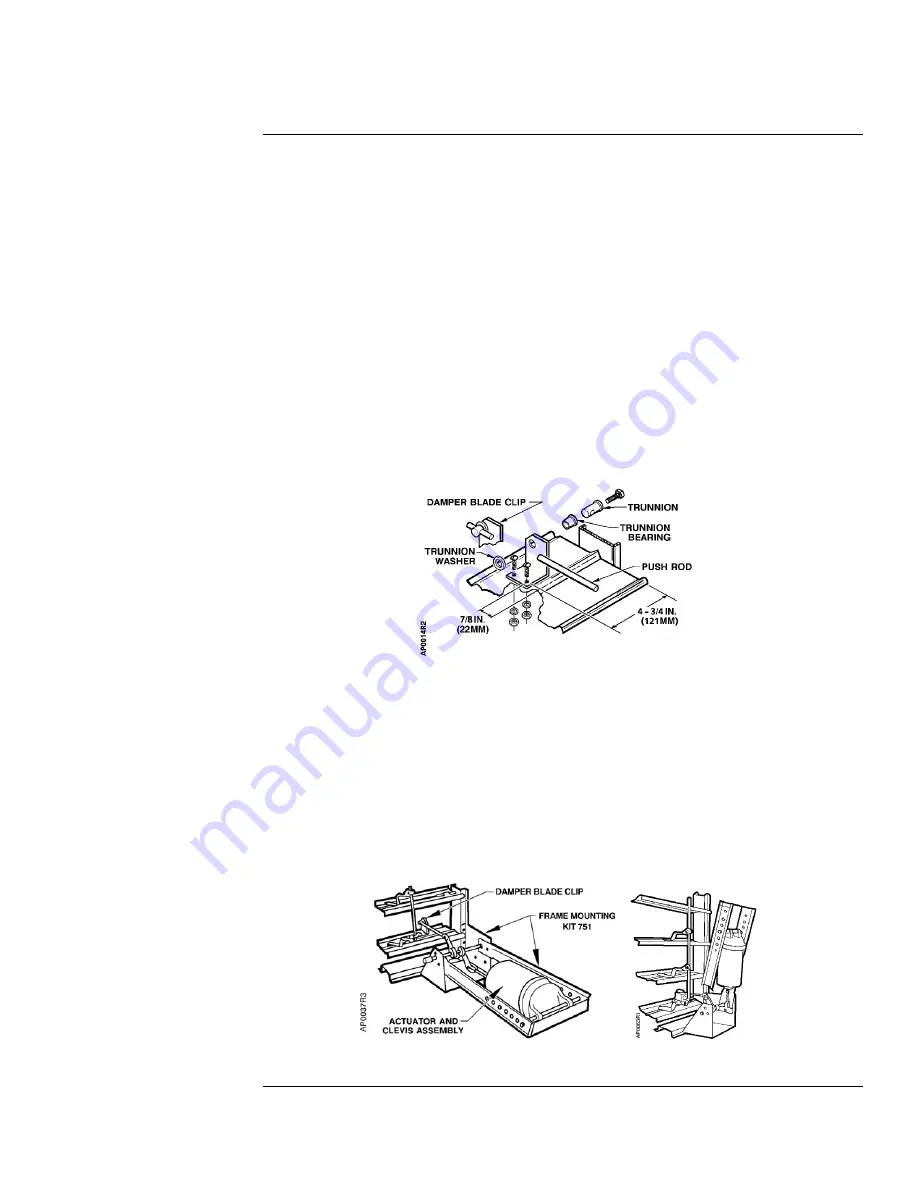
POWERS™ Controls No. 6 Pneumatic Damper Actuator
Technical Instructions
Document No. 155-029P25
December 3, 2004
One-Section Damper
Kit 751
See Figure 4 and
Figure 5
1. Attach the damper mounting bracket to the lower right-hand corner (or upper
left-hand corner if necessary) of the damper section with the six screws provided.
For Arrow United Industries 1770 dampers, add the shim provided between the
bracket and bottom of the frame. Have the damper manufacturer drill the holes in the
damper frame (Figure 5).
2. Have the damper manufacturer drill the holes in the damper blade for the blade clips
(Figure 4). Use the same clip location for both normally open and normally closed
dampers. Attach the damper blade clip to the damper blade (Figure 4). Put the
damper in its normal position, open or closed. Connect the push rod to the trunnion
in the blade clip and tighten the setscrew. Connect the other end of the push rod to
the crank on the drive shaft and tighten the trunnion setscrew on the push rod.
Position the crank so the push rod is parallel to the bracket, then tighten the crank
setscrews.
3. lnstall the actuator in the actuator support bracket using the pivot shaft and hitch
pins. The pivot shaft should be in the holes about 17-1/2 inch (445 mm) from the
drive shaft. The actuator support bracket can also mount in the vertical position for
installations where space is limited.
Figure 4. Damper Blade Clip.
4. Position the crank driven by the actuator as follows:
a. Normally open damper: the crank is above the drive shaft.
b. Normally closed damper: the crank is below the drive shaft.
5. Connect the actuator clevis to the crank. Put the damper in its normal position, open
or closed. Stroke the actuator 1/4-inch (6 mm) with a hand pump, then tighten the
crank setscrews. This will ensure tight damper closure.
Figure 5. One-section Damper.
Siemens Building Technologies, Inc.
Page 7