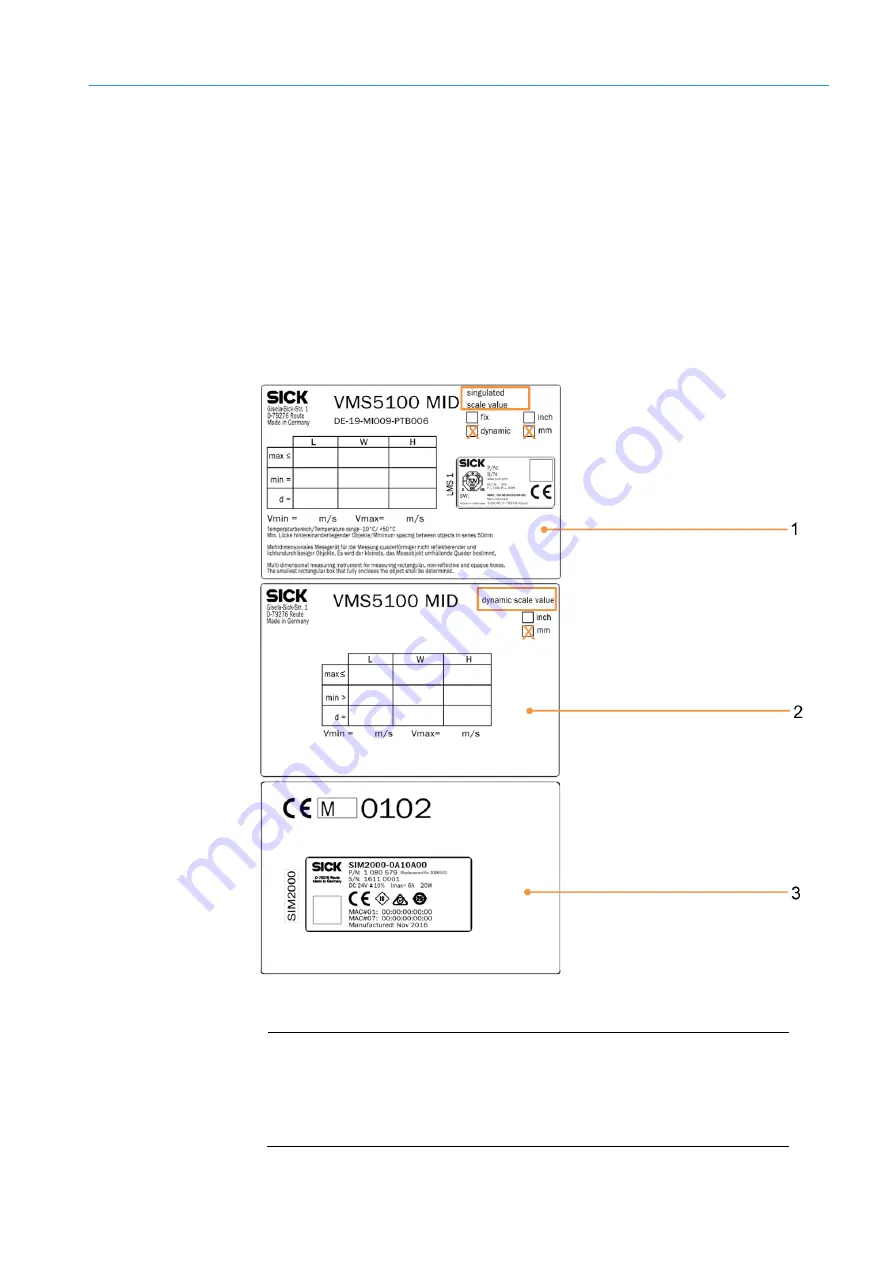
SYSTEM DESCRIPTION
3
45
8023994-17I6/2020-03-19|SICK
Subject to change without notice
O R I G I N A L O P E R A T I N G I N S T R U C T I O N S | VMS4100/5100
For dynamic scale value switchover, the scale values for two scale interval values used
must be described in two separate information labels and attached to the system
indelibly.
For scale interval value 1, use the information label for the relevant operating mode
(
Singulated
or
Touching/Side-by-Side
). The
dynamic
scale value and the measuring unit
(
mm
or
inch
) with the accompanying dimensional values must be specified on the
appropriate information label in indelible ink. The LMS4xxx type label must also be affixed
to this information label.
On the information label for scale interval value 2, the measuring unit (
mm
or
inch
)
with the accompanying dimensional values must be specified.
The type label for the SIM2000 system controller must be affixed to the metrology
information label in the appropriate field.
Fig. 39: MID - information labels for the VMS5100 in “Singulated” operating mode with dynamic
scale value switchover and affixed type labels
Legend
1
Identification label for scale interval value 1
(for “Singulated” operating mode)
2
Identification label for scale interval value 2
3
Metrology information label with affixed type label
Information labels with
dynamic scale value
switchover