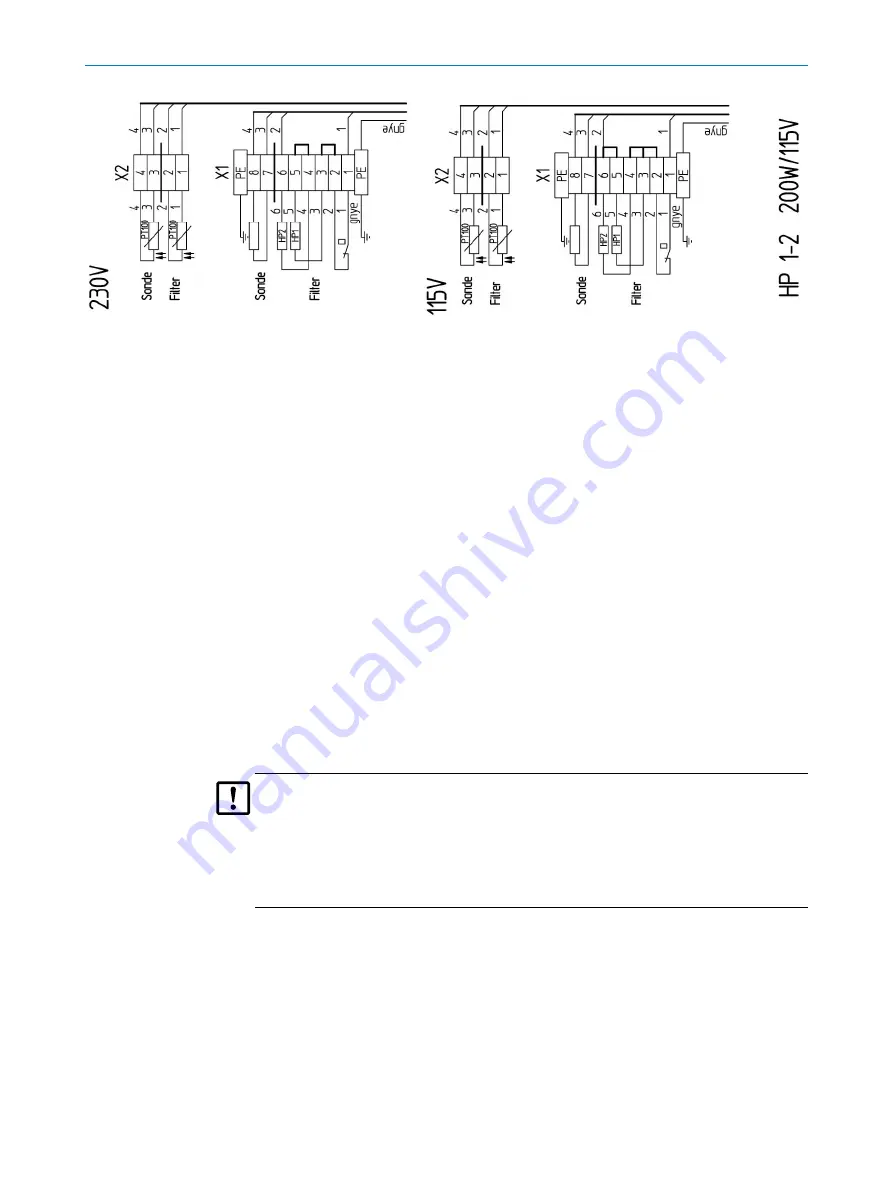
Figure 11: Terminal diagram for 230 V and 115 V
The electrical connection of the gas sampling unit is made via the connection terminals
on the installation plate.
Observe the terminal diagram on the SFU.
The temperature sensors and the heating cartridges are wired ex factory.
b
Remove the enclosure.
b
Perform electrical connections.
4.6
Installing the gas sampling tube on the gas sampling unit
Installing the gas sampling tube
The gas sampling unit with gas sampling tube is supplied pre-assembled.
Installing the pre-filter
The pre-filter can be screwed to the gas sampling tube.
1
Wrap the thread with Teflon tape.
2
Screw the pre-filter onto the tip of the gas sampling tube. Tighten by hand with a
wrench.
4.7
Installing the SFU on the welding neck flange
NOTICE
Risk of contamination of the gas sampling unit
Do not install a cold gas sampling unit on the stack.
b
Allow the gas sampling unit to warm up before installing it on the welding neck
flange.
b
Warm-up time: Approx. 1.5 h at 25 °C ambient temperature
4
INSTALLATION AND START-UP
20
O P E R A T I N G I N S T R U C T I O N S | SFU
8023849/14SF/V1-1/2019-07 | SICK
Subject to change without notice